Quite a lot of DIY amplifiers have their heat-sink(s) mounted externally, such as on the sides of the chassis (in many cases, they 'are' the sides); this all seems very sensible. Conversely, quite a lot (probably most) domestic/hi-fi amps that one can buy have the heat-sinks inside the chassis, with vents below and above; this is visually quite neat (and possibly has some minor safety advantages if the heatsink got very hot). Neither is 'wrong', they are just different choices.
To that end, I'm wondering is how much of a performance reduction is there likely to be if using a heat-sink internally? Assuming a very open wire grill were used below and above, is it likely to impede convection enough to make much difference?
Thanks,
Kev
To that end, I'm wondering is how much of a performance reduction is there likely to be if using a heat-sink internally? Assuming a very open wire grill were used below and above, is it likely to impede convection enough to make much difference?
Thanks,
Kev
I have wondered this too.
I suspect the criteria are cost and amount of power dissipation. Internal heatsinks are cheaper, but have to fit inside the enclosure.
I am amazed by the custom PCBs, heatsinks, and enclosures in DIY amplifiers. Those weren't available to hobbyists back when I was designing and building amplifiers.
Ed
I suspect the criteria are cost and amount of power dissipation. Internal heatsinks are cheaper, but have to fit inside the enclosure.
I am amazed by the custom PCBs, heatsinks, and enclosures in DIY amplifiers. Those weren't available to hobbyists back when I was designing and building amplifiers.
Ed
I never quite understood the utility of the "internal heatsink". From a thermodynamic point of view, the way to manage heat is to remove or eject it from the hot area (the component generating it) to a cold area. Where is the "cold area"? I can tell you it is NOT inside the chassis! It's the room environment. The only means to move heat in this scenario are convection or conduction. Conduction moves heat by passing it through one material to another one, e.g. one solid to another like the component to the heat sink. Convection is moving heat out into the air by contacting a material with air. Remember, the only air that is cool is outside the chassis in the room. So with an internal heat sink you use convection cooling to move the heat from the component to the air inside the chassis via the heatsink. Now the problem is that the air inside the chassis is mostly just staying there, so it just heats up. This reduces the thermal gradient between the heat sink and the air, which reduces the ability to move heat energy across the metal-air junction. Air can "move" via any openings in the chassis, but your typical amplifier will only have a few slots in the top and probably none in the bottom. So how is air going to move/flow through the chassis with that kind of setup? Answer: it doesn't. External heat sinks are are much better option from this standpoint. But they do allow for the possibility of shock if the energized component comes in contact with the heatsink metal. I would guess that this is why they are not so common, but I cannot say for sure. It might just be a cost thing, since an internal heat sink can be made from pretty thin metal and does not need to be mechanically robust like an external one.
It really depends on dissipation. If heat produces is small (think class d, dacs), then visually you may prefer to have heatsinks inside as heat dissipated is not that much, and vents handle it. For class A for example, most of the power consumed is turned to heat. So it can get really hot, and you want heatsinks outside due to so much heat dissipating, and within the case ambient temperature would rise by a lot and quickly.
The trouble with grills and small vents is that dust and webs may obstruct them reducing the air flow. Periodically I must to clean the refrigerator's condenser because lots of dust and bugs accumulate in it.
Heat flow is driven by temperature difference. Colder heatsink means more heat flow from the device to the heatsink.
if the energized component comes into contact with the heatsink the fuse will/should blow...But they do allow for the possibility of shock if the energized component comes in contact with the heatsink metal. I would guess that this is why they are not so common, but I cannot say for sure. It might just be a cost thing, since an internal heat sink can be made from pretty thin metal and does not need to be mechanically robust like an external one.
i have always been a fan of Bryston's philosophy with respect to passive cooling...as much heatsink area outside the box as possible is the best...
Last edited:
Thanks everyone, some very good points raised here and there.
Yes, there are some fairly poor implementations of internal heat-sinks and grills, cutting corners on both the heat-sink size and even the open vented areas. I suppose for some manufacturers the life expectancy of the semiconductors would only need to exceed the warranty period.
Suffice it to say that if I had chosen to do this then there would have been 'extremely' open vents below and above, so I'm sure it would have worked. However due to the helpful points raised, I'm rapidly going off the idea even if well implemented; the disadvantages still seem notable. The heatsinks I have are robust, so they don't need to be inside for mechanical reasons, and are large enough that they shouldn't get dangerously hot to touch.
