I'm hoping to see some examples of CLD that members have attempted and maybe have a discussion about how effective different techniques have proven to be? I've done some searching on the subject, but I'm not sure how many of the people discussing the technology have built or go on to build a CLD enclosure.
I'm thinking about building CLD panels so the speaker can be made from thinner panels, to reduce weight and to increase internal volume relative to the external volume. (Plus sometimes feature creep is fun when I don't have a deadline...)
So far I've read that CLD works best when the surface plies are a rigid/ stiff material. And a thread mentioned that Geddes used a 40 shore A urethane for his designs.
I'm debating between 100% composite panels, composite sandwich construction using thin hardwood plywood as a core, or thin plywood with no composites.
I would plan to use urethane as the damping material. I have a couple gallons of 70 shore A material laying around. It may not be the ideal durometer, but it's the spoils from R&D from another project...(buy a gallon so I can make a test with 6oz of the material!) I can easily source a 40 shore A urethane like Geddes used if that would be a significant improvement, but I'll cross that bridge when I get there.
To solve the problem of constructing thin panels of consistent thickness, my most promising ideas are to either machine out shallow pockets in the surface plies, or add thin spacers around the edges of the panel to create an air gap inbetween the two plies. And then I would inject the urethane into that air gap.
I'm thinking about building CLD panels so the speaker can be made from thinner panels, to reduce weight and to increase internal volume relative to the external volume. (Plus sometimes feature creep is fun when I don't have a deadline...)
So far I've read that CLD works best when the surface plies are a rigid/ stiff material. And a thread mentioned that Geddes used a 40 shore A urethane for his designs.
I'm debating between 100% composite panels, composite sandwich construction using thin hardwood plywood as a core, or thin plywood with no composites.
I would plan to use urethane as the damping material. I have a couple gallons of 70 shore A material laying around. It may not be the ideal durometer, but it's the spoils from R&D from another project...(buy a gallon so I can make a test with 6oz of the material!) I can easily source a 40 shore A urethane like Geddes used if that would be a significant improvement, but I'll cross that bridge when I get there.
To solve the problem of constructing thin panels of consistent thickness, my most promising ideas are to either machine out shallow pockets in the surface plies, or add thin spacers around the edges of the panel to create an air gap inbetween the two plies. And then I would inject the urethane into that air gap.
I use mass loaded vinyl in between 3/4" plywood and 1/2" MDF. I build the plywood, lay in the vinyl then put the MDF in and glue it. I have put screws through the MDF into the plywood and I have also left it free standing. Not sure which is better.
I have definitely succeeded in making really heavy speakers.........I think it also helps with resonances.
Hi,I'm hoping to see some examples of CLD that members have attempted and maybe have a discussion about how effective different techniques have proven to be? I've done some searching on the subject, but I'm not sure how many of the people discussing the technology have built or go on to build a CLD enclosure.
I'm thinking about building CLD panels so the speaker can be made from thinner panels, to reduce weight and to increase internal volume relative to the external volume. (Plus sometimes feature creep is fun when I don't have a deadline...)
So far I've read that CLD works best when the surface plies are a rigid/ stiff material. And a thread mentioned that Geddes used a 40 shore A urethane for his designs.
I'm debating between 100% composite panels, composite sandwich construction using thin hardwood plywood as a core, or thin plywood with no composites.
I would plan to use urethane as the damping material. I have a couple gallons of 70 shore A material laying around. It may not be the ideal durometer, but it's the spoils from R&D from another project...(buy a gallon so I can make a test with 6oz of the material!) I can easily source a 40 shore A urethane like Geddes used if that would be a significant improvement, but I'll cross that bridge when I get there.
To solve the problem of constructing thin panels of consistent thickness, my most promising ideas are to either machine out shallow pockets in the surface plies, or add thin spacers around the edges of the panel to create an air gap inbetween the two plies. And then I would inject the urethane into that air gap.
