Hi AJT,
This could turn out to be a lengthy discussion too!
Hi Bob,
Excellent topic! Very rarely talked about.
I'm of the same mind there ... There is a balancing act between necessary but competing design requirements. It's all about how that balance comes out.
... and there is the balance and rational behind it. I would accept that BTW.
I would cautiously agree with you. I have serviced amplifiers where the coil has been cooked, some from the amp going DC. You just know the speakers weren't very happy about it either!
I'm not a physicist, but I do know that heating copper wire will raise the resistance. Will this matter considering the crossover and voice coils will change even more since they are longer lengths of copper wire? Another decision to make.
Sounds good, and practical. My choice would be #5, a larger gauge, two layer design. I think it delivers the best compromise of board space, IR losses and cost.
Great pints to consider ... I mean points ...
However, the 22 ga wire is much higher in resistance than the larger ga wire to start with. When then does the HF losses equal the losses at 22 ga. You also have skin effect on the speaker wire, cross-over components and ... the voice coils. Where are the biggest losses and how great are they? This might be valid if you're really thinking a 22 ga wire coil is on the table. I dropped it from consideration a while ago. 🙂
Probably. But what is the maximum displacement? Probably not very much, and a little silicone (in lengthwise strips) would damp them.
Higher in the larger coils due to stiffness to weight ratio. However, coil vibration can be damped. Also, the power transformer probably puts out more noise, and the output coil vibration occurs in sync with loud music passages - you wouldn't hear them anyway.
No, the ceramic capacitors were louder.
I have. Normally they use magnet wire which comes pre-coated.
But heat shrink is expensive, and it will block air flow to cool the coil. The smaller coils would require more air cooling than the larger ones as more heat leaves via the leads in large ga coils.
Sure, if only to conclude it isn't an issue. This issue is easy to solve with damping material that does not block too much air flow. Silicone. Lovely stuff.
Excellent topic! Thanks for bringing it up.
-Chris
Hi Chris,
Thanks for your detailed and thoughtful response. This is exactly the kind of discussion I wanted to provoke with my Devil's Advocate position.
I am not familiar with magnet wire that is pre-coated (presumably with a coil doping equivalent). How does this pre-coating work to hold the coil elements together after winding? For example, does it need to be set with the application of heat? If it was simply a ready-to-use adhesive, I would not think it would be strong enough and reliable enough for the purpose.
Have any DIYers here used this pre-coated magnet wire, or used coil doping on output coils?
Cheers,
Bob
perhaps Bob can devote an entire chapter or at the very least an appendix...😀
all the while, i was thinking that the output coils were no big deal till now...
i guess you learn something new each day....
AFAIR, Daniel Meyer also suggested this in in Tigersaurus 250 watter build...
6 turns of #16 magnet wire on the body of one of the large filter caps.
ant those caps were at least 2.5 inches in diameter...
![]()
So you think I should spend some ink on this in my second edition?
If so, the feedback here would certainly help me to get it right.
I think Dan Meyer's approach to winding the output coil on the electrolytics has been pretty much considered to have been a really bad idea.
Cheers,
Bob
Magnet wire is coated with a heat set coating. After winding the wire is usually held in place with zip ties or such and baked in an oven. Unless you exceed the oven temperature the coils will be perfectly physically stable. If done correctly to the proper temperature and with enough time to make sure the entire mass is baked the coils will be physically bonded throughout the winding. If there was any resonance of the coil stack it would have to be the entire mass that was resonating and not a single wire strand. I see no method for that to happen unless the coil is not baked. Adding just silicone or epoxy to the outside of an air core coil of wires would not produce the same monolithic mass as an oven baked coil. You would have to vacuum impregnate the coil stack if you want to use a liquid epoxy and be sure that it was a monolithic whole, whether this would be audible is a question but there could clearly be mechanical resonance within the coil with a loosely wound inductor.
for minimum coil resistance one needs a coil diameter to coil length ratio of roughly 4.
Any coil that is longer than ~25% of the coil diameter will have a higher resistance.
