I recently had a project fail and it appears to be because of the soldering paste used during construction. The circuit failed the second time out and investigation showed it was badly corroded at every place I had used MG Chemicals No Clean Flux Paste. I was using it with a soldering wick to wick up excess solder. The corrosion was bad enough to short a supply rail under one chip, compromise all the traces under another and take the tinning off in multiple spots.
I obviously need a few pointers on a good solder flux and a cleaner. The stuff says 'No Clean' but apparently this isn't the case. I've seen this before when using something called Orange Crush which is why I tried this other stuff.
Most of my work is hand soldered surface mount. What does everybody use as a soldering flux?
I obviously need a few pointers on a good solder flux and a cleaner. The stuff says 'No Clean' but apparently this isn't the case. I've seen this before when using something called Orange Crush which is why I tried this other stuff.
Most of my work is hand soldered surface mount. What does everybody use as a soldering flux?
If it doesn't specify use as electronic soldering, never use it. Fluxes used for plumbing and other types of metal joining can be extremely corrosive as you found out.
I don't trust the "no-clean" ad copy. I use isopropyl alcohol from the drug store and an old toothbrush. SMD might require a pressure spray or a good soak, which includes some forethought before stuffing sensitive parts.
I prefer corrosive, conductive, water soluble flux whenever practical.
It just plain works better, and no solvent odors or hazards.
Obviously you don't ever want to use anything corrosive where it can't
be thoroughly rinsed or can't be baked dry afterward. And I do mean
you must "drown it", in the hottest clean water you can stand to touch..
Dabbing at the top with alcohol does nothing for the real problem
underneath. Baking a corrosive flux "dry" doesn't work long either,
cause it soaks up new water from the air, and becomes wet again.
Alcohol is OK (except for the enamel on inductors), but you have
to use a totally unreasonable amount of it to totally wash away the
problem when we speak of corrosive fluxes. Water is cheap, use it...
Mixing flux types results in a conductive corrosive mess that can't
be washed away in plain water... You are gonna need LOTS of alc.
The danger in any rework is the prior no-clean residue gets mixed
with new corrosive flux and won't wash away...
It just plain works better, and no solvent odors or hazards.
Obviously you don't ever want to use anything corrosive where it can't
be thoroughly rinsed or can't be baked dry afterward. And I do mean
you must "drown it", in the hottest clean water you can stand to touch..
Dabbing at the top with alcohol does nothing for the real problem
underneath. Baking a corrosive flux "dry" doesn't work long either,
cause it soaks up new water from the air, and becomes wet again.
Alcohol is OK (except for the enamel on inductors), but you have
to use a totally unreasonable amount of it to totally wash away the
problem when we speak of corrosive fluxes. Water is cheap, use it...
Mixing flux types results in a conductive corrosive mess that can't
be washed away in plain water... You are gonna need LOTS of alc.
The danger in any rework is the prior no-clean residue gets mixed
with new corrosive flux and won't wash away...
Last edited:
I would not recommend using gasoline on electronics assemblies.
No clean flux is a bit of a myth, unless you are making cheep electronics that will be skipped in a few months, it is always recommended to clean flux off.
No clean flux is a bit of a myth, unless you are making cheep electronics that will be skipped in a few months, it is always recommended to clean flux off.
What sort of project was this??
Point-to-point or PCB or surface mount stuff??
Don't use Gasoline. For a petroleum product Naptha might work, but they are dangerous to use and Gasoline leaves residues.
_-_-
Point-to-point or PCB or surface mount stuff??
Don't use Gasoline. For a petroleum product Naptha might work, but they are dangerous to use and Gasoline leaves residues.
_-_-
What sort of project was this??
Point-to-point or PCB or surface mount stuff??
Don't use Gasoline. For a petroleum product Naptha might work, but they are dangerous to use and Gasoline leaves residues.
_-_-
It's an audio mixer used with two transceivers. The PCB is a small double sided board primarily surface mount with a a few through hole components. This solder paste is sold for use with electronic components. In one of the pictures taken through a magnifying glass (not a good photo sorry) you can see some of the corrosion. It was bad enough underneath a couple chips to compromise the circuit. The odd thing is, the flux residue exists in all the pic's. It was on the board for weeks with no problems until it was used in the field. It only seems to have caused a problem where I used it with a solder wick.