I've done very simple experiments, I've had basically "normal" box built, then if there is any largish surfaces between bracing I've put thin sheet of ply with suitable shore adhesive to that area, like as the very last thing when building a box, a slap on fix so to speak. Sure enough it has some effect, knock test and measurement shows different sound to the portion where there is the panel compared to areas next to it, but this doesn't tell anything how effective the CLD there is, only that it does something. If you have to optimize a box for thin walls I'm afraid you must conduct some tests to make best out of it. At least you should prototype / test that performance is good enough. I've been pondering making CLD panels for next project, but it seems quite a hurdle to be effective and need prototyping and playing with adhesives so I likely won't, perhaps I'll still do the slap on additions like before. Interested on your thread though, so will follow.
I suppose you have studied at least basics of CLD but in case someone is not familiar here is some quickies:
it works so that there is two outer panels and viscoelastic material in between. When the panels deform, the surfaces to viscoelastic material get to different lengths and shear losses in the viscoelastic material should dampen it. See the image:
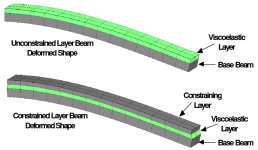
Image from https://www.semanticscholar.org/pap...-Pai/89c1c8f4bf248a1b1de2d0a23157b2f253c755da
The viscoelastic material needs to be have particular stiffness compared to the base and constraining layer for optimal damping, can't be too loose or too stiff, or performance suffers. So all three layers together determine the performance. See this for example, or any study about this stuff:
https://elib.dlr.de/187991/1/Manuscript_Final_Version.pdf
As seen in the photo above, on a panel the shear is most on the edges and least on the middle where the panel actually flexes (as in lowest mode). Panels have multiple modes though and could flex here and there at higher frequencies and you can steer it some with bracing, kill the first mode by having one brace in the middle.
General idea is to dampen any resonance on the panels to reduce their amplitude and Q perhaps. There are other ways to reduce audibility of panel resonances by designing the system with smaller panels, attaching a driver from magnet, using dual opposing drivers, making it stiff using bracing. One could use all of these, and some CLD in addition.
If I'm not mistaken Geddes uses light weight stiff box and CLD bracing, so the box panels resonate at high frequency (above driver pass band is the goal) and then the resonances get damped some with CLD structure in the bracing.
Gathering from these basics and that you have bit stiffer viscoelastic layer I'd make the outer layers stiffer as well, like thick plywood which is likely counter productive to your goals 😀 So, just experiment if it works. You could make comparison by using the same outerlayers but with stiff glue in between, without the viscoelasticity. You could also build finished box and evaluate performance as in final build, but that's more work. You could search the forum, at least augerpro has done some tests and published measurements of layered structure.
There is downside to thin speaker box panels though, they make difficult build box. You'd need some extra corner stuff or fancy joinery to make the corners sturdy enough. In this sense perhaps two 1/4" sheets and something in between makes thinnest I'd find usable, butt joints could work. This is more expensive than using one 1/2" thick sheet and much more work, so be sure you know all aspects of your design to be able to determine whether it's worh it, or would it be enough to just use CLD brace? Anyway, interesting engineering task it is.
I hope these give some ideas how to get started, have fun!🙂
ps. apparently auditory system is really sensitive to time aspect of audio, so if CLD can reduce decay time of any resonance it should be only positive thing, which kind of indicates all speaker boxes should consider CLD construct assuming it is easy to make it more effective than some other means of damping. If you already have certain panel material which you must use and all that you can do is to decide whether to use the soft or hard glue you also have it's almost a dice roll: you might get better damping with the soft one, while the harder would give more stiffness. You could add either with other means as well.
Last edited:
Layer of plywood , rubber , wool then another plywood layer.
Basically a floor mat from the hardware store.
Only the front baffle.
The cabinet was 2x15 for live sound use, and was already
a very thin walled cabinet with neo speakers for lightweight.
Being so light, I thought it needed a magical baffle to stop
possible rattles from such thin walls.
It did not rattle, and it sounded like every other 2x15
on a crossover.
DJ friend was amazed how light it was.
Borrowed for many live music nights, no complaints.
I sold it easily.
So most the satisfaction was getting rid of it.
And actually selling something I made.
My non magic baffles also sounded fine.
