Hi,
i've been looking for some information of how to calculate, and desing a bass reflex speaker. But all books i look, they only talk about diameter, only of cilindrical ports.
But what about if i want to design a speaker with a rectangular port? wich formulas do i have to use?? Or is it a cut & try solution only?
how can i calculate, or estimate if you want to put one, two, four or how many ports you want? Or i can put as many as i want aslong as they verify they formulas???
i found this, can anyone verify this is correct? haven't seen it in any of the 3 books i looked 🙂
Port Length
The port length required to tune a volume of air to a specific frequency can be calculated by using the following equation: Lv = (23562.5*Dv^2*Np/(Fb^2*Vb))-(k*Dv)
where,
Dv = port diameter (cm)
Fb = tuning frequency (Hz)
Vb = net volume (litres)
Lv = length of each port (cm)
Np = number of ports
k = end correction (normally 0.732)
==================================================
i have this formula from a good book, but for circular ports:
Lv=2340*(dv^2/fb^2*Vab) - 0'73dv
looks like it....but..... still not sure :S :S :S
thanks for your help in advance!!
keep up this cool forum 🙂)
i've been looking for some information of how to calculate, and desing a bass reflex speaker. But all books i look, they only talk about diameter, only of cilindrical ports.
But what about if i want to design a speaker with a rectangular port? wich formulas do i have to use?? Or is it a cut & try solution only?
how can i calculate, or estimate if you want to put one, two, four or how many ports you want? Or i can put as many as i want aslong as they verify they formulas???
i found this, can anyone verify this is correct? haven't seen it in any of the 3 books i looked 🙂
Port Length
The port length required to tune a volume of air to a specific frequency can be calculated by using the following equation: Lv = (23562.5*Dv^2*Np/(Fb^2*Vb))-(k*Dv)
where,
Dv = port diameter (cm)
Fb = tuning frequency (Hz)
Vb = net volume (litres)
Lv = length of each port (cm)
Np = number of ports
k = end correction (normally 0.732)
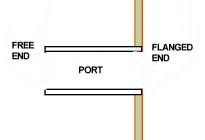
i have this formula from a good book, but for circular ports:
Lv=2340*(dv^2/fb^2*Vab) - 0'73dv
looks like it....but..... still not sure :S :S :S
thanks for your help in advance!!
keep up this cool forum 🙂)

Hi,
i've been looking for some information of how to calculate, and desing a bass reflex speaker. But all books i look, they only talk about diameter, only of cilindrical ports.
But what about if i want to design a speaker with a rectangular port? wich formulas do i have to use?? I found...
Lv = (23562.5*Dv^2*Nv/(Fb^2*Vb))-(k*Dv)
where,
Dv = port diameter (cm)
Fb = tuning frequency (Hz)
Vb = net volume (litres)
Lv = length of each port (cm)
Nv = number of vents
k = end correction (normally 0.732)
i [also] have this formula from a good book, but for circular ports:
Lv=2340*(dv^2/fb^2*Vab) - 0'73dv
The second formula is for measurements in mm and volume in liters.
The Nv business is to correct the area for multiple ports, so if you take it out and allow for a factor of 10, for mm vs cm, you will see the formulas are essentially the same except for the constant. I think the correct value for the constant should be about 23610 in the first and 2361 in the second, but you often see values between 2340 and 2350, so there might be a "fudge factor" worked in. Small suggested to use 2350 - so 23500 for the first formula..
I think the first formula has an error in that it doesn't correct for the end correction properly - should read:
Lv = (23500*Dv^2*Nv/(Fb^2*Vb))-(k*Dv*sqrt(Nv))
This is for cylindrical ports. Remember the area of a circle Av=pi*Dv^2, so Dv^2=Av/pi and Dv=sqrt(Av/pi) so to convert the formula for area you get
Lv=(23500*Av*(Nv/pi)/(Fb^2*Vb))-(k*sqrt(Av*Nv/pi))
For a rectangular port, you get Av=Wv*Hv (width times height), so:
Lv=(23500*Wv*Hv*(Nv/pi)/(Fb^2*Vb))-(k*sqrt(Wv*Hv*Nv/pi))
...assuming I didn't make any substitution errors. 😉
Have fun!
Last edited:
The Subwoofer DIY Page - Port Calculations
That should help.
But do notice, cross sectional area will be the same, but since You are using rectangular ports.
The difference is simply, that the rectangular port needs bigger cross sectional area than a cylindrical one. It is couse of different flow of air.