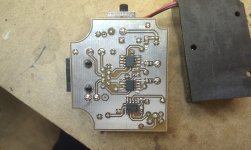
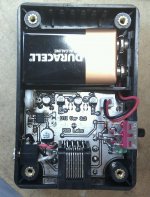
![DSCF0248[1].jpg DSCF0248[1].jpg](https://www.diyaudio.com/community/data/attachments/315/315158-f01f809f3ce338dba2ab22758f2a896c.jpg?hash=8B-AnzzjON)
> It only seems to have caused a problem where I used it with a solder wick.
Hate to repeat myself, but solder wick usually contains flux.
Hate to repeat myself, but solder wick usually contains flux.
I worked for a company where for a while they went the no clean flux way, until we got problems in hot humid areas of the world with failures. This was traced to the no clean flux becoming active in the heat and moisture...A few dollars later and every product went out of the door sparkingly clean. The IPC has had produced numerous reports on this problem., as have other assembly centric associations and mags.
Problem With No Clean Solder Flux Residue
Problem With No Clean Solder Flux Residue
Obviously there is a correlation between use of flux and corrosion, so 99% the problem comes from there.
As others said, don't believe the labels.
Personally I never clean flux residues and yet never had problems, but I have always used simple homemade flux: a "stone" of rosin dissolved in medical grade (94%) ethyl alcohol, simply because it's *guaranteed* to be pure with no nasty additives.
I keep it in an old jam/marmalade bottle, last batch was made 5 years ago and I still have it half full 🙂
Commercial fluxes often have "activators" which work wonders, but by definition attack copper, so need washing.
Pure pine or sap rosin does not.
That said, that PCB looks homemade.
If traces of etching chemicals remained, even a little can do a lot of damage if exposed to humid conditions so that's something to consider.
That PCB sits in a very tight, closed space, but in larger spaces (such as inside a TV or Guitar Amp, rat pee can have a terrible corrosive effect. No kidding.
Edit: I make my own PCBs; something I learned to do long ago, is to neutralize acid residues after etching, simply washing is not enough, doubly so in Phenolic PCBs which absorb moisture .
After etching and washing under running water I give it a last bath in a couple teaspoons of common household bicarbonate (a.k.a. baking soda in USA) into a liter/pint/quart of tap water, let it sit there for a few minutes and the wash again under a tap.
When dry (use heat or Sun to be certain) I brush copper shiny clean with steel wool and brush my homemade flux .... works like a charm and is very reliable.
Here's a batch of 36 100W power amp PCB air drying after flux spraying:
As others said, don't believe the labels.
Personally I never clean flux residues and yet never had problems, but I have always used simple homemade flux: a "stone" of rosin dissolved in medical grade (94%) ethyl alcohol, simply because it's *guaranteed* to be pure with no nasty additives.
I keep it in an old jam/marmalade bottle, last batch was made 5 years ago and I still have it half full 🙂
Commercial fluxes often have "activators" which work wonders, but by definition attack copper, so need washing.
Pure pine or sap rosin does not.
That said, that PCB looks homemade.
If traces of etching chemicals remained, even a little can do a lot of damage if exposed to humid conditions so that's something to consider.
That PCB sits in a very tight, closed space, but in larger spaces (such as inside a TV or Guitar Amp, rat pee can have a terrible corrosive effect. No kidding.
Edit: I make my own PCBs; something I learned to do long ago, is to neutralize acid residues after etching, simply washing is not enough, doubly so in Phenolic PCBs which absorb moisture .
After etching and washing under running water I give it a last bath in a couple teaspoons of common household bicarbonate (a.k.a. baking soda in USA) into a liter/pint/quart of tap water, let it sit there for a few minutes and the wash again under a tap.
When dry (use heat or Sun to be certain) I brush copper shiny clean with steel wool and brush my homemade flux .... works like a charm and is very reliable.
Here's a batch of 36 100W power amp PCB air drying after flux spraying:

Last edited:
Rosin contains several different acids. Resin acid - Wikipedia, the free encyclopedia There's nothing "pure" about it. Its just acid from a tree instead of from a factory.
I use some Kester liquid I have had for many years, cannot recall what the product number. I do wash the boards thoroughly, twice in 91% isopropyl, once in isopropanol, then in distilled water. I use a hair dryer to dry it with when I am done. never had an issue.
You are missing the point completely.🙄Rosin contains several different acids. Resin acid - Wikipedia, the free encyclopedia There's nothing "pure" about it. Its just acid from a tree instead of from a factory.
