Hello everybody,
I've jsut got a webinar invitation for some 3M filters:
http://www.filter-equipment.com/uploads/1/2/2/8/122858212/3m-high-flow-hfr-series-data-sheet_1.pdf
Look at bottom right of page 2. That one has the purpose to increase the filtering surface area of a flow passing through the filter, but...
Imagine that the flows doesn't pass through the membranes but tangentially... imagine that is not a membrane but a sheet of Alluminium, imagine it is air and not water and imagine it clamped on the magnet of the cone.
Has anyone ever done a "clampable heat sink" made in the 3M HFR way, to be clamped on the magnet and with the same diameter of the speaker?
The purpose is:
- increase the heat tranfer coefficient (when the cone moves, the convection goes from natural to forced (by the cone moving), so increase the capability to transfer heat;
- increase in the surface area of the magnet, so increase the capability to transfer heat.
This will give two scenarios:
- lower temperatures for the magnet, so higher reliability for the speaker;
- higher allowed power handling.
Has anyone an idea on how (badly) it would impact the sonic performance of the speaker?
By doing the "radiator" in Alluminium and thin, it will give optimal passage for the air, low weight, low costs and less sonic impact, but how can it be calculated?
Thank you all in advance
Roberto
I've jsut got a webinar invitation for some 3M filters:
http://www.filter-equipment.com/uploads/1/2/2/8/122858212/3m-high-flow-hfr-series-data-sheet_1.pdf
Look at bottom right of page 2. That one has the purpose to increase the filtering surface area of a flow passing through the filter, but...
Imagine that the flows doesn't pass through the membranes but tangentially... imagine that is not a membrane but a sheet of Alluminium, imagine it is air and not water and imagine it clamped on the magnet of the cone.
Has anyone ever done a "clampable heat sink" made in the 3M HFR way, to be clamped on the magnet and with the same diameter of the speaker?
The purpose is:
- increase the heat tranfer coefficient (when the cone moves, the convection goes from natural to forced (by the cone moving), so increase the capability to transfer heat;
- increase in the surface area of the magnet, so increase the capability to transfer heat.
This will give two scenarios:
- lower temperatures for the magnet, so higher reliability for the speaker;
- higher allowed power handling.
Has anyone an idea on how (badly) it would impact the sonic performance of the speaker?
By doing the "radiator" in Alluminium and thin, it will give optimal passage for the air, low weight, low costs and less sonic impact, but how can it be calculated?
Thank you all in advance
Roberto
Last edited:
Thanks JonSnell,
so the heat transfer from the coil to the magnet is poor?
I ask so because I remember years ago, in the early ages of Neodimium for Bass Instrument cabinets, that high magnetic temperatures lead to irrecoverable worse performances (low Curie temperatures?).
so the heat transfer from the coil to the magnet is poor?
I ask so because I remember years ago, in the early ages of Neodimium for Bass Instrument cabinets, that high magnetic temperatures lead to irrecoverable worse performances (low Curie temperatures?).
Modern neo drivers are better in that regard.
However, yes, the coil-to-magnet heat transfer isn't great. That's why the biggest drivers (M-Force) use fixed coils (so they can attach heatsinks) and moving magnets.
A heatsink can be useful for long-term power handling. Problems tend to occur when the magnet is saturated with heat - the voice coil has to get even hotter before it can transfer heat to the magnet.
Adding a heatsink would mean more of the heat from the coil ends up inside the cabinet, though. Eminence did their Kilomax drivers a while ago, which put a heatsink on the front of the driver so the heat could be radiated to the outside world. Those things could really take some power, but the compromises made to the motor (low BL) meant they weren't great drivers anyway.
In conclusion, getting rid of heat from driver is good, so long as it's being expelled outside the cabinet.
Chris
However, yes, the coil-to-magnet heat transfer isn't great. That's why the biggest drivers (M-Force) use fixed coils (so they can attach heatsinks) and moving magnets.
A heatsink can be useful for long-term power handling. Problems tend to occur when the magnet is saturated with heat - the voice coil has to get even hotter before it can transfer heat to the magnet.
Adding a heatsink would mean more of the heat from the coil ends up inside the cabinet, though. Eminence did their Kilomax drivers a while ago, which put a heatsink on the front of the driver so the heat could be radiated to the outside world. Those things could really take some power, but the compromises made to the motor (low BL) meant they weren't great drivers anyway.
In conclusion, getting rid of heat from driver is good, so long as it's being expelled outside the cabinet.
Chris
Thanks Chris,
I was not aware of this technology:
https://www.powersoft-audio.com/it/docman/897-m-force-datasheet/file
very smart!
