Curious...I have not seen this drum effect in my measurements, neither with my current design using the XT32, nor with the previous version using the Dayton EX30. I consistently have a peak at 4.2KHz, but tend to have a dip around 10kHz instead, and then it goes back up at 15kHz.
Was this the Nidaplast with the non-woven fabric on the surfaces? I've thought a few times in the past about trying it with fiberglass or carbon fiber skins, to get nice stiff structure with high efficiency, but hesitated since the minimum thickness is 5 mm and I feared such a panel would have to be very large to get down to , say 100 Hz.I eventually found the problem to be in the Albasia itself. I changed to Nidaplast/PVA/Resin, and I'm getting better curves even with the soft, thick tape.
So you have covered it with PVA and then resin, without any fibers? What resin (epoxy?) Why PVA and resin? Does this combination stiffen the panel? What is the idea behind this combination?
Thanks,
Eric
I did a test using CLD tape and it definitely looks like an improvement. I used this 2" wide tape: https://www.amazon.com/dp/B093QCQS9C
The panel is ~10"x22"x0.75" XPS @ ~24kg/m3 with a heavy coating of undiluted PVA on both sides. The short top and bottom sides are clamped tight in a wood frame and the long sides have a very light foam pad in the middle. The frame was about 2.5ft from my big TV and mic was 7ft away from panel.
I placed the tape along the short edges of the panel right next to the frame running across the full width. I figured this extra mass should have minimal impact as long as it is close to the firmly clamped edges.
I only tested this one panel which was already pretty heavily damped with undiluted PVA, but the results are pretty clear. I think this change will be even more dramatic for less damped panels. I'm sure more tuning can be done with the tape, I just did two quick tests.
To test this I did have to pull the frame out from its position and turn it to attach the tape, and then moved it back. The angle of the panel was certainly not perfect each time. We can see how the tape appears to have helped in many places but is not without side effects in other places.
After applying this tape I had to significantly reduce EQ'ing to get the curve flattest. Where I had -8 and -10 dB before I reduced those to ~-3dB because those corrections were no longer required.
Important note: it doesn't seem like there's any way to get this tape off the panel. Once applied it's permanent. If I pull hard it will either tear the foam or leave butyl behind.
REW data attached.
The panel is ~10"x22"x0.75" XPS @ ~24kg/m3 with a heavy coating of undiluted PVA on both sides. The short top and bottom sides are clamped tight in a wood frame and the long sides have a very light foam pad in the middle. The frame was about 2.5ft from my big TV and mic was 7ft away from panel.
I placed the tape along the short edges of the panel right next to the frame running across the full width. I figured this extra mass should have minimal impact as long as it is close to the firmly clamped edges.
I only tested this one panel which was already pretty heavily damped with undiluted PVA, but the results are pretty clear. I think this change will be even more dramatic for less damped panels. I'm sure more tuning can be done with the tape, I just did two quick tests.

To test this I did have to pull the frame out from its position and turn it to attach the tape, and then moved it back. The angle of the panel was certainly not perfect each time. We can see how the tape appears to have helped in many places but is not without side effects in other places.
After applying this tape I had to significantly reduce EQ'ing to get the curve flattest. Where I had -8 and -10 dB before I reduced those to ~-3dB because those corrections were no longer required.
Important note: it doesn't seem like there's any way to get this tape off the panel. Once applied it's permanent. If I pull hard it will either tear the foam or leave butyl behind.
REW data attached.
Attachments
Last edited:
Hi Saphire,
Interesting results, I may have to try this too. So it is just stuck to the back near the edge not used to suspend the panel itself? Did you notice much of a drop in sensitivity/output level?
The second picture of data I assume you had a sub working too as the output below 100Hz is far better than any panel I've seen.
Thanks for posting.
Interesting results, I may have to try this too. So it is just stuck to the back near the edge not used to suspend the panel itself? Did you notice much of a drop in sensitivity/output level?
The second picture of data I assume you had a sub working too as the output below 100Hz is far better than any panel I've seen.
Thanks for posting.
Hi Christian,What is "Albasia"?
Albasia is a very lightweight plywood. @twocents introduced me to it I think via @BurntCoil (?)
I've been testing a 3mm version.
