One of the most important reasons DIY'ers and commercial manufacturers alike choose to make small speakers is that we want them to take up less space in our room. We would all prefer large speakers if this wasn't important to us.
The smaller the speaker get the more critical the wall thickness of the cabinet becomes. The table below illustrates this, I have calculated the internal and external volume of cabinets from 1 to 10 liters with internal dimensions related for this example by a so called golden ratio of 1.6 and wall thickness of 10mm (already considered by many to be very thin).
Internal volume, External volume, Increase in %
1.0000 1.7820 78.2000
2.0000 3.1944 59.7202
3.0000 4.5357 51.1901
4.0000 5.8381 45.9518
5.0000 7.1146 42.2916
The same internal volumes but this time with wall thickness of 5mm
Internal volume, External volume, Increase in %
1.0000 1.3558 35.5750
2.0000 2.5536 27.6785
3.0000 3.7183 23.9447
4.0000 4.8648 21.6211
5.0000 5.9991 19.9828
As you can see the difference for small volumes is quite dramatic. Commercial manufacturers solve this by using thin walled cabinets of molded plastic or cast aluminum. These methods are not available to DIY'ers so how could we best make thin walled small cabinets?
The smaller the speaker get the more critical the wall thickness of the cabinet becomes. The table below illustrates this, I have calculated the internal and external volume of cabinets from 1 to 10 liters with internal dimensions related for this example by a so called golden ratio of 1.6 and wall thickness of 10mm (already considered by many to be very thin).
Internal volume, External volume, Increase in %
1.0000 1.7820 78.2000
2.0000 3.1944 59.7202
3.0000 4.5357 51.1901
4.0000 5.8381 45.9518
5.0000 7.1146 42.2916
The same internal volumes but this time with wall thickness of 5mm
Internal volume, External volume, Increase in %
1.0000 1.3558 35.5750
2.0000 2.5536 27.6785
3.0000 3.7183 23.9447
4.0000 4.8648 21.6211
5.0000 5.9991 19.9828
As you can see the difference for small volumes is quite dramatic. Commercial manufacturers solve this by using thin walled cabinets of molded plastic or cast aluminum. These methods are not available to DIY'ers so how could we best make thin walled small cabinets?
Those hollow plastic fence post builds around the net offer some insight into a method if getting thin-wall boxes made by the DIYer with minimal fuss. Just glue in a cutout to the top and bottom ~1/2" thick or whatever floats your canoe.
Interesting, had not heard about those fence post builds.
Plastic tubes may be a valid solution, if they are stiff enough. It limits the choice of dimensions though, the width and depth has to be equal which isn't ideal.
For those interested here are the internal dimensions of the speaker volumes in the first post in cm:
6.2500 10.0000 16.0000
7.8745 12.5992 20.1587
9.0141 14.4225 23.0760
9.9213 15.8740 25.3984
10.6873 17.0998 27.3596
and external dimensions for 10mm wall thickness
8.2500 12.0000 18.0000
9.8745 14.5992 22.1587
11.0141 16.4225 25.0760
11.9213 17.8740 27.3984
12.6873 19.0998 29.3596
Plastic tubes may be a valid solution, if they are stiff enough. It limits the choice of dimensions though, the width and depth has to be equal which isn't ideal.
For those interested here are the internal dimensions of the speaker volumes in the first post in cm:
6.2500 10.0000 16.0000
7.8745 12.5992 20.1587
9.0141 14.4225 23.0760
9.9213 15.8740 25.3984
10.6873 17.0998 27.3596
and external dimensions for 10mm wall thickness
8.2500 12.0000 18.0000
9.8745 14.5992 22.1587
11.0141 16.4225 25.0760
11.9213 17.8740 27.3984
12.6873 19.0998 29.3596
Here's one: Fence Post Speaker 2.0 - AudioKarma.org Home Audio Stereo Discussion Forums
There are some on the youtooob, some on other forums. I personally think it's a great idea. I think a guy could make some pretty respectable little micro speakers for dirt cheap utilizing them. or the tall skinny floor standing units as pictured above are certainly interesting (I think they are actually attractive personally).
Eric
There are some on the youtooob, some on other forums. I personally think it's a great idea. I think a guy could make some pretty respectable little micro speakers for dirt cheap utilizing them. or the tall skinny floor standing units as pictured above are certainly interesting (I think they are actually attractive personally).
Eric
Hi,
Probably by using thin ply and lining the cabinet internally with
perforated zinced steel sheeting, attached by a thick contact
adhesive layer that would act as a constrained damping layer.
Something similar has been done in the past.