Powersoft Introduces New M-Force Design at 2018 Prolight+Sound | audioXpress
Powersoft to Present on Advanced Subwoofer Design and its Patented M-Force Loudspeaker Technology at 137th AES Convention | audioXpress
I was not aware of this technology:
https://www.powersoft-audio.com/it/docman/897-m-force-datasheet/file
very smart!
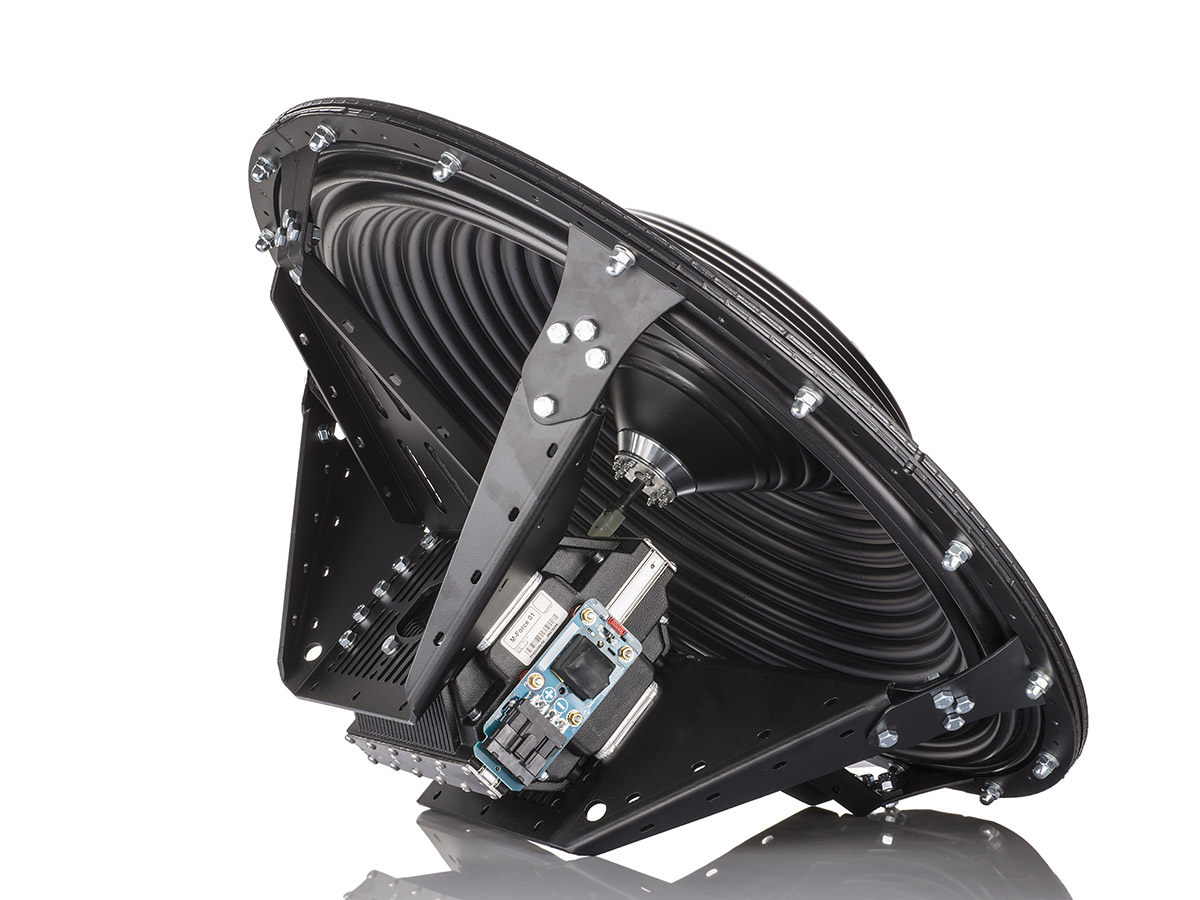
Powersoft Introduces New M-Force Design at 2018 Prolight+Sound | audioXpress
Powersoft to Present on Advanced Subwoofer Design and its Patented M-Force Loudspeaker Technology at 137th AES Convention | audioXpress
Why not just use a thermo-electric cooler "TEC" with the hot side loaded onto a water jacket with plumbing, pump, temperature feedback control, etc? That'd get the pole piece down to where condensation / ice would be your next problem. But I imagine an ice cold pole piece is better for the VC than a hot one. More Power!
- Home
- Loudspeakers
- Full Range
- Heat-sink to be clamped to the magnet of the speaker