I'm looking to buy a 3D printer to make PCBs and considereing an AnkerMake M5 but need to find PCB design software as the package I'm using, ExpressPCB does not allow exporting of a file suitable for printing.
So 3 questions.
1. can you recommend a free software package for PCB design; snothing fancy to design single sided baords is sufficient and would be useful to have a library of components: resistors, capacitores, pads and IC packages.
2. can you recommend a 3D printer - I'm sure that one I list above will do the job providing I can send to the PCB layour files (.dxf? .stl?) to it.
3. have you done this, what is your set up?
I so I'm going to have to look at an alternative.
So 3 questions.
1. can you recommend a free software package for PCB design; snothing fancy to design single sided baords is sufficient and would be useful to have a library of components: resistors, capacitores, pads and IC packages.
2. can you recommend a 3D printer - I'm sure that one I list above will do the job providing I can send to the PCB layour files (.dxf? .stl?) to it.
3. have you done this, what is your set up?
I so I'm going to have to look at an alternative.
I am struggling to imagine how the PCB would be made by a 3d printer. What's the material structure you are thinking of? I understand there are conductive filaments. Not sure about the fidelity of that sort of thing.
I can imagine a number of applications like supports to arrange multiple pcbs in the chassis and provide support for mezzanine layers, wire guides... anyone else got ideas for applications?
I can imagine a number of applications like supports to arrange multiple pcbs in the chassis and provide support for mezzanine layers, wire guides... anyone else got ideas for applications?
The idea is to print the mask, a thin layer of material onto the copper side then etch away the copper, then remove the printed layer.
Trust me, not worth the trouble. Jlcpcb, ends up cheaper, higher quality, plated trough pads and vias.
But if you want to put yourself trough the process, theres quite a few videos on youtube. General gist is, design a pcb in software of your choosing, export it as svg, import it into a 3d software. Extrude it to 0.1mm, export it as step, stp or whatever your resin printer slicer consumes, import, set to 40s duration exposure, add your plated copper plated board with uv sensitive film on top, and stick it to your plate (make sure you offset it for that much as to not break the screen), and shine away. Then you etch it, and enjoy your badly made pcb 😅 Speaking from experience, not even close to jlcpcb quality. I used mono 4k printer.
But if you want to put yourself trough the process, theres quite a few videos on youtube. General gist is, design a pcb in software of your choosing, export it as svg, import it into a 3d software. Extrude it to 0.1mm, export it as step, stp or whatever your resin printer slicer consumes, import, set to 40s duration exposure, add your plated copper plated board with uv sensitive film on top, and stick it to your plate (make sure you offset it for that much as to not break the screen), and shine away. Then you etch it, and enjoy your badly made pcb 😅 Speaking from experience, not even close to jlcpcb quality. I used mono 4k printer.
I am making small quantities, typically 1 of, not more than 5 at most and I want very quick turnaround, plus if there is a mistake, I would want to correct and remake it very quickly, so whilst the pricess on JLCPCB seem good, I don't want to wait that long. I did gather bits and pieces to make a UV light box but that project stalled as the glass plate, from a printer/scanner does not fit the box - if I were to go back to that, I wouldn't needn't a 3D printer as I have a laster printer that should be able to print onto transparency.
... anyway, n one of this is answering the original question about 3D printer.
... anyway, n one of this is answering the original question about 3D printer.
For smd, you pretty much need a resin printer with high resolution screen. For crude trough hole, you can use pretty much any filament one, and use uv light as you already half made. One you linked is more than good enough for that.
As for software, it follows procedure i wrote above. You can use easyeda, easy, free and online. For slicer, whatever comes with the printer.
Also, make sure you use black filament, it blocks UV well.
As for software, it follows procedure i wrote above. You can use easyeda, easy, free and online. For slicer, whatever comes with the printer.
Also, make sure you use black filament, it blocks UV well.
Not exactly the same way you described, but I use a 3d printer to fab PCBs at home.
I replaced the print head with a dremel extension like this: Dremel Flex Shaft Attachment. So, instead of printing and etching the PCB, I "machine" it - i.e., mill, drill, cut.
I use an Ender 3 V2 printer with a custom Marlin firmware. It takes a few tries to get used to it, but, with practice, you can even fab SMD two sided PCBs. I would say that the worst part is the software. You will have to deal with gcode files at the low level, understand code commands and customize/merge the files accordingly. You will break a few drill/mill bits until you get used to the process, but I find it great to create prototypes.