Allso, You should notice that no calculation will ever yield what You get in real life.
In other words, You may do Your math as best as it can be, but when You build it, it will be not realy accurate.
Calculations are just to give a starting point. Suposedly cylindrical pots can be made to be adjustable in lenght with ease.
It has the benefit to be adjusted after building the whole box, so You can set Your desired tuning freqvency.
vent tuning
while this article has its own flaws, it does verifys (correctly) that calulcations and real life are 2 different things.
Usualy the simulation/calculation toosl just give a nice starting point.
Goal is to get the largest possible crossectional area You can fit into the box, get a more or less close tuning freqvency, then mesure What You done and adjust Your port till You get what You where looking for.
The process of mesuring the tuning feqvency is not hard. a simple multimeter can do the job.
As tuning freqvency will have an impedance peak.
Port placement has its own effects too, specialy for the non-cylindrical ports.
They can act as if they where a LOT longer than they are actualy.
That is realised as a lower tuning freqvency then expected.
Good news is, they can be cut down to size with ease, and that is what You need to do in order to get a higher tuning freqvency.
My absolute not scientific approach is simply using the maximal crossectional area regardles if its cylindircal, or not.
Allso, in my calculations value of k = end correction (normally 0.732) is just 0.7
I done that by experience. MAny times I got it closer with 0.7 end correction to real life, many times close enough to simply not worth the effort to trimm it a bit shorter.
-> notice, the k value i use is not at all verifyd by anyone, not even me. it is just my personal practice.
That should help.
But do notice, cross sectional area will be the same, but since You are using rectangular ports.
The difference is simply, that the rectangular port needs bigger cross sectional area than a cylindrical one. It is couse of different flow of air.
Allso, You should notice that no calculation will ever yield what You get in real life.
In other words, You may do Your math as best as it can be, but when You build it, it will be not realy accurate.
Calculations are just to give a starting point. Suposedly cylindrical pots can be made to be adjustable in lenght with ease.
It has the benefit to be adjusted after building the whole box, so You can set Your desired tuning freqvency.
vent tuning
while this article has its own flaws, it does verifys (correctly) that calulcations and real life are 2 different things.
Usualy the simulation/calculation toosl just give a nice starting point.
Goal is to get the largest possible crossectional area You can fit into the box, get a more or less close tuning freqvency, then mesure What You done and adjust Your port till You get what You where looking for.
The process of mesuring the tuning feqvency is not hard. a simple multimeter can do the job.
As tuning freqvency will have an impedance peak.
Port placement has its own effects too, specialy for the non-cylindrical ports.
They can act as if they where a LOT longer than they are actualy.
That is realised as a lower tuning freqvency then expected.
Good news is, they can be cut down to size with ease, and that is what You need to do in order to get a higher tuning freqvency.
My absolute not scientific approach is simply using the maximal crossectional area regardles if its cylindircal, or not.
Allso, in my calculations value of k = end correction (normally 0.732) is just 0.7
I done that by experience. MAny times I got it closer with 0.7 end correction to real life, many times close enough to simply not worth the effort to trimm it a bit shorter.
-> notice, the k value i use is not at all verifyd by anyone, not even me. it is just my personal practice.
I think the first formula has an error in that it doesn't correct for the end correction properly - should read:
Lv = (23500*Dv^2*Nv/(Fb^2*Vb))-(k*Dv*sqrt(Nv))
That would make the end correction subject to the number of vents being used, rather than just the vent's diameter. I remember reviewing this formula some time ago (years, LOL), and having an end-correction that was independent of the number of vents in use was judged to be more "accurate".
vent tuning
while this article has its own flaws, it does verifys (correctly) that calulcations and real life are 2 different things.
I suspect that the formula breaks down as vent volume approaches box volume. But you're correct - the calculated lengths should be considered a starting point, with some trimming likely required to get the target Fb.
I suspect that the formula breaks down as vent volume approaches box volume. But you're correct - the calculated lengths should be considered a starting point, with some trimming likely required to get the target Fb.
Further to this, I tried comparing the results of my vent length equation against the predictions of another program that's used a lot here for speaker design - HornResp. I simmed a 80 litre volume that's being tuned to various frequencies with a 140cm^2 vent.