The "drum effect" issue does make sense, I'll have to test for it. The best tests will be either to use a damping mass inside the VC cavity, but adhered to the Albasia, and not to the motor magnet. (I've been using a small acoustic foam disk inside the VC cavity, stuck to the motor magnet thinking the problem was cavity-resonance related. But it's not. It made no difference.)Some readings I had recently recalled me different sources of HF problems :
- the peaks like the one seen at about 10kHz with EPS for example which is called "drum effect". It is the central area that acts like a drum. The panel is like a dual cone speaker. When you changed from the XT32 to the DAEX25, the diameter was reduced so maybe that frequency pushed to a higher value. What I didn't have in mind before those readings it is before the peak, this drum effect has a dip but it seems it is not the one you detected. Is it?
Or,
To simply drill a 22mm hole in the Albasia itself, centred on the VC. Watch this space.
Yes I'm aware of this problem. And it's specifically because of Zenker's paper that I was able to identify the problem with the DAEX30HESF, which seems to warp and collapse at HF when driving an acoustically heavy surface.
- the second source of HF limitation is in the chain that transmits the force from the coil to the plate. The first element pointed in a B Zenker's paper is the stiffness of the coil former. He didn't described against which element this stiffness react to create a filter or a resonator. The tape or any glue is also in this chain acting like a stiffness and a damper. In this paper,
I was therefore a little intrigued when I saw his (Zenker's) XT32's using the same, thick, soft VHB tape as the Dayton drivers. My subsequent tests have shown little to no difference between ultra-thin tape, superglue, hot glue or 1mm VHB tape. But then I am driving fairly light-weight panels, less than 200kg/m3. The XT's are factory-measured on acrylic panels (1200kg/m3) whereas the Daytons are measured on foam board. Probably less than 100kg/m3.
This is interesting. I will definitely test for it.
- B Zenker recommands to make an impedance measurement with the panel laying on a support (a plan) with the magnet free. The frequency of the "accident" in the force chain appears as a small peak in the impedance curve where we are suppose to see only the coil inductance effect. To be tested maybe?
Hi Eric,Was this the Nidaplast with the non-woven fabric on the surfaces? I've thought a few times in the past about trying it with fiberglass or carbon fibre skins, to get nice stiff structure with high efficiency, but hesitated since the minimum thickness is 5 mm and I feared such a panel would have to be very large to get down to , say 100 Hz.
Yes, this was Nidaplast. A modified version...
A few years ago when I first started working with these panels, I'd originally used Nidaplast panels, 300mm x 900mm, skinned with 22gsm CF tissue and bonded with polyester resin. Both the NP and the CF are non-woven, and soak up A LOT of resin. This made it too heavy and far too stiff, and not too efficient because of the total mass/high density (290kg/m3) problem.
Here are comparisons:
5mm NP/CF/Resin, 300 x 900mm in red, and
10mm EPS/Kevlar/PVA, 300 x 900mm in blue.
In live comparisons, the EPS sounded better because it was LOUDER to my listeners (at a backyard barbeque including way too many beers. And simply proves that louder is always "better" to the inexperienced layman), but the EPS is not useable on stage because of the massive midrange, and lack of HF. The NP/CF composite was also not useable because of inefficiency.
So recently I've been messing around with framed canvases. I started out with fairly large panels, 500mmx 800mm, and with various inserts. I'd firstly tension the canvas slightly by running dowels on the insides all along the edges between the canvas and its frame, and then glue (with PVA) a test panel-insert onto the back of the canvas.So you have covered it with PVA and then resin, without any fibres? What resin (epoxy?) Why PVA and resin? Does this combination stiffen the panel? What is the idea behind this combination?
Thanks,
Eric
I've tested all kinds of stuff for inserts: EPS, plywood, Nidaplast, Twinwall, solid acrylic etc etc. This is where I picked up the problem of the Albasia 3mm ply dipping at 5k and peaking at 10khz. (The aural symptom of the 10kHz peak is weak but glassy highs, with high-hats that might be loud enough, but just sound very thin.) I might be tempted to use thicker Albasia in my next round.