Using 13.92T in 3 layers on a 8.26mm diameter bobbin that is 3.93mm wide one gets 2.0005uH and 11.3milli-ohms for 516.2mm of wire in the coil. the overall diameter will be 15.34mm. One would have to add a bit more length and resistance for the tails.
This is arrived at using Wheeler's formula: L = 7.87M²N² / 3M+9B+10C, in nH when dims are in mm
where M= mean diameter, N= Turns, C= coil height, B= coil width.
M+C = overall diameter, M-C = bobbin diameter
The numbers are a bit odd since I adjusted dimensions until the Inductance L near enough equaled 2uH.
0.7mm wire results in 0r0201
1mm wire results in 0r0113
1.2mm wire results in 0r0085
1.5mm wire results in 0r0059
1.8mm wire results in 0r0044
These are the minimum resistances for an air-cored copper coil of 2uH
Longer coils will have more resistance.
Adding on a correction for skin depth will generally add less resistance than changing to a long coil.
Hi Andrew,
Coil aspect ratio is a very good issue. This is why most of the example designs I showed have aspect ratio in the vicinity of 1:1. I have seen many amplifier coils where the length is longer than the diameter, which is the direction in which we do not want to go.
Doug Self has pointed out that the coil efficiency as a function of aspect ratio (diameter/length) has a very broad peak, with its maximum occurring at about 2.2:1. According to his data, the coil efficiency is about 92% at an aspect ratio of 1:1. This is not bad, especially if we are not too obsessed with getting extremely low coil resistance beyond the point where its value-added is questionable.
I assume that the on-line coil calculators use Wheeler's formula or a close equivalent, but I don't know for sure.
Cheers,
Bob
A bit about output inductors wound around caps
The Dynaco Stereo 120 made its output inductor by winding wire around C7, the output coupling capacitor. It was a single rail design.
The original inductor is 74 inches of 16 AWG insulated solid wire wrapped around C7, a 2" diameter capacitor. Using the Wheeler formula, that calculates out to about 5 uH or so. Actual measurements show a lot closer to 1.0 uH. What's going on?
Recall that the coil is wrapped around the cap. The cap consists of two rolled up conductive sheets separated by a dielectric. It looks like a loosely coupled one turn secondary to the primary of the speaker inductor wrapped around the cap. That reflected impedance drops the inductance, making it much less than you'd expect. I took network analyzer measurements and fitted a model in the region from 1kHz to 10 MHz. The model looked like the enclosed picture.
More info can be found here:
Replacement Capacitors
The Dynaco Stereo 120 made its output inductor by winding wire around C7, the output coupling capacitor. It was a single rail design.
The original inductor is 74 inches of 16 AWG insulated solid wire wrapped around C7, a 2" diameter capacitor. Using the Wheeler formula, that calculates out to about 5 uH or so. Actual measurements show a lot closer to 1.0 uH. What's going on?
Recall that the coil is wrapped around the cap. The cap consists of two rolled up conductive sheets separated by a dielectric. It looks like a loosely coupled one turn secondary to the primary of the speaker inductor wrapped around the cap. That reflected impedance drops the inductance, making it much less than you'd expect. I took network analyzer measurements and fitted a model in the region from 1kHz to 10 MHz. The model looked like the enclosed picture.
More info can be found here:
Replacement Capacitors
Attachments
using the capacitor as a temporary bobbin has the big advantage that it gives a large diamter coil and this will require fewer Turns. This will get closer to that 4:1 ratio and will result in lower resistance................I think Dan Meyer's approach to winding the output coil on the electrolytics has been pretty much considered to have been a really bad idea.
.............
D.Self is referring to single layer coils which because they don't have the "squarish" coil bundle cannot be near the lowest resistance.....................
Coil aspect ratio is a very good issue. ....................
Doug Self has pointed out that the coil efficiency as a function of aspect ratio (diameter/length) has a very broad peak, with its maximum occurring at about 2.2:1. ................
He is giving guidance of how to get better efficiency from a higher resistance coil.
He does show a resistance optimised coil in fig14.12, but this shape can never be approached with a single layer coil unless it has ONLY 1Turn.
A 2layer coil would have 2layers each with 2Turns, i.e. a 4Turn coil.
