Recently @hifijim started a new project involving the Bliesma T25A tweeter, as part of the discussion I offered to see if a simple small waveguide could be simulated. Jim has decided against the use of a waveguide for perfectly understandable reasons. I don't have a T25A myself and so I haven't created a printable model of the profile to test. There was some interest shown in that thread for the waveguide profile to be posted in a separate thread, so here it is.
The Bliesma aluminium drivers are very tall and require a different profile than many modern waveguides aim for in order to avoid ugly cancellations in the very high frequency range. I tried a number of variations on a theme in Ath to see what I could get, but it was not easy to find a profile that did not have some kind of downside to it.
I've simulated many CAD drawn profiles for the T25A in the past and so that is the route I tried next. This should hardly come as news or any kind of discovery as it has been known for a long time that dome tweeters almost always work in a waveguide that uses a section of a circular radius for it's profile. This does not have as dramatic of an effect on the directivity as OS or other proflies can have, but it is that property of not doing too much that allows it to work almost as a universal profile.
It is very simple to draw in a CAD program. I use Fusion and will outline how to use that program to draw it, but the principal could be applied to any other program.
This waveguide is thin at 6mm and relatively small at 104mm in diameter, similar to a standard tweeter faceplate.
I first draw a circle on the XZ plane that represents the throat, in this case it is 29.7mm, using a slightly higher value of 30mm might be preferable depending on the properties of the material being used to print it.
A new sketch is drawn on the XY plane and the previous circle is projected into this sketch. I draw a construction line straight up at the depth of the waveguide in this case 6mm. I then draw another line across at a 90 degree angle the distance of half the overall diameter in this case 52mm. I then draw a 3 point arc between the projected throat, the outer point of the waveguide profile and the last point just needs to be below the top construction line. With practice you can place it so that tangency is already enforced, but if not use the sketch constraints to make the 3 point arc tangent to the top construction line. You can check if this has worked by extending the arc all the way around until it becomes a circle. In this case the 3 point arc as drawn has a radius of 118.01mm.
The centre point of the circle that is the radius can be see by zooming out the sketch, it is highlighted in yellow
The same principal could be used to create a deeper and larger version of the same thing, there will then be a bigger effect on the overall directivity. This may not be a good thing for the T25A, but if the same ratio is kept between depth and outer diameter I would imagine it could be scaled up without creating negative interference. I haven't tested this so I cannot say exactly what will happen.
I have attached the surface profile as a zipped step file in case anyone wants to use it as is to create their own printable model.
I have attached the simulation outputs based on Jim's baffle. It is more consistent and even than a bare driver and given the size constraints, it fit's on the same diameter as the driver or can be made to. These are non normalized and show 1500 to 15K 0 to 90 degrees in 10 degree steps. The response is pretty much within 1 or 2 dB 0 to 40 degrees and is an even 10 dB down across the board at 90 degrees vs 0.
There is diffraction on axis because this is a BEM model with fully reflective boundaries. All sharp edges and creases on the baffle of which there are a few that are also symmetric show the worst case scenario. A real wooden baffle with smoothed edges and a less symmetric profile would offset this to some extent.
By 15 degrees off axis the response is a pretty smooth downslope
The Bliesma aluminium drivers are very tall and require a different profile than many modern waveguides aim for in order to avoid ugly cancellations in the very high frequency range. I tried a number of variations on a theme in Ath to see what I could get, but it was not easy to find a profile that did not have some kind of downside to it.
I've simulated many CAD drawn profiles for the T25A in the past and so that is the route I tried next. This should hardly come as news or any kind of discovery as it has been known for a long time that dome tweeters almost always work in a waveguide that uses a section of a circular radius for it's profile. This does not have as dramatic of an effect on the directivity as OS or other proflies can have, but it is that property of not doing too much that allows it to work almost as a universal profile.
It is very simple to draw in a CAD program. I use Fusion and will outline how to use that program to draw it, but the principal could be applied to any other program.