The rosin acids are active at soldering temperature, above 250ºC, and inactive at ambient temperature.😉
The "factory acids" , such as clorhidric acid, used to solder tin cans, etc. , are active at any temperature, and hygroscopic to boot, which multiplies the effect.😉
Comparing both on a same footing shows you have no clue about Chemistry.😀
And by "pure" I do not mean any esoteric , cosmic or ethereal quality, but "chemically" pure, meaning "nothing added". 😱
There must be some reason rosin core solderd is *the* Electronics Industry standard while acid core solder is *forbidden* for such use.
So "tree acid" and "Factory acid" (as you call it 🙄) are not the same as you claim.
Sorry.
As a former solder jockey, I can make some recommendations. In all seriousness, if you want your circuit build to last a very long time, clean it after soldering to remove all traces of flux, no matter what flux. This is DIY, so you aren't making 1000's of boards. Just take the time and clean it. Isopropyl, Simple Green, whatever. It feels funny scrubbing a stuffed and soldered PC board in water but so long as it's totally clean and dried before energizing it's probably the least potentially damaging method. Even zinc chloride pipe flux has its place in electronics for large connections that can't be properly clean before soldering. But it is difficult to clean petroleum base paste flux, and if used on stranded conductors or migrates under or into a component (like a small potentiometer) it can be plain impossible to completely clean off, so watch out / don't use it there.
This is excellent information. The article link posted my Marce is very informative. After reading that I believe this to be metal salts from the paste. I probably used to much or didn't get it hot enough or both. This is the first problem I've had of corrosion and the paste is new. I won't be using It again.
I've never washed my boards after population and haven't had problems but I probably should wash them. There are commercial board cleaners out there in spray cans. Sounds like some off you use alcohol and water. Do you simply immerse the entire populated board in the alcohol and then water to remove the leftover paste?
I've never washed my boards after population and haven't had problems but I probably should wash them. There are commercial board cleaners out there in spray cans. Sounds like some off you use alcohol and water. Do you simply immerse the entire populated board in the alcohol and then water to remove the leftover paste?
Andrew, you were posting the answer the same time I was asking question. Thanks. It also never occurred to me to flux the entire board and wash it prior to population. I've simply been cleaning them.well after etching and tinning them.
This board is a write off unfortunately but I'll be washing my boards after population from now on.
This board is a write off unfortunately but I'll be washing my boards after population from now on.
Actually the old tried and true wave soldering process used to cover the entire solder side with liquid flux by various means before running over the solder. Covering the board in paste flux would be a no-no, not sure that needed to be said but..
I have gone far as carefully dumping or spraying alcohol to "soak" a board full of heavy, old flux. I never saw the necessity to use a tank of it. Freshly used flux seems to lift up much more easily than very old, and some kind of general purpose or "bathroom" spray cleaner (non chlorine) with a toothbrush can out pace pure alcohol without all the fumes. Obviously a product specifically designed for washing boards would be expected to work well, although I've never used them, and you might check the contents for "industrial" chemicals that might need to be used outside or under a vent hood.
I have gone far as carefully dumping or spraying alcohol to "soak" a board full of heavy, old flux. I never saw the necessity to use a tank of it. Freshly used flux seems to lift up much more easily than very old, and some kind of general purpose or "bathroom" spray cleaner (non chlorine) with a toothbrush can out pace pure alcohol without all the fumes. Obviously a product specifically designed for washing boards would be expected to work well, although I've never used them, and you might check the contents for "industrial" chemicals that might need to be used outside or under a vent hood.
beware that Ketones like Acetone, MEK can eat a number of plastics used in capacitors, cases, pots...
...that said they are sometimes the best flux cleaners - so I sometimes cautiously use them as spot cleaners
hot soapy water is a good start before going to alcohols - 91% isopropyl is the strongest solvent I use generally on finished PCB
distilled water can be followed by (more) alcohol - dilutes, "drags out" the water from crevices for faster drying
...that said they are sometimes the best flux cleaners - so I sometimes cautiously use them as spot cleaners
hot soapy water is a good start before going to alcohols - 91% isopropyl is the strongest solvent I use generally on finished PCB
distilled water can be followed by (more) alcohol - dilutes, "drags out" the water from crevices for faster drying
- Status
- Not open for further replies.
- Home
- Design & Build
- Construction Tips
- Flux paste causing corrosion