A 3layer coil is 3Turns on each layer giving 9Turns.
All these "squarish" coils get very close to the resistance predicted by Wheeler's formula.
It is because of this bundling into the square coil format that I am concerned about parasitic capacitance.
I suspect that a more spaced out coil will have lower capacitance and that this may result in a coil that behaves as an inductor over a much wider bandwidth.
i.e. a single layer coil with gapped Turns may perform better due to lower capacitance rather than perform badly due to extra resistance.
Magnet wire is coated with a heat set coating. After winding the wire is usually held in place with zip ties or such and baked in an oven. Unless you exceed the oven temperature the coils will be perfectly physically stable. If done correctly to the proper temperature and with enough time to make sure the entire mass is baked the coils will be physically bonded throughout the winding. If there was any resonance of the coil stack it would have to be the entire mass that was resonating and not a single wire strand. I see no method for that to happen unless the coil is not baked. Adding just silicone or epoxy to the outside of an air core coil of wires would not produce the same monolithic mass as an oven baked coil. You would have to vacuum impregnate the coil stack if you want to use a liquid epoxy and be sure that it was a monolithic whole, whether this would be audible is a question but there could clearly be mechanical resonance within the coil with a loosely wound inductor.
Thanks Kindhornman,
This is great information. It makes eminent sense.
Does anyone here know if any DIYers have used coated magnet wire and baked their coils?
Can I buy this coated magnet wire at DigiKey or Mouser?
Cheers,
Bob
using the capacitor as a temporary bobbin has the big advantage that it gives a large diamter coil and this will require fewer Turns. This will get closer to that 4:1 ratio and will result in lower resistance.
Dan Meyer did not use the electrolytic as a temporary bobbin. He put the coil on the capacitor permanently. We do need to be mindful of what is inside the coil if it is not truly air, especially if it is conductive.
Cheers,
Bob
Recall that the coil is wrapped around the cap. The cap consists of two rolled up conductive sheets separated by a dielectric.
The aluminum capacitor body probably shields the cap internals quite well while providing a solid shorted turn to the windings.
D.Self is referring to single layer coils which because they don't have the "squarish" coil bundle cannot be near the lowest resistance.
He is giving guidance of how to get better efficiency from a higher resistance coil.
But most of the output coils we deal with are single-layer. In that respect, I'm thinking that what he stated is correct and relevant.
Directly related to this point is the fact that, for a given coil diameter and wire gauge, inductance does not go up as fast as the square of the number of turns for a single-layer coil.
For a 2-layer coil, we also know that we are more efficient in terms of uH per milli-ohm. This also largely fits into the notion that the larger aspect ratio (diameter/length) is more efficient, since going to 2 layers for a given number of turns increases the aspect ratio.
Cheers,
Bob
Hi Bob,
I have never bothered to bake the coil after winding. I have seen hot glue, epoxy and silicone used to keep the wires from vibrating. One reason that I like silicone is that it requires no additional steps to use and comes straight out if its tube. The windings are not locked together as you pointed out, but we don't need this. The coils are heavily damped by the silicone and you end up with a mass that has high internal damping. Leaving spaces will allow heat dissipation while achieving the goal of low to no noise from that component.
I don't think this is a true concern anyway. Aside from the coil rubbing off the coating and then shorting, any noise will only occur when the speaker is seeing a lot of energy. The tiny amount of noise would be drowned out by the acoustic noise, and by the power transformer.
Magnet wire is available from the usual sources. The fact that it is called "magnet wire" tells you that it is coated as the manufacturer has created it specifically to wind coils with. The coatings are normally reddish or yellowish, and must be scraped or burned off in order to solder it.
Some mention of coil winding and the optimal design would be nice to see in print in your book. It should be treated even if its only a couple paragraphs.
-Chris
I have never bothered to bake the coil after winding. I have seen hot glue, epoxy and silicone used to keep the wires from vibrating. One reason that I like silicone is that it requires no additional steps to use and comes straight out if its tube. The windings are not locked together as you pointed out, but we don't need this. The coils are heavily damped by the silicone and you end up with a mass that has high internal damping. Leaving spaces will allow heat dissipation while achieving the goal of low to no noise from that component.