I suppose ideally in a single heat-sink monoblock design it would be at the front or maybe down one side of the enclosure. But I might put it at the back for aesthetic reasons. I've no intention of cramming the amp into a cupboard or enclosed hi-fi rack, so there'd still be plenty of open air around it.
Thanks again,
Kev
Yes, there are some fairly poor implementations of internal heat-sinks and grills, cutting corners on both the heat-sink size and even the open vented areas. I suppose for some manufacturers the life expectancy of the semiconductors would only need to exceed the warranty period.
Suffice it to say that if I had chosen to do this then there would have been 'extremely' open vents below and above, so I'm sure it would have worked. However due to the helpful points raised, I'm rapidly going off the idea even if well implemented; the disadvantages still seem notable. The heatsinks I have are robust, so they don't need to be inside for mechanical reasons, and are large enough that they shouldn't get dangerously hot to touch.
I suppose ideally in a single heat-sink monoblock design it would be at the front or maybe down one side of the enclosure. But I might put it at the back for aesthetic reasons. I've no intention of cramming the amp into a cupboard or enclosed hi-fi rack, so there'd still be plenty of open air around it.
Thanks again,
Kev
Consumer products sold in USA used to be tested to a FTC spec. Something like a 1 hour soak at 1/4 power then a few minutes at full power. If it met that, could be advertised at the full power. I tried to run my 1970 dynaco ST120 (60 w/ch stereo) with internal sinks and a grill at about 20 watts/ch for 3.5 hours and it burned the output transistors.To that end, I'm wondering is how much of a performance reduction is there likely to be if using a heat-sink internally? Assuming a very open wire grill were used below and above, is it likely to impede convection enough to make much difference?
OTOH there are 24/7 power rated products with an internal sink. A Peavey MMA-875 warehouse amp has internal heatsinks, grills top & bottom, and 1" tall (25mm) feet. It is rated at 75 watts. Which would be about as much as you could run with interal sinks all day, IMHO.
PA amps with a fan can run much more of course. A PV-4c has 120 w/ch and a cs800s has about 260 w/ch with internal sinks. The fan runs slowly at low power and fast after the sink heats up. A QSC CX300 has 150 w/ch and a really noisy fan that runs all the time.
Last edited:
The horizontal position of the fins reduces the efficiency of the radiator.Photo of a Norge amplifier with isolated external heatsink
Attachments
well i for one would like to see a firmly measured correlation to what your suggesting...conventional wisdom does suggest that a vertical topology would be better but to me it's more about surface area versus air flow in order to achieve sufficient cooling to keep the highest dissipation devices in their Safe Operating Area Range (S.O.A.R.)
You are correct in your observationsThe horizontal position of the fins reduces the efficiency of the radiator.
I've always understood that as convection currents (in free air) tend towards the vertical, vertical fins facilitate them moving up the face of the sink. In practice, I believe that a little turbulence 'might' help by mixing the flowing air, since it doesn't conduct well (to spread the heat into itself). But large horizontal surfaces would tend to block or redirect the flow, rather than just slightly disrupt the smoothness of it.
But either way, my heatsinks have vertical fins, so I'll be going with those in any case. I forget the model number but they're some conrad ones that look vaguely like this:
But either way, my heatsinks have vertical fins, so I'll be going with those in any case. I forget the model number but they're some conrad ones that look vaguely like this:
There is also this kind of design, which might get over some of the objections to internally positioned heatsinks, though probably not all of them:
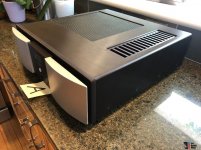
(image just found at random on the net to illustrate the general idea)
I've seen arguments that a chimney effect can be created, increasing convection current speeds. But presumably this is quite critically related to things like the spacing and temperature to get right, and i've no confidence in my ability to do that.
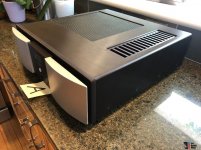
(image just found at random on the net to illustrate the general idea)
I've seen arguments that a chimney effect can be created, increasing convection current speeds. But presumably this is quite critically related to things like the spacing and temperature to get right, and i've no confidence in my ability to do that.
Last edited:
- Home
- Amplifiers
- Solid State
- Internal vs External Heat-Sinks