This first table shows the predicted lengths using my vent calculation:
20 Hz - 121.5 cm
30 Hz - 48.6 cm
40 Hz - 23.4 cm
50 Hz - 11.2 cm
60 Hz - 4.8 cm
70 Hz - 0.9 cm
This second table shows the lengths predicted by HornResp
20 Hz - 118.0 cm
30 Hz - 51.6 cm
40 Hz - 27.0 cm
50 Hz - 15.0 cm
60 Hz - 8.8 cm
70 Hz - 5.2 cm
It looks like HornResp is predicting longer vents are required to achieve the same Fb (except for 20 Hz). The difference between the lengths seems to vary from 4.3 cm down to 3.0 cm @ 30 Hz, suggesting that the end-correction factor that HornResp is not only slightly different, but also somewhat frequency-dependent.
Curiously enough, if my equation is predicting vent lengths that are longer than required (the linked site in a previous message suggests just under 20% too long), that means that the vent lengths predicted by HornResp might even more inaccurate...
That would make the end correction subject to the number of vents being used, rather than just the vent's diameter. I remember reviewing this formula some time ago (years, LOL), and having an end-correction that was independent of the number of vents in use was judged to be more "accurate".
Hi Brian,
The theory is that the shape of the vent doesn't matter (or that it is multiple) only the areas, so the correction I posted is more "mathematically correct" than yours.
I seem to remember an old argument on the bass list where this was discussed and the person who posted wrote me later that upon testing he found I was right - in THAT case anyway 😉
In real life, vents are not the ideal creatures envisioned in theory, and in practice the environment near the port makes a difference. Most empirical studies I have seen show lower tuning frequencies than predicted. This makes the formula conservative, in that you can always cut the port shorter, but it is harder to add material....
Note: Troels Gravesen has some port investigations on a site somewhere where he gives results from empirical study. [edit - Ah, I see it is linked above]
Regards,
Ron
Last edited:
Hi Brian,
The theory is that the shape of the vent doesn't matter (or that it is multiple) only the areas, so the correction I posted is more "mathematically correct" than yours.
That was actually the crux of the argument - that the calculated length referred to the length of each vent, not the length of a "summed" vent that consisted of N vents of the same area, and it was therefore incorrect to apply the end correction in the manner your equation suggested.
If I remember the discussion correctly (it WAS a long time ago), it concerned an analysis of JL Audio's suggested approach for vent calculations - see JL Audio - Car Audio Systems. My equation gives results that are in close agreement with JL's for multiple vents.
In any case, the results of the calculations seems to be quite conservative, to the tune of 15~20%, and the vents will likely need to be trimmed a bit to achieve target Fb.
In any case, the results of the calculations seems to be quite conservative, to the tune of 15~20%, and the vents will likely need to be trimmed a bit to achieve target Fb.
The end correction is for the area, though, and not the diameter of a single vent. So regardless of JL's info I would stand by my correction.
Troels results for undamped boxes give approx 19000 for the first constant and 0.57 for the end correction constant if fitted to the same equation. Might be interesting to measure a vented box and see.
--
Ron
Troels results for undamped boxes give approx 19000 for the first constant and 0.57 for the end correction constant if fitted to the same equation. Might be interesting to measure a vented box and see.
Some quick measurements with a vented speaker I have on hand suggest that even that might be conservative, e.g.
Box size = 5.1 litres
Vent = 4.5cm diameter, 9.5 cm long
Measured Fb = 67.8 Hz
My equation:
Calculated L (67.8 Hz) = 16.7 cm
Troels' adjustment
Calculated L (67.8 Hz) = 13.5 cm
The box does have a little bit of damping in it, which might be skewing Fb down a bit.
just another question , that seems that all of you have much much more knowledge than me, i'm a poor newbie 🙂 🙂
Tonight i calculated the dimension,Lv,Sv,etc.... for my reflex box. but i have a doubt.
I'll make the ports a bit longer, just in case, so maybe i can trim them to achieve the desired Fb
Wich method can i use to check the tunne of the Fb? Is there a post? any web that explains the process for dummies? 🙂)
Thanks again, really apreciate all your help 🙂
Tonight i calculated the dimension,Lv,Sv,etc.... for my reflex box. but i have a doubt.
I'll make the ports a bit longer, just in case, so maybe i can trim them to achieve the desired Fb
Wich method can i use to check the tunne of the Fb? Is there a post? any web that explains the process for dummies? 🙂)
Thanks again, really apreciate all your help 🙂
you hook your sub up to your amplifier.
You download winisd, and use its freqvency generator, or any other freqvency generator you like.