I don't think this is a true concern anyway. Aside from the coil rubbing off the coating and then shorting, any noise will only occur when the speaker is seeing a lot of energy. The tiny amount of noise would be drowned out by the acoustic noise, and by the power transformer.
Magnet wire is available from the usual sources. The fact that it is called "magnet wire" tells you that it is coated as the manufacturer has created it specifically to wind coils with. The coatings are normally reddish or yellowish, and must be scraped or burned off in order to solder it.
Some mention of coil winding and the optimal design would be nice to see in print in your book. It should be treated even if its only a couple paragraphs.
-Chris
Last edited:
In H/K integrated amps there is clear brownish stuff melted onto the coils that seems to be rosin. I actually melted some of it off to use it on another coil! Easy to do with a lighter.
Search at Mouser provided
Belden Wire & Cable magnet wire Hook-up Wire | Mouser
One of my college summer jobs was as a motor re-winder/rebuilder, messy job, we baked the coils in the hot oven then dropped in the varnish tank, then back in the oven to bake it in. Fans going all summer long in that literal sweat shop, so I have lots of 3phase-winding coil wire from my winding mistakes 🙂
Varnish is the proven way to impregnate a coil, but it is stinky stuff, next best would be thermally conductive epoxy resin. Cheaper yet asphalt tar as the ballast folks use. Tighter windings are better than loose wound ones.
Belden Wire & Cable magnet wire Hook-up Wire | Mouser
One of my college summer jobs was as a motor re-winder/rebuilder, messy job, we baked the coils in the hot oven then dropped in the varnish tank, then back in the oven to bake it in. Fans going all summer long in that literal sweat shop, so I have lots of 3phase-winding coil wire from my winding mistakes 🙂
Varnish is the proven way to impregnate a coil, but it is stinky stuff, next best would be thermally conductive epoxy resin. Cheaper yet asphalt tar as the ballast folks use. Tighter windings are better than loose wound ones.
Hi Bob,
I have never bothered to bake the coil after winding. I have seen hot glue, epoxy and silicone used to keep the wires from vibrating. One reason that I like silicone is that it requires no additional steps to use and comes straight out if its tube. The windings are not locked together as you pointed out, but we don't need this. The coils are heavily damped by the silicone and you end up with a mass that has high internal damping. Leaving spaces will allow heat dissipation while achieving the goal of low to no noise from that component.
I don't think this is a true concern anyway. Aside from the coil rubbing off the coating and then shorting, any noise will only occur when the speaker is seeing a lot of energy. The tiny amount of noise would be drowned out by the acoustic noise, and by the power transformer.
Magnet wire is available from the usual sources. The fact that it is called "magnet wire" tells you that it is coated as the manufacturer has created it specifically to wind coils with. The coatings are normally reddish or yellowish, and must be scraped or burned off in order to solder it.
Some mention of coil winding and the optimal design would be nice to see in print in your book. It should be treated even if its only a couple paragraphs.
-Chris
What kind of silicone are you talking about and how do you smooth it out over the coil? I assume you are not talking about the popular GE Silicone in a tube we use around the house and then using your finger or some kind of appliance to smooth it out.
I understand that DIY coil dope can be made by dissolving ping pong balls in acetone. Finger nail polish can also be used, but it is apparently not as durable.
We do not want to spread the coil out because that reduces the inductance. We want it to be close-wound with ideally no space between the windings.
It is not the acoustic noise of a singing coil we object to. It is the fact that such singing is a symptom that electromechanical vibration is occurring in response to the signal current, which cannot be a good thing. How bad it is on the audio signal is the question.
The coating that makes it magnet wire that you refer to is the enamel insulating layer (magnet wire is also called enameled wire). I don't think that is the coating that acts to bond the wires together when baked.
Cheers,
Bob
Here in the States one of the major supplies is MWS Wire Industries.
Welcome to MWS Wire Industries
There is any information that you may need on their site.
All the perfect lay coils i have had made by Erse in the past were always baked. I have personally made many hand wound coils on a simple form that I had mounted on a low speed lathe made for watch makers. When I was done I would tie wrap them and coat them with hot melt glue. I never had a problem but with a speaker making noise I don't know that you could ever hear any noise over the sound.