This waveguide is thin at 6mm and relatively small at 104mm in diameter, similar to a standard tweeter faceplate.
I first draw a circle on the XZ plane that represents the throat, in this case it is 29.7mm, using a slightly higher value of 30mm might be preferable depending on the properties of the material being used to print it.
A new sketch is drawn on the XY plane and the previous circle is projected into this sketch. I draw a construction line straight up at the depth of the waveguide in this case 6mm. I then draw another line across at a 90 degree angle the distance of half the overall diameter in this case 52mm. I then draw a 3 point arc between the projected throat, the outer point of the waveguide profile and the last point just needs to be below the top construction line. With practice you can place it so that tangency is already enforced, but if not use the sketch constraints to make the 3 point arc tangent to the top construction line. You can check if this has worked by extending the arc all the way around until it becomes a circle. In this case the 3 point arc as drawn has a radius of 118.01mm.
The centre point of the circle that is the radius can be see by zooming out the sketch, it is highlighted in yellow
The same principal could be used to create a deeper and larger version of the same thing, there will then be a bigger effect on the overall directivity. This may not be a good thing for the T25A, but if the same ratio is kept between depth and outer diameter I would imagine it could be scaled up without creating negative interference. I haven't tested this so I cannot say exactly what will happen.
I have attached the surface profile as a zipped step file in case anyone wants to use it as is to create their own printable model.
I have attached the simulation outputs based on Jim's baffle. It is more consistent and even than a bare driver and given the size constraints, it fit's on the same diameter as the driver or can be made to. These are non normalized and show 1500 to 15K 0 to 90 degrees in 10 degree steps. The response is pretty much within 1 or 2 dB 0 to 40 degrees and is an even 10 dB down across the board at 90 degrees vs 0.
There is diffraction on axis because this is a BEM model with fully reflective boundaries. All sharp edges and creases on the baffle of which there are a few that are also symmetric show the worst case scenario. A real wooden baffle with smoothed edges and a less symmetric profile would offset this to some extent.
By 15 degrees off axis the response is a pretty smooth downslope
Attachments
Thank you for sharing your work and fusion steps.
To test the BEM model, do you have modeled the shapes of the t25a, dome and suspension?
Is it mandatory?
How to have an accurate 3d model of a tweeter?
To test the BEM model, do you have modeled the shapes of the t25a, dome and suspension?
Is it mandatory?
How to have an accurate 3d model of a tweeter?
Yes I have the dome and surround modeled for any dome tweeter that I am simulating. It does need to be a reasonably accurate physical match for the actual tweeter and all of the dimensions have an impact on the response that each tweeter will produce.
I have drawings of the Bliesma drivers that I got from the manufacturer. Scan speak and Purifi have CAD models of their drivers that could be used to extract the information. With, time and some non magnetic measuring tools any driver could be physically measured to get close enough dimensions.
Hard domes are required for accurate simulation with only BEM.
I have drawings of the Bliesma drivers that I got from the manufacturer. Scan speak and Purifi have CAD models of their drivers that could be used to extract the information. With, time and some non magnetic measuring tools any driver could be physically measured to get close enough dimensions.
Hard domes are required for accurate simulation with only BEM.
Yes this very helpfull !Scan speak and Purifi have CAD models of their drivers that could be used to extract the information
Non magnetic tools. I must find this. The bliesma motor is very strong.With, time and some non magnetic measuring tools any driver could be physically measured to get close enough dimensions.
If I understand correctly, with this Akabak BEM, the assumption is that the dome and suspension have a linear behaviour.Hard domes are required for accurate simulation with only BEM.
So the most important thing is the surface geometry...
I've launched Akabak last night for the first time and run the waveguide profile with a flat source diaphragm, to test the sofware.
Not very successful. There was mistakes in the observations settings.
Now I must draw the tweeter 3d model, starting with a simple spherical dome and flast suspension.
If the results are closed to yours, I could go futher.