After a lot of testing I've settled on 300mm x 400mm panels—just a bit smaller than A3 in size—and with a Nidaplast insert 270mm x 340mm in size, which results in a nice, high-compliance "surround" to the moving bits. The NP is glued to the canvas with diluted PVA. The canvas is damped top and bottom, on the short sides, with weather foam between the frame and the canvas.
I also coat the back of the NP with the same diluted PVA which stiffens it just a little. Not too much.
However, the NP is relatively soft by itself, and does not transmit HF well. Therefore I poke holes through the back layer of the NP where the driver is to be positioned, and fill up those holes with resin, which also results in a perfect surface for the driver to stick to.
Measured results: Nice, thick highs, very fat, round bass, but there's a midrange peak at 600hz, to do with either the panel dimensions or the critical frequency, not sure which, but a 40g weight, positioned correctly, seems to sort it out.
This is a no EQ measurement, no sub, measured indoors at 500mm.
So in effect, I have a high-density mounting spot for the driver and which extends through the NP to the front of the canvas, then a lower-density, less stiff panel area around the driver, with a light-weight, high-compliance surround to the frame which allows the NP panel a large excursion, but yet controlled.
I have not optimised for distortion yet. This is next on the cards.
Last edited:
Hi Andre, wow great results especially in the sub 100hz range on such a small panel. So is the Nidaplast you are using on the canvas skinned with CF or just the honeycomb itself, sorry I may have missed something. Do you use them with a single exciter and how does the sensitivity compare to EPS would you say?
I was going to experiment with adding pressure to certain points on the panel on the back to get rid of a broad peak around 400-500hz, I hadn't thought of localised weight instead.
Thanks for sharing,
I was going to experiment with adding pressure to certain points on the panel on the back to get rid of a broad peak around 400-500hz, I hadn't thought of localised weight instead.
Thanks for sharing,
It's just the honeycomb by itself. The tissue on the Nidaplast does form a little bit of stiffening if you apply PVA to it.is the Nidaplast you are using on the canvas skinned with CF or just the honeycomb itself
It's a single XT32-4.Do you use them with a single exciter and how does the sensitivity compare to EPS would you say?
EPS is a lot more sensitive, but only in the mid range. I have not tested yet using weights to counter this problem, but if you do get a flatter response using EPS then you might find that you've lost all the sensitivity that makes it attractive in some ways.
Canvas/Nidaplast/PVA/Resin.
Before n after.
Green no weight. Red, with weight.
The weight is here:
I've found that all panels I'm testing with seem to benefit from the weight in a similar position. This is just a steel washer. I need to test for higher/lower density weights, more spread out or more concentrated.
Last edited:
No sub in the test. That LF isn't so great though because I have some light foam wedged in the middle of the long sides, and no baffles. Frame clamp is very tight as well. I did that because it controlled the panel better in other tests and for general use I do have a sub that I cross this with. I got better LF from this same panel in this frame before with looser clamp and no long-side foam (no CLD here):Hi Saphire,
Interesting results, I may have to try this too. So it is just stuck to the back near the edge not used to suspend the panel itself? Did you notice much of a drop in sensitivity/output level?
The second picture of data I assume you had a sub working too as the output below 100Hz is far better than any panel I've seen.
Thanks for posting.
Using the CLD tape on the foam surface under the frame clamp makes sense, I just didn't want to pull it apart to get these test strips in there. Putting butyl rope in there probably has the same effect but is cheaper, though that may not cover as wide an area. I also don't know how much tape would be the right amount so I wanted easy access. I might try sticking some more on there just to see what happens, but if it goes poorly there's probably no way to recover the panel.
Hi Andre,It's just the honeycomb by itself. The tissue on the Nidaplast does form a little bit of stiffening if you apply PVA to it.
It's a single XT32-4.
EPS is a lot more sensitive, but only in the mid range. I have not tested yet using weights to counter this problem, but if you do get a flatter response using EPS then you might find that you've lost all the sensitivity that makes it attractive in some ways.
Canvas/Nidaplast/PVA/Resin.
Before n after.
Green no weight. Red, with weight.
View attachment 1314463
The weight is here:
View attachment 1314464
I've found that all panels I'm testing with seem to benefit from the weight in a similar position. This is just a steel washer. I need to test for higher/lower density weights, more spread out or more concentrated.