You mesure the speaker impedance vs freqvency, and you will see a nice impedance peak at tuning freqvency. If its too low, You trimm the port a bit and .. mesure again.
And again, and again until You are happy.
not too accurate in terms of absolute impedance, but will reveal the peaks anyways, and the corresponding freqvency if You use 2 multimeters to mesure voltage and current for every feqvency step. Voltage / current = impedance (at a given freqvency)
Choose a low volume, something around few volts is more than sufficient to take the readings.
You can use only 1 ultimeter, but then you need to mesure 2 times.
1 for voltage, 1 for freqvency.
There are other methoods, but thisone is easy to understand and carry out.
The impedance graph You get will be inaccurate in terms of absolute values, but the shape of the graph and the freqvency of impedance peaks will be well whitin tolerance.
For Brian Steele :
Yes, the ratio of the air in the port and the air in the box does alter the end correction factor.
So do flared ports, ports that are not straight, and so on.
The end correction value is -at least in my experience- allso depends on the ratio of the box dimensions. Sourrounding of the port is allso having an effect, it will change the tuning freqvency a bit. Allso, the friction between the materia of the port and the air has its own effect.
I could list You like 20 more small effects that add up.
One by one none of them will alter tuning more than a fraction of a hz.
But they do add up. Even the lineing of damping material on the walls of the box will change things a bit.
Hence i told, calculations are just a starting point.
I use only a handfull of drivers, i know them fairly well. Hence i can estimate for my usual box designs a correction value that is closer to realy than the general formula.
If You ask me, best is to use the simulation and pick the largest port that can fit the box. And the port should be one of those that can be adjusted. Then You can play around witht he lenght of the port, till You find what You are looking for.
You download winisd, and use its freqvency generator, or any other freqvency generator you like.
You mesure the speaker impedance vs freqvency, and you will see a nice impedance peak at tuning freqvency. If its too low, You trimm the port a bit and .. mesure again.
And again, and again until You are happy.
not too accurate in terms of absolute impedance, but will reveal the peaks anyways, and the corresponding freqvency if You use 2 multimeters to mesure voltage and current for every feqvency step. Voltage / current = impedance (at a given freqvency)
Choose a low volume, something around few volts is more than sufficient to take the readings.
You can use only 1 ultimeter, but then you need to mesure 2 times.
1 for voltage, 1 for freqvency.
There are other methoods, but thisone is easy to understand and carry out.
The impedance graph You get will be inaccurate in terms of absolute values, but the shape of the graph and the freqvency of impedance peaks will be well whitin tolerance.
For Brian Steele :
Yes, the ratio of the air in the port and the air in the box does alter the end correction factor.
So do flared ports, ports that are not straight, and so on.
The end correction value is -at least in my experience- allso depends on the ratio of the box dimensions. Sourrounding of the port is allso having an effect, it will change the tuning freqvency a bit. Allso, the friction between the materia of the port and the air has its own effect.
I could list You like 20 more small effects that add up.
One by one none of them will alter tuning more than a fraction of a hz.
But they do add up. Even the lineing of damping material on the walls of the box will change things a bit.
Hence i told, calculations are just a starting point.
I use only a handfull of drivers, i know them fairly well. Hence i can estimate for my usual box designs a correction value that is closer to realy than the general formula.
If You ask me, best is to use the simulation and pick the largest port that can fit the box. And the port should be one of those that can be adjusted. Then You can play around witht he lenght of the port, till You find what You are looking for.
Some quick measurements with a vented speaker I have on hand suggest that even that might be conservative, e.g.
Box size = 5.1 litres
Vent = 4.5cm diameter, 9.5 cm long
Measured Fb = 67.8 Hz
My equation:
Calculated L (67.8 Hz) = 16.7 cm
Troels' adjustment
Calculated L (67.8 Hz) = 13.5 cm
The box does have a little bit of damping in it, which might be skewing Fb down a bit.
Note that both damping and inductance could make the minimum impedance frequency shift without actually affecting the tuning frequency. For measuring Fb, the minimum in diaphragm SPL might be a more accurate measure in that case. The particulars of damping material placement might also actually add effective mass to the port, so things are not as simple as they seem 😉
it can happen that it would be less work to list what CAN'T change the tuning freqvency.
LOL - true.