Thomas
Everything is modeled as reflective and infinitely stiff unless damping is applied. The surface geometry is important and getting a good mesh to use in a manual design can take some experience, this is one area where Ath is very good if it works for the design.If I understand correctly, with this Akabak BEM, the assumption is that the dome and suspension have a linear behaviour.
So the most important thing is the surface geometry...
A flat source is fine to simulate a compression driver but a dome tweeter is quite different. Observation settings are easy to change in AKABAK but choosing the correct plane to put them on can be a head scratcher sometimes. Use the spectrum hints to show you where start axis is and the direction the observations are going. I have vertical up to 90 and horizontal right to 90 in this example. If it was to 180 the grey arc would extend to the green lineI've launched Akabak last night for the first time and run the waveguide profile with a flat source diaphragm, to test the sofware.
Not very successful. There was mistakes in the observations settings.
Some hours later learning Akabak with this "Fluid simple waveguide" ...
T25A-6
It is based on the T25B, I changed only the dome height, not the surround.
Box model
Simulation Normalized
Horizontal, 1m distance, farfield
Normalized at 0°
Fixed driving, amplification 1 and no weighting
1500 Hz to 15k Hz
Simulation Non normalized
Test non normalized
Fixed driving at 0.2
Weighting Divide by JW
Things to improve and to do
I'm not sure that the surround of the T25A is the same than T25B.
In Acoustic Horn Design – The Easy Way (Ath4) the surround radiation is divided in two parts weighted by 0.25 and 0.75.
I don't know if this make a big difference.
BTW this thread is an amazing treasure but very long and difficult sometimes.
@fluid
What are yours settings when you don't use the normalization ?
I don' have success to simulate in infinite baffle because the apex of the dome is higher than the waveguide.
I'll could make a big baffle in Fusion maybe 2x the wavelength.
Is it enough ?
That's ok with the WG scale x2 in IB. I'll share later.
Thomas
T25A-6
It is based on the T25B, I changed only the dome height, not the surround.
Box model
Simulation Normalized
Horizontal, 1m distance, farfield
Normalized at 0°
Fixed driving, amplification 1 and no weighting
1500 Hz to 15k Hz
Simulation Non normalized
Test non normalized
Fixed driving at 0.2
Weighting Divide by JW
Things to improve and to do
I'm not sure that the surround of the T25A is the same than T25B.
In Acoustic Horn Design – The Easy Way (Ath4) the surround radiation is divided in two parts weighted by 0.25 and 0.75.
I don't know if this make a big difference.
BTW this thread is an amazing treasure but very long and difficult sometimes.
@fluid
What are yours settings when you don't use the normalization ?
I don' have success to simulate in infinite baffle because the apex of the dome is higher than the waveguide.
I'll could make a big baffle in Fusion maybe 2x the wavelength.
Is it enough ?
That's ok with the WG scale x2 in IB. I'll share later.
Thomas
These are the settings I use and I do split the surround.
I almost always simulate non normalised and then duplicate the graph in VACS and add normalisation to that.
As far as I know the T25B and A surrounds have the same diameter and shape.
It hasn't created an issue in your simulation but watch out for creating meshes with CAD programs as they produce long thin triangles like in your waveguide. These can be a problem for correct simulation and BEM in general works much better when the traingles are even on all sides.
You also have to consider that with big roundovers on all sides you can sometimes see effects from sound going all the way around and when the simulation ends up sqaure there are two dimensions that can reinforce or cancel, which is unlikely to be true in a real speaker.
The T25B will also respond better to deeper profiles than the T25A if you want to try them out.
I almost always simulate non normalised and then duplicate the graph in VACS and add normalisation to that.
As far as I know the T25B and A surrounds have the same diameter and shape.
It hasn't created an issue in your simulation but watch out for creating meshes with CAD programs as they produce long thin triangles like in your waveguide. These can be a problem for correct simulation and BEM in general works much better when the traingles are even on all sides.