Another method for making inductors for speakers that I have used and perhaps it isn't technically the optimum is to wind the coil on a 1/4" or 3/8" wooden dowel. The windings don't have the large air core center section but one advantage is that starting with a much smaller diameter the actual length of wire needed to make a turn is much less than a bobbin type winding. The result is that the dc resistance is less than a longer wire length of the air cored coil of the same Mh value. When you are making very high value inductors for a low frequency network that can be a lot of difference in wire length. I leave the wooden dowel in the center and use the dowel to mount the coil to the board. I can say I never measured the difference in capacitance using this method. It is very easy to make a coil this way on a lathe with two end plates to limit the length of the coil and wind until you reach your required inductance. I'm not sure that all the formulas for coil dimensions are not actually based on DCR values and don't take into account in a network we are working with ACR values.
Welcome to MWS Wire Industries
There is any information that you may need on their site.
All the perfect lay coils i have had made by Erse in the past were always baked. I have personally made many hand wound coils on a simple form that I had mounted on a low speed lathe made for watch makers. When I was done I would tie wrap them and coat them with hot melt glue. I never had a problem but with a speaker making noise I don't know that you could ever hear any noise over the sound.
Another method for making inductors for speakers that I have used and perhaps it isn't technically the optimum is to wind the coil on a 1/4" or 3/8" wooden dowel. The windings don't have the large air core center section but one advantage is that starting with a much smaller diameter the actual length of wire needed to make a turn is much less than a bobbin type winding. The result is that the dc resistance is less than a longer wire length of the air cored coil of the same Mh value. When you are making very high value inductors for a low frequency network that can be a lot of difference in wire length. I leave the wooden dowel in the center and use the dowel to mount the coil to the board. I can say I never measured the difference in capacitance using this method. It is very easy to make a coil this way on a lathe with two end plates to limit the length of the coil and wind until you reach your required inductance. I'm not sure that all the formulas for coil dimensions are not actually based on DCR values and don't take into account in a network we are working with ACR values.
Last edited:
So you think I should spend some ink on this in my second edition?
If so, the feedback here would certainly help me to get it right.
I think Dan Meyer's approach to winding the output coil on the electrolytics has been pretty much considered to have been a really bad idea.
Cheers,
Bob
now that the topic is being discussed here, i think it is a good idea to put it in your book....
to be honest, i never followed Dan Meyer's coil suggestion, i installed them right at the speaker binding posts....
In H/K integrated amps there is clear brownish stuff melted onto the coils that seems to be rosin. I actually melted some of it off to use it on another coil! Easy to do with a lighter.
i used shrinkable tubing in some of my coils....
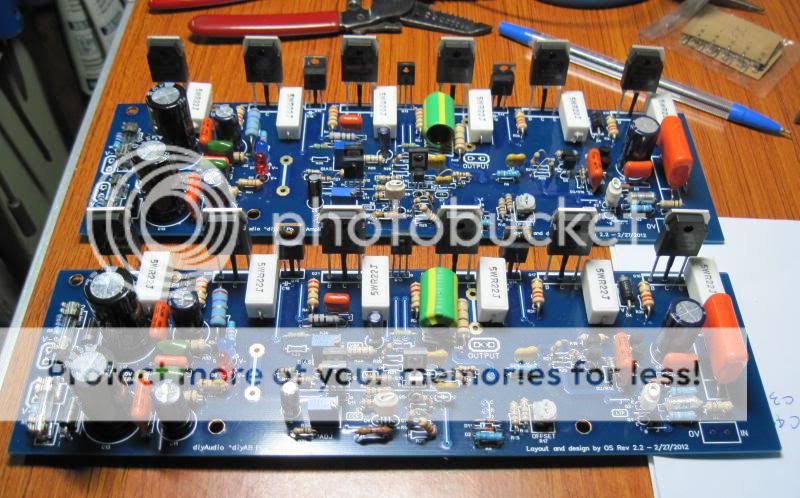
- Home
- Amplifiers
- Solid State
- Bob Cordell's Power amplifier book