Sold or traded bunch of those too.
At 120 or so dB, nobody hears micro measured color graphs.
It either rattles or it dont, braces work for that.
Basically a floor mat from the hardware store.
Only the front baffle.
The cabinet was 2x15 for live sound use, and was already
a very thin walled cabinet with neo speakers for lightweight.
Being so light, I thought it needed a magical baffle to stop
possible rattles from such thin walls.
It did not rattle, and it sounded like every other 2x15
on a crossover.
DJ friend was amazed how light it was.
Borrowed for many live music nights, no complaints.
I sold it easily.
So most the satisfaction was getting rid of it.
And actually selling something I made.
My non magic baffles also sounded fine.
Sold or traded bunch of those too.
At 120 or so dB, nobody hears micro measured color graphs.
It either rattles or it dont, braces work for that.
I did now. I like the version on his website better. A lot of info, and wide ranging. For CLD, he took a minimally resonant enclosure and added CLD by making the cabinet thicker. This doesn't really help me, because I'd like to reduce material thickness.Did you read this yet?
Don't worry, my cabinet design was already difficult without CLD! That's part of the fun, right? Pushing our limits. Below is the first speaker, effectively a prototype still. There are a few things I have decided I want to change when I build the final version.There is downside to thin speaker box panels though, they make difficult build box.
https://www.diyaudio.com/community/...ting-multiple-subwoofers.401343/#post-7672370
I'm having decent results with Flex Paste applied on a surface then evened out with the short side of this bad boy, which sets up lines of paste alternated with clear grooves, both 1/4" (6 mm) in width and height. Clamping down the panel with a bolt in the middle spreads out the paste to fill the gaps.
Simply slapping it on isn't great because the thickness is tough to control, whereas the toothed trowel sets up the thickness admirably, especially if the mating surface is scuffed up with 80 grit beforehand. The paste hardens to Shore 40A, which seems to work well with the ultimate 1/8" (3mm) thickness the paste squishes down to.
Eventually I'll throw together an accelerometer measuring jig to quantify how good the result is, but for now hitting a 12 inch square panel with a hard object goes from a hollow sounding "tok" to a fairly dead sound somewhere between "tak" and "tik". Good enough for me.
Simply slapping it on isn't great because the thickness is tough to control, whereas the toothed trowel sets up the thickness admirably, especially if the mating surface is scuffed up with 80 grit beforehand. The paste hardens to Shore 40A, which seems to work well with the ultimate 1/8" (3mm) thickness the paste squishes down to.
Eventually I'll throw together an accelerometer measuring jig to quantify how good the result is, but for now hitting a 12 inch square panel with a hard object goes from a hollow sounding "tok" to a fairly dead sound somewhere between "tak" and "tik". Good enough for me.
What material thickness?for now hitting a 12 inch square panel with a hard object goes from a hollow sounding "tok" to a fairly dead sound somewhere between "tak" and "tik". Good enough for me.
I'm not sure what the ideal test setup would be, but intuitively I'd say a tap test would give some information about the effect of the construction. But it has to be consistent and repeatable for accurate results.
My guess is that the resonant frequency and the decay time should both change with CLD, if the damping is effective.
While not a speaker cabinet, I applied a layer of damping material between my sub floor (1 1/8" plywood) and oak floor (3/4" thick) and it reduced footfall sound appreciably compared to the area that does not have the damping material. The material looks like thin (around 1/32") green color foam roll and cost about $100 for @ 100 sq feet. Haven't tried in a speaker yet and I don't know if it would make a difference in that applications but was surprised how well it worked for our upstairs floor.
R
R
What material thickness?
I'm not sure what the ideal test setup would be, but intuitively I'd say a tap test would give some information about the effect of the construction. But it has to be consistent and repeatable for accurate results.
My guess is that the resonant frequency and the decay time should both change with CLD, if the damping is effective.
Base panel 3/4" (19 mm), second panel 1/2" (12 mm). The first one had Flex Paste slathered on, whereas it was distributed evenly as described forthe second one. No real difference between the two.