A wackier idea is thin ply, a layer of porous but stiff foam and then
a further layer of holed pegboard / hardboard internally, the walls
would form absorbers at certain frequencies but below those the
foam layer would contribute to the effective internal volume.
I've had some wacky ideas regarding the issue over the years,
including thin ply walls with an internal matrix of varnished
holed corrugated cardboard as effective bracing.
Mission allegedly made a small sealed speaker with thin walls
and completely filled with fairly stiff porous foam as "bracing".
Using something like 1/4" steel plate for the front baffle helps.
rgds, sreten.
Probably by using thin ply and lining the cabinet internally with
perforated zinced steel sheeting, attached by a thick contact
adhesive layer that would act as a constrained damping layer.
Something similar has been done in the past.
A wackier idea is thin ply, a layer of porous but stiff foam and then
a further layer of holed pegboard / hardboard internally, the walls
would form absorbers at certain frequencies but below those the
foam layer would contribute to the effective internal volume.
I've had some wacky ideas regarding the issue over the years,
including thin ply walls with an internal matrix of varnished
holed corrugated cardboard as effective bracing.
Mission allegedly made a small sealed speaker with thin walls
and completely filled with fairly stiff porous foam as "bracing".
Using something like 1/4" steel plate for the front baffle helps.
rgds, sreten.
Last edited:
It's worth noting that smaller boxes will hold smaller woofers which are probably used to a higher frequency. There is therefore a call to make the walls more stiff. Further to that, the front baffle, which holds other drivers/ranges, should probably be even more solid.
The plastic thing is getting closer to reality with reprap machines. Here's the latest:...
As you can see the difference for small volumes is quite dramatic. Commercial manufacturers solve this by using thin walled cabinets of molded plastic or cast aluminum. These methods are not available to DIY'ers so how could we best make thin walled small cabinets?
MakerBot Replicator? - MakerBot Industries
The build area (volume) is still too small for a (full-range) cabinet, and substantial wall thickness would take a lot of plastic, but perhaps a cabinet could be build up from several "prints." Also this (melted and extruded plastic built up in layers to make the cabinet) may not be the same as molded plastic, but I have the bottle opener right in front of me, and even though it's a not-quite-competed print, it seems pretty strong to me.
Also, with "printing" the walls, they don't have to be flat, they can have built-in beams for strength and raising resonant frequencies of the panels, and/or have weird patterns on the inside and/or outside as sreten was mentioning. I'm trying hard not to mention the infamous "E" word here...
Last edited:
there are heavy duty PVC and Fiberglass "square" tube with rounded corner profiles available. Up to 6x6" at mcmaster. Not exactly cheap stuff but... you could probably get quite a few little "micro towers" out of a 5' section ($100+ depending on size).
Eric
Eric
Hi,
A wackier idea is thin ply, a layer of porous but stiff foam and then
a further layer of holed pegboard / hardboard internally, the walls
would form absorbers at certain frequencies but below those the
foam layer would contribute to the effective internal volume.
I like this kind of whacky idea!
You could build up a board from many thin layers (~1mm each?) where only the outer layer was solid, the others were holed out, sort of like swiss cheese. Bonded together it would be just as stiff as a solid board of same total thickness I would think.
I was also thinking about prestressing thin plywood by forcing it to bend. For example the sidewall could be thin ply that was bent outwards by tightening bolts that went from front to back panel. Prestressing it like that should make it resist the internal airpressure better.
That's great 🙄. Saves you the trouble of buying cheap plywood with voids.
You could build up a board from many thin layers (~1mm each?) where only the outer layer was solid, the others were holed out, sort of like swiss cheese. Bonded together it would be just as stiff as a solid board of same total thickness I would think.
I just had a thought related to the swiss cheese idea..
In order to organize my collets for the mill, I took a piece of 3/4" MDF and made a grid of blind flat bottom plunge cuts on it to act as a holder/orgnizer for my collet sets.
You can see the piece of MDF with the collets in the holes in this image:
I wonder if a similar approach, perhaps with smaller diameter cuts, could be implemented to good effect. Heck... that has me wanting to build some little speakers that way 🙂 I wonder if it would be better to use flat bottom holes for maximum volume retrieval or holes with a conical bottom (135 degree angle from a drill bit), large holes? small holes?
Any idea what would be the best way to approach that?
In order to organize my collets for the mill, I took a piece of 3/4" MDF and made a grid of blind flat bottom plunge cuts on it to act as a holder/orgnizer for my collet sets.