If you have a single sided pcb, you can program the printer to remove the copper (creating the tracks), drill the holes and cut the pcb using a single mill bit. Or you can use different drill/mill bits to acheive better finish. I currently prefer a 60 degrees 0.1mm v-shaped mill bit to cut the tracks, a flat mill bit (0.8mm) to remove copper and cut the board and one or more regular drill bits to... well... drill the holes.
I use FlatCAM to produce the gcode files from gerber files. Here is a picture of the v-shaped mill bit cutting the tracks:
This is not exactly what you asked, but it is an option to consider. Of course, all parts that you need to make it work were 3d printed.
I replaced the print head with a dremel extension like this: Dremel Flex Shaft Attachment. So, instead of printing and etching the PCB, I "machine" it - i.e., mill, drill, cut.
I use an Ender 3 V2 printer with a custom Marlin firmware. It takes a few tries to get used to it, but, with practice, you can even fab SMD two sided PCBs. I would say that the worst part is the software. You will have to deal with gcode files at the low level, understand code commands and customize/merge the files accordingly. You will break a few drill/mill bits until you get used to the process, but I find it great to create prototypes.
If you have a single sided pcb, you can program the printer to remove the copper (creating the tracks), drill the holes and cut the pcb using a single mill bit. Or you can use different drill/mill bits to acheive better finish. I currently prefer a 60 degrees 0.1mm v-shaped mill bit to cut the tracks, a flat mill bit (0.8mm) to remove copper and cut the board and one or more regular drill bits to... well... drill the holes.
I use FlatCAM to produce the gcode files from gerber files. Here is a picture of the v-shaped mill bit cutting the tracks:
This is not exactly what you asked, but it is an option to consider. Of course, all parts that you need to make it work were 3d printed.
Last edited:
A 3D printer is difficult, I think a laser engraver up to 2W will be more convenient. The board is simply painted, and then the unnecessary layer of paint is burned off with a laser, there is no need to burn metal, so the laser power is not needed high.
And if you take an engraver with the ability to replace the laser head with an engraving one, you can drill holes in the right places.
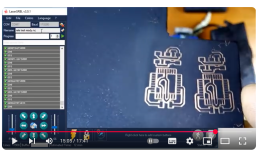
And if you take an engraver with the ability to replace the laser head with an engraving one, you can drill holes in the right places.
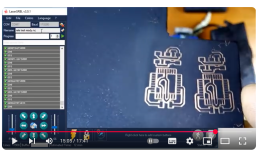
I'd be printing onto the PCB with a material chose to stick to the copper so etch directly; no need of UV.Also, make sure you use black filament, it blocks UV well.
Ah, that makes sense. Kind of funny that I did not consider that since I work in Lithography.The idea is to print the mask, a thin layer of material onto the copper side then etch away the copper, then remove the printed layer.
UV is preferred because it is the king of anisotropy.
You can use an SLA 3D printer for UV PCBs -
https://www.eevblog.com/forum/eda/m...-easy-66mil-pcbs-exposed-with-an-sla-printer/
The best diy UV PCB exposer is probably the AlphaCrow HLDI design
using the guts of an old inkjet printer and a 405nm UV LED.
You can use it to expose dry film photoresist coated PCBs
for etching and also UV curable solder mask. Excellent results.
There is a huge thread on the Russian radiokot forum.
Short video of HLDI -
A longer, detailed one (I use youtube autotranslate - works well)
https://radiokot.ru/forum/viewtopic.php?f=8&t=119089
https://www.eevblog.com/forum/eda/m...-easy-66mil-pcbs-exposed-with-an-sla-printer/
The best diy UV PCB exposer is probably the AlphaCrow HLDI design
using the guts of an old inkjet printer and a 405nm UV LED.
You can use it to expose dry film photoresist coated PCBs
for etching and also UV curable solder mask. Excellent results.
There is a huge thread on the Russian radiokot forum.
Short video of HLDI -
A longer, detailed one (I use youtube autotranslate - works well)
https://radiokot.ru/forum/viewtopic.php?f=8&t=119089
- Home
- Design & Build
- Equipment & Tools
- 3D printer to make PCB