Your Nidaplast creation looks a lot like the Russian panel material (cell size/print through). I wouldn't be surprised if they also use this material.
https://whiskyrooms.world/room-art/tefra/
A question : Why don't you just eq the 600 Hz peak? It looks like the end result would be flatter (until aprox 900 Hz), and you wouldn't loose efficiency in the range where it counts most.
Greetings, Hans
That sounds like a good test of the drum effect concept. I'm a bit skeptical of the idea, as I wonder if the plastic voice coil and "foot" are stiff enough to constrain any moderately stiff panel sufficiently for such a thing to happen. I'm looking forward to your results.To simply drill a 22mm hole in the Albasia itself, centred on the VC. Watch this space.
I was thinking of other ways to test the idea. One would be to attach a small disk of panel material that is the same size as the voice coil diameter. If such an effect occurs I think it would really stand out, as it would be at the fundamental frequency of the circular panel (easily calculated by FEM) with no overlapping panel frequencies in the vicinity to confuse matters.
I recall doing some other tests that seemed to discount the idea, but I can't recall exactly what they were so take that with a huge grain of salt.
Did you source your Albasia locally? This is the first I've heard of it. I did not find any US sources in my initial search.
Your canvas/NP panel results do look good. How is the efficiency? I would not have expected it to be too good without stiff (say fg/epoxy) skins.
Eric
Last edited:
Yes, There's a local importer here. They sell truck-loads of the stuff to the building industry.Did you source your Albasia locally? This is the first I've heard of it. I did not find any US sources in my initial search.
From Gemini AI:
"Finding an Albasia supplier in the US can be tricky because Albasia trees are fast-growing and not native to the US. Most commercially available lumber comes from Southeast Asia. However, there are a few options to consider:
- Importers: Some US lumber companies import Albasia wood products like veneer. Try searching online for "Albasia lumber importer US" or contacting specialist hardwood distributors."
Thank you, the results are better than I expected, and they do sound very nice indeed. I especially like the fatness and roundness of the bass. The highs could be a few dB higher, but they're ok for now. The whole impression is of a warm, non-fatiguing, well-balanced sound with masses of detail.Your canvas/NP panel results do look good.
Efficiency is not much better or worse than any of the other materials I've tested. But I cannot do absolute measurements until I get either a decent oscilloscope or a USB mic. I will be using these same construction principles as described here in order to build slightly larger panels that wil handle four drivers to increase efficiency a bit. But, heads-up, the guys at XciteAudio have advised the following:How is the efficiency? I would not have expected it to be too good without stiff (say fg/epoxy) skins.
"... The sensitivity does not increase in the same way as conventional drivers, which has to do with the bending wave excitation on the panel and you can't find unlimited positions, which excite the different bending waves 100% correlated to each other..."
Apparently the maximum is around four drivers per single panel.
In any case, I will certainly have to increase stiffness on a larger panel anyway so that it does not flap around given the Xmax and Bl of four drivers. This might also increase efficiency slightly.
Last edited:
Thanks Hans.A question : Why don't you just eq the 600 Hz peak? It looks like the end result would be flatter (until aprox 900 Hz), and you wouldn't loose efficiency in the range where it counts most.
I want to stay away from EQ for hi-fi panels for the simple reason that "audiophiles" with "golden ears" will think that they can hear things that aren't actually there.
But for PA use I will make generous use of DSP EQ and get it ruler-flat if necessary. And it will probably sound better than the HiFi versions too except for the fact you can't tell an "audiophile" that a system is EQ'd without risking an apoplexy.
meaning that the drivers will hit Xmax much more readily, given a specific mechanical impedance, than with a single driver.given the Xmax and Bl of four drivers
I did a bunch more tests with CLD tape today and I found that sticking 1" wide strips along the long edges made things worse, but when I moved them in they brought some improvement. Adding a patch in the center of the panel also brought some improvement. It isn't perfect, there's some trouble that comes with them too, but overall the net is an improvement.
An interesting thing I noticed is that despite the increased mass of the panel the impulse response improved. The heaviest CLD application lowered the output by about 3-5db so maybe that contributes to faster impulse response, idk. I didn't try turning up the volume to bring the dB back up to the previous test's level, but in hindsight I should have tested that.