You can see the piece of MDF with the collets in the holes in this image:
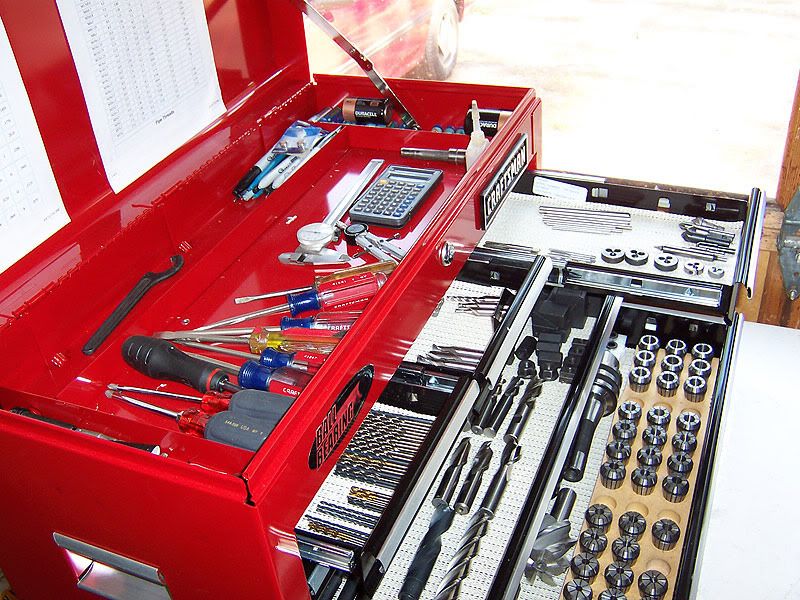
I wonder if a similar approach, perhaps with smaller diameter cuts, could be implemented to good effect. Heck... that has me wanting to build some little speakers that way 🙂 I wonder if it would be better to use flat bottom holes for maximum volume retrieval or holes with a conical bottom (135 degree angle from a drill bit), large holes? small holes?
Any idea what would be the best way to approach that?
Hi,
You could make a swiss cheesed cabinet, with holes in a
honeycomb pattern and then clad it in 3 ply to finish it off.
Regarding the above flat holes would be better IMO. Hole size is
not that critical, its really about the spacing, the ribs you leave.
It would make sense to vary hole size to avoid one critical frequency.
rgds, sreten.
Another wacky idea :
Using something like the above epoxy the top surface to the inside walls.
(Some form of disposable roller would be good for applying the glue I'd say.)
Due to the bottom layer you will end up with a dual layer sandwich.
You could make a swiss cheesed cabinet, with holes in a
honeycomb pattern and then clad it in 3 ply to finish it off.
Regarding the above flat holes would be better IMO. Hole size is
not that critical, its really about the spacing, the ribs you leave.
It would make sense to vary hole size to avoid one critical frequency.
rgds, sreten.
Another wacky idea :
Using something like the above epoxy the top surface to the inside walls.
(Some form of disposable roller would be good for applying the glue I'd say.)
Due to the bottom layer you will end up with a dual layer sandwich.
Last edited:
I have an image in my head from a picture of a sliced open B&W 300 series speaker from back in the 90s with very radical interior wall treatments.
What about 1/8" birch plywood and a couple of layers of carbon fiber. One other idea would be to use a lot of pieces of bambo for extensive cross bracing but have
a lot of holes drilled in the bambo.
a lot of holes drilled in the bambo.
Most of these ideas are taking a difficult approach, strengthening the wall materials instead of engineering the braces to effectively counter the exact problematic forces.
Look carefully at the "matrix' bracing used in some B&W speakers. The air pressure is trying to blow up the box like a ballon and then suck the air out to collapse it. Good bracing doesn't just stiffen or strengthen the wall panels, it must connect the opposite walls. I used to work in a liquor store, and noted how a case of wine bottles was boxed. Inside were pieces of cardboard to divide the box into individual sections for each bottle. Half the cardboard pieces were slotted on the top and were oriented left to right, the other half were slotted on the bottom and oriented front to back. When assembled, if you glued it then it would make a nice matrix of braces connecting opposite walls.
Of course, inside a speaker such braces need to be epoxied and filleted (or welded??) to make solid connections where the solid sections fit into the slots, and most important the ends of the braces must connect solidly to the cabinet walls (preferabley in routed or dado grooves).
There are a few special considerations...the brace material used mostly in tension and compression can be thin and light (like masonite or sheet metal). But if you make all the brace panels the same they can be like the strings of a guitar tuned to one note, and their sympathetic resonance amplified by the cabinet walls like a guitar's sound board. So I damp them with liquid rubber or undercoating and I drill large holes in them so that internal pressure inequalities or wavefronts don't tend to activate them into motion. Then I stuff the voids. Placing stuffing where you would place the bottles if this were a wine crate, you can indeed make tuned cavities if you so desire...these can be acoustical structures if the box dimensions allow. I like to somewhat randomize the braces.