About 20 years ago, a small-shop surfboard shaper/builder named Bert Burger introduced a composite sandwich (compsand) method on swaylocks surfboard building forum. Each skin, itself a cored composite assembly, was vacuumed down to an eps foam core that was thinner and of lower density than could have effectively been used in basic cored composite construction. The boards were lighter, thinner and stiffer as a result. Each skin was 2oz glass, 1/8" balsa, 2oz glass. I've watched a diy built board being flung across a parking lot before being suspended near each end and jumped on without exterior or delam damage. CF/balsa/CF? FWIW He sold it off, now the tech is used in manufactured boards
I had that concept for a bike frame I made for a school project in the ‘90s. Had the idea years earlier but wasn’t ready to dive into something like that when I was 18.
What’s the name of the new company, if you recall?
What’s the name of the new company, if you recall?
@phase Firewire. Funny enough, I was checking their site out a couple months ago after popping into a new surf shop near here. I haven't been in the water in several years but I've got the itch.
Not composite but I was just checking out some cool wood framed bikes at a Wooden Boat Fest.
Not composite but I was just checking out some cool wood framed bikes at a Wooden Boat Fest.
I have used small bits of Sorbothane between baffles and car structure in a subwoofer installation that seems to work well.
The question about full CLD treatment is: is it worth the hassle?
Earl Geddes shifted from full treatment of box to CLD bracing during Summa production and this is what KEF use too.
There is a thread in there where Earl gives his pov about this even explain it's a dirty secret of industry ( cld bracing)... even recipe he used ( he mixed some small balls into melamine glue to accentuate the losses).
Earl Geddes shifted from full treatment of box to CLD bracing during Summa production and this is what KEF use too.
There is a thread in there where Earl gives his pov about this even explain it's a dirty secret of industry ( cld bracing)... even recipe he used ( he mixed some small balls into melamine glue to accentuate the losses).
I have done a lot of experimentation on enclosure material. I no longer use one type when building a speaker. The reason is that I believe that you need at least two different materials with two different speeds of sound through them. This works to smear out and dampen resonances.
My latest pair is made from oak, birch plywood, a layer of rubbery/tar-like sound dampening material, a layer of foam and/or denim batting, then polyfill. All together it makes the cabinet "dead" when you knock on it.
I've found that building anything out of 1 material is a recipe for disaster whenever oscillation or resonances are concerned. Same is true of bridges, buildings, and speakers. I'd love to love aluminum cone woofers but they do ring and you can hear it even when crossed over properly. (Not to say your results are doomed, just keep your expectations realistic)
Polymer cones or cones made of several different materials just sound better overall to me. Cones made from trees are hard to beat in many ways, as nature has done much of the refining for us in terms of weight, stiffness, and dampening.
My latest pair is made from oak, birch plywood, a layer of rubbery/tar-like sound dampening material, a layer of foam and/or denim batting, then polyfill. All together it makes the cabinet "dead" when you knock on it.
I've found that building anything out of 1 material is a recipe for disaster whenever oscillation or resonances are concerned. Same is true of bridges, buildings, and speakers. I'd love to love aluminum cone woofers but they do ring and you can hear it even when crossed over properly. (Not to say your results are doomed, just keep your expectations realistic)
Polymer cones or cones made of several different materials just sound better overall to me. Cones made from trees are hard to beat in many ways, as nature has done much of the refining for us in terms of weight, stiffness, and dampening.
I must have missed the notification... But what you said is a good summary of what I am hoping to ask. It probably is not practical, but I'm interested in a light weight construction that is still damped.The question about full CLD treatment is: is it worth the hassle?
Nobody has commented about using CLD to make a thin panel non-resonant, but I think that is the main engineering application? I mean, reduce resonance/ noise with minimum added weight/ bulk. Geddes talks about using it in high end cars. The only commercial speaker application I've come across (aside from Geddes' own speakers) is the aluminum spiral portion of the Genelec LSE subwoofers. Atleast it looks like CLD from a photo I found, but I'm not 100% sure.
I'll try to knock together some sample panels this weekend. I think 1/4"/ 6mm plywood (total thickness) with a thin layer of urethane inside. The goal would be to match or improve on the resonance of a piece of 3/4"/ 19mm MDF.