I also tested using butyl rope in the frame clamp. It worked about the same as the foam I had. It is harder to work with the butyl rope to make it smooth and flat. I had soft slow-return foam tape before and it was clamped pretty tight. The butyl, like the -compressed- foam strip, performed best with light compression. Just enough so that the washers on my bolts are snug enough to not rattle.
While reviewing my test results and trying to understand the data I realized I have no test to see if it's just the mass of the tape or the CLD action causing these effects. It's a combination obviously but how does each contribute? I haven't thought of anything I have that I can add as benign mass to do an A/B comparison.
I found today that I can removed the CLD tape without damage if I just peel it slowly at room temperature. The test panel was coated with heavy PVA and that held up. Other lighter coatings may not.
Here's the heaviest test I did which I later EQ'd and left in place for now:
It has the same wide top and bottom strips on the front side.
All tests done with panel frame 3ft from big TV and mic 7ft from panel in an untreated room. Same volume level set for every test, no sub or anything else. There was a good amount of household noise (appliances and kids) but I tried to keep it as clean as possible. Graphs combine 1/3 smoothing and 1/24.
Red is the panel without any CLD tape. Has middle foam on long LR sides.
Blue is the panel with heaviest CLD tape arrangement. Middle foam removed.
Purple is the Blue EQ'd real quick.
An interesting thing I noticed is that despite the increased mass of the panel the impulse response improved. The heaviest CLD application lowered the output by about 3-5db so maybe that contributes to faster impulse response, idk. I didn't try turning up the volume to bring the dB back up to the previous test's level, but in hindsight I should have tested that.
I also tested using butyl rope in the frame clamp. It worked about the same as the foam I had. It is harder to work with the butyl rope to make it smooth and flat. I had soft slow-return foam tape before and it was clamped pretty tight. The butyl, like the -compressed- foam strip, performed best with light compression. Just enough so that the washers on my bolts are snug enough to not rattle.
While reviewing my test results and trying to understand the data I realized I have no test to see if it's just the mass of the tape or the CLD action causing these effects. It's a combination obviously but how does each contribute? I haven't thought of anything I have that I can add as benign mass to do an A/B comparison.
I found today that I can removed the CLD tape without damage if I just peel it slowly at room temperature. The test panel was coated with heavy PVA and that held up. Other lighter coatings may not.
Here's the heaviest test I did which I later EQ'd and left in place for now:
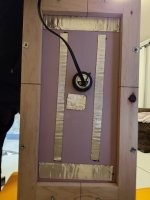
It has the same wide top and bottom strips on the front side.
All tests done with panel frame 3ft from big TV and mic 7ft from panel in an untreated room. Same volume level set for every test, no sub or anything else. There was a good amount of household noise (appliances and kids) but I tried to keep it as clean as possible. Graphs combine 1/3 smoothing and 1/24.
Red is the panel without any CLD tape. Has middle foam on long LR sides.
Blue is the panel with heaviest CLD tape arrangement. Middle foam removed.
Purple is the Blue EQ'd real quick.
Last edited:
I have been saying this for the last 15years, not that anyone takes any notice🙄I have been going for materials that re more flexible and sponge-like than butyl. I'm sure it dampens well, but the question is how much damping you want? I'm chasing high efficiency, but also like the sound of a less constrained plate as long as it not completely free to swing around. In my first attempts at constraining I had long strips at all sides, and found that the less contact I had the better the plates sounded and the more efficient they become.
I have only tested that on the GPS plates with four exciters in cluster though, and perhaps I'm overlooking some variables and have jumped to conclusions...am I the only one that experienced that minimal perimeter constraints both sounds best and is more efficient?
By the way, the peak at 10k would depend on the panel material used and its internal damping, some panels have very high peaks and some are buried below the response plot.
Your, main problem using multiple exciters on a panel is finding positions in which they to not fight with each other in the lower end, which causes damage and overheating.
Or even roll 1 or 2 off that are interfering with each other(this was a last minute thought 🤔)
I intend at some point to look into this problem for use on my proplex round flueted panels.
Until then I am just quessing as to curing this problem, so I will say no more.
Steve.
- Home
- Loudspeakers
- Full Range
- A Study of DMLs as a Full Range Speaker