Another interesting approach to making good enclosures of light thinwall materials invovles some kind of preload. Remembering again that the speaker wants to inflate your cabinet like a balloon and deflate it, and that you want to counter that tendency, you can use steel cables or steel rods anchored to opposed cabinet walls to significantly strenghten it without adding too much weight or taking much volume from the cabinet. Sometimes a threaded rod thru opposing cabinet walls does wonders and you can hear the difference as you tighten down on the nuts to preload the wall panels. I used to think some big folded horns had a distrubing sound, but most of that was the large panels resonating; threaded rods are especially useful for stiffening bass horns without interfering significantly with the desired sound waves.
There's a theory that a flaccid panel at rest vibrates easily but pulled into tension it's much stiffer. I haven't investigated or thought about it sufficiently to have an opinion. But imagine some way to string a thin steel cable inside a cabinet so that it acts like a big block and tackle pulley system, and some tension on the cable from a turnbuckle exerts thousands of pounds of force on the walls. That's not going to be easy to inflate.
Just some thoughts.
Look carefully at the "matrix' bracing used in some B&W speakers. The air pressure is trying to blow up the box like a ballon and then suck the air out to collapse it. Good bracing doesn't just stiffen or strengthen the wall panels, it must connect the opposite walls. I used to work in a liquor store, and noted how a case of wine bottles was boxed. Inside were pieces of cardboard to divide the box into individual sections for each bottle. Half the cardboard pieces were slotted on the top and were oriented left to right, the other half were slotted on the bottom and oriented front to back. When assembled, if you glued it then it would make a nice matrix of braces connecting opposite walls.
Of course, inside a speaker such braces need to be epoxied and filleted (or welded??) to make solid connections where the solid sections fit into the slots, and most important the ends of the braces must connect solidly to the cabinet walls (preferabley in routed or dado grooves).
There are a few special considerations...the brace material used mostly in tension and compression can be thin and light (like masonite or sheet metal). But if you make all the brace panels the same they can be like the strings of a guitar tuned to one note, and their sympathetic resonance amplified by the cabinet walls like a guitar's sound board. So I damp them with liquid rubber or undercoating and I drill large holes in them so that internal pressure inequalities or wavefronts don't tend to activate them into motion. Then I stuff the voids. Placing stuffing where you would place the bottles if this were a wine crate, you can indeed make tuned cavities if you so desire...these can be acoustical structures if the box dimensions allow. I like to somewhat randomize the braces.
Another interesting approach to making good enclosures of light thinwall materials invovles some kind of preload. Remembering again that the speaker wants to inflate your cabinet like a balloon and deflate it, and that you want to counter that tendency, you can use steel cables or steel rods anchored to opposed cabinet walls to significantly strenghten it without adding too much weight or taking much volume from the cabinet. Sometimes a threaded rod thru opposing cabinet walls does wonders and you can hear the difference as you tighten down on the nuts to preload the wall panels. I used to think some big folded horns had a distrubing sound, but most of that was the large panels resonating; threaded rods are especially useful for stiffening bass horns without interfering significantly with the desired sound waves.
There's a theory that a flaccid panel at rest vibrates easily but pulled into tension it's much stiffer. I haven't investigated or thought about it sufficiently to have an opinion. But imagine some way to string a thin steel cable inside a cabinet so that it acts like a big block and tackle pulley system, and some tension on the cable from a turnbuckle exerts thousands of pounds of force on the walls. That's not going to be easy to inflate.
Just some thoughts.
I have an image in my head from a picture of a sliced open B&W 300 series speaker from back in the 90s with very radical interior wall treatments.
Not wall treatments, but study their "matrix" bracing! Thin materials connecting opposite walls.
I would think that If you have the ability to build a jig for bent wall lamination, that would be the best way to get thin wall and minimize the need for bracing. Using a synthetic resin to bond the layers would add damping into the wall structure. You could even weave a lattice layer then use a nice veneer to finish the outside.
Speakers are small and light because they have to be shipped from China, the smaller the more goes into a container. Less material makes for cheaper production. They use drivers with no magnet weight too. Utter crap. Real audiophile speakers have thick walls and are very very heavy.
Real audiophile speakers have thick walls and are very very heavy.
That is a tendency, but not a requirement, or even a good goal.
dave
- Status
- Not open for further replies.
- Home
- Loudspeakers
- Multi-Way
- The importance of thin-wall cabinets for small speakers, any solutions?