Hi @fredygump,
Yes a 'real' CLD means use of a very thin damping layer where shear happen.
Imho most 'sandwiched' built technique presented by members are a bit different in their results than a 'textbook' CLD ( i would call them multilayer damping), that doesn't say they aren't effective though.
And i agree with you one of the main application of textbook CLD is to make 'thin' light rigid structures ( it all depend of scale as in a 'oil supertanker' vessel, a 1meter thick metal sheet can be 'thin' and 'light' relative to the whole structure... 🙂 ) damped. But in the case of loudspeakers it's difficult to have 'thin' walls, except if you use metal like Genelec.
[Edit:Talking about Genelec cast aluminium boxes i've seen, they didn't used CLD, but 'traditional' damping material and different thickness/geometry at 'key' area/location. But it was a small nearfield, they could have different approach for different box size and target program. ]
Maybe it's true for composite structure like you have done too? I wonder if thin wood base+carbon+epoxy will react the same as a metal sheet rather than same thickness in wood only? We should have to study modulus and such... but i disgress.
In fact i wonder if wood (material) is adapted to a whole CLD boxe approach. If E.Geddes or Kef switched to some CLD matrix/bracing technique it's not only for ease of build ( this was clearly stated by Earl) but because it is as efficient and cost way less to do too.
Have you found the thread i refered about? There was some link to a patent about this in it with many possible application of bracing approach.
If you decide to do some testing about CLD i would include the whole box too. I mean, once you have found a CLD recipe which work for your target, build a box with it, a second one using only CLD bracing and a third with 'traditional' approach... then compare them.
It's a lot of work and it rise some issues ( eg a smaller boxe (5Liters) will have different behavior than a bigger one (150liter) by different structural and scale property) but it would be a definitive test about effectiveness of the approach.
I would target the application too: a subwoofer will see little improvement from a CLD box ( in comparison to extreme 'traditional' bracing) but a mid dedicated enclosure will surely have.
Yes a 'real' CLD means use of a very thin damping layer where shear happen.
Imho most 'sandwiched' built technique presented by members are a bit different in their results than a 'textbook' CLD ( i would call them multilayer damping), that doesn't say they aren't effective though.
And i agree with you one of the main application of textbook CLD is to make 'thin' light rigid structures ( it all depend of scale as in a 'oil supertanker' vessel, a 1meter thick metal sheet can be 'thin' and 'light' relative to the whole structure... 🙂 ) damped. But in the case of loudspeakers it's difficult to have 'thin' walls, except if you use metal like Genelec.
[Edit:Talking about Genelec cast aluminium boxes i've seen, they didn't used CLD, but 'traditional' damping material and different thickness/geometry at 'key' area/location. But it was a small nearfield, they could have different approach for different box size and target program. ]
Maybe it's true for composite structure like you have done too? I wonder if thin wood base+carbon+epoxy will react the same as a metal sheet rather than same thickness in wood only? We should have to study modulus and such... but i disgress.
In fact i wonder if wood (material) is adapted to a whole CLD boxe approach. If E.Geddes or Kef switched to some CLD matrix/bracing technique it's not only for ease of build ( this was clearly stated by Earl) but because it is as efficient and cost way less to do too.
Have you found the thread i refered about? There was some link to a patent about this in it with many possible application of bracing approach.
If you decide to do some testing about CLD i would include the whole box too. I mean, once you have found a CLD recipe which work for your target, build a box with it, a second one using only CLD bracing and a third with 'traditional' approach... then compare them.
It's a lot of work and it rise some issues ( eg a smaller boxe (5Liters) will have different behavior than a bigger one (150liter) by different structural and scale property) but it would be a definitive test about effectiveness of the approach.
I would target the application too: a subwoofer will see little improvement from a CLD box ( in comparison to extreme 'traditional' bracing) but a mid dedicated enclosure will surely have.
Last edited:
- Home
- Design & Build
- Construction Tips
- Have You Attempted Constrained Layer Damping (CLD); What did you do and how did it work?