You also have to consider that with big roundovers on all sides you can sometimes see effects from sound going all the way around and when the simulation ends up sqaure there are two dimensions that can reinforce or cancel, which is unlikely to be true in a real speaker.
The T25B will also respond better to deeper profiles than the T25A if you want to try them out.
You can scale it up so that as it gets wider it also gets deeper, for the T25B that will most likely be fine, much harder to say for the T25A without a simulation as it is very picky.
That off axis nulling above 10k is what starts to happen when the waveguide narrows the pattern, it gets worse with increasing directivity.
Thinking about to give it a try:
Thanks a lot for the design! 👍 🙂
Thanks a lot for the design! 👍 🙂
An SLA print in Nylon would look nice, if you decide to give it a try let me know how it goes 🙂Thinking about to give it a try:
Thanks a lot for the design! 👍 🙂
New try...
This a free standing waveguide.
It has been generated with ATH Rosse, thanks to @mabat !
Diameter 10cm, depth 9mm
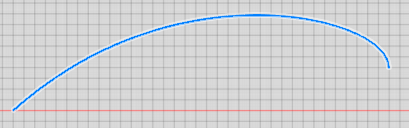
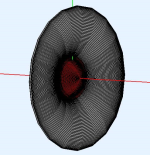
It may be possible to integrate it in a baffle with some work or rework.
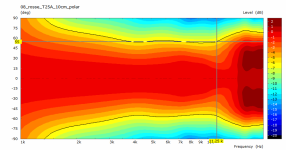
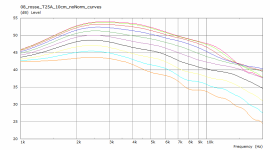
The top looks ugly but the T25A starts to widen after 12K Hz.
IHMO this could add some "air" but simply nothing wrong for the old ears. 🙂
Thomas
This a free standing waveguide.
It has been generated with ATH Rosse, thanks to @mabat !
Diameter 10cm, depth 9mm
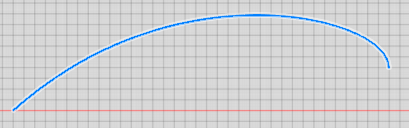
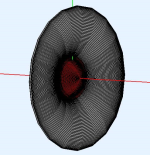
It may be possible to integrate it in a baffle with some work or rework.
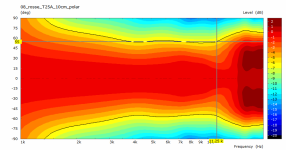
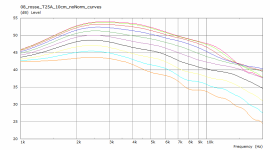
The top looks ugly but the T25A starts to widen after 12K Hz.
IHMO this could add some "air" but simply nothing wrong for the old ears. 🙂
Thomas
Just ordered the parts few days ago, PA12 material. Will paint it black then, have a small 2k lacquer 150ml spray can left over I will spend on this. 104mm diameter / 6mm depth are ideal to ensure exchangeability with other tweeters from Seas, Scan Speak, SB etc. Circle Diameter is 92mm so I can directly replace a Seas DXT in my current speaker for initial test. Will post measurements but it might take few weeks until the parts arrive and find time to do the sweeps....
This is because the profile is too deep for the nominal width of it, it is the reason why the T25A is so fickle in most existing waveguides.The top looks ugly but the T25A starts to widen after 12K Hz.
Where the profile ends before the termination begins is quite a bit less than 10cm.
Yes the tall dome with too deep profile creates diffraction.
I don't know how much this effect can be heard at those frequencies.
Is the control at the lower FR range worths this trade off ?
However, I don't have this tweeter and one of its great quality is its wide radiation.
I don't know how much this effect can be heard at those frequencies.
Is the control at the lower FR range worths this trade off ?
However, I don't have this tweeter and one of its great quality is its wide radiation.
- Home
- Loudspeakers
- Multi-Way
- T25A Simple Waveguide Profile