On a somewhat related issue, HornResp seems to give two different results, depending on how you model the vented box. One gives results identical to those predicted by my equations (I'm going to guess because the same equation is likely used in HornResp's calculations), and the other gives vent lengths that are even longer than those predicted by my equations, if you model for 2*PI space. It's only if you shift the model down to 1*PI or 0.5*PI do the results come into closer alignment. Quite curious, as I think most box-modelling programs assume 2*PI space. Now I know from my own personal experience that HornResp's predictions re Fc tend to be pretty good, but that's when designing an actual "horn", with a large expanding flare. Perhaps the equations governing the behaviour of the horn flare lose accuracy as the flare size approaches a simple vent.
Hmm... perhaps it's time to take advantage of our "Internet connectiveness" and use actual measured results to derive a equation that better describes the relationship between Vb, Fb, Dv and Lv. Basically ask persons to submit their own measurements and results and use those to create the "best-fit" curve. What do you think? I'm thinking if we do this, we'll need to set some "benchmark requirements" for the data collection, i.e.
1. Vb>> vent volume (e.g. vent volume must be 10% or less of Vb)
2. Vent must be located at least one vent diameter (and preferably more) away from any walls or other obstructions.
3. Vb must be unlined and unstuffed
4. Measurement should be taken at 2.83V
5. Vents should not be noticeably flared
Hmm... perhaps it's time to take advantage of our "Internet connectiveness" and use actual measured results to derive a equation that better describes the relationship between Vb, Fb, Dv and Lv. Basically ask persons to submit their own measurements and results and use those to create the "best-fit" curve. What do you think? I'm thinking if we do this, we'll need to set some "benchmark requirements" for the data collection, i.e.
1. Vb>> vent volume (e.g. vent volume must be 10% or less of Vb)
2. Vent must be located at least one vent diameter (and preferably more) away from any walls or other obstructions.
3. Vb must be unlined and unstuffed
4. Measurement should be taken at 2.83V
5. Vents should not be noticeably flared
Here's a "better" formula, based on the ideal gas law:
Lv=(gamma*Pb/(rho*16*pi))*Dv^2/(Fb^2*Vb)-0.85*Dv
gamma ~= 1.0 to 1.4
Pb ~= 101325
rho ~= 1.2
pi=3.1415926535...
If you believe the whole adiabatic to isothermal thing, you could say gamma=1.4 for unstuffed boxes, and somewhere around 1.2 or so for stuffed boxes. rho could possibly be altered by stuffing. Pb is barometric pressure, which perhaps varies by +5/-10% or so. IMO, at typical vent frequencies all ports are effectively flanged at both ends.
Clear as mud, right? 😉 Have fun, try it out, discuss! You saw it here first, folks!
Regards,
Ron
well..
if you want to experiment thats okay.
but results will be quite disapointing if many many parameters change.
I would suggest if You realy want to get to the bottom of this.. is to grab a driver,
and make a demo box for your experiments.
The box should be able to accept a BIG port along with the driver.
Your goal is not to get ideal response, but to check tuning freqvency.
Then start to tune it to the same freqvency with different port crossectional area.
Suposedly the port -if a pipe is used- should be 1 diameter away from edges, and the driver.
The box should be radiating into 2pi space, or if you like you can do dual test by moving it to a 1pi space after You finished the mesurement step at 2pi.
At least you will be able to find the relation of port contained airmass vs box airmass and correction value.
And so on.. I would bet the relation is not linear, but anyways if you are that intrested You can give it a go.
And one by one You could change parameters, but it is surely going to be a LONG way till You get anywhere. Be prepared to conduct mesurements in the order of 100-s.
Someone could team up with you, but it would alter results. Simply impossible they hve the exact conditions you have.
if you want to experiment thats okay.
but results will be quite disapointing if many many parameters change.
I would suggest if You realy want to get to the bottom of this.. is to grab a driver,
and make a demo box for your experiments.
The box should be able to accept a BIG port along with the driver.
Your goal is not to get ideal response, but to check tuning freqvency.
Then start to tune it to the same freqvency with different port crossectional area.
Suposedly the port -if a pipe is used- should be 1 diameter away from edges, and the driver.
The box should be radiating into 2pi space, or if you like you can do dual test by moving it to a 1pi space after You finished the mesurement step at 2pi.
At least you will be able to find the relation of port contained airmass vs box airmass and correction value.
And so on.. I would bet the relation is not linear, but anyways if you are that intrested You can give it a go.
And one by one You could change parameters, but it is surely going to be a LONG way till You get anywhere. Be prepared to conduct mesurements in the order of 100-s.
Someone could team up with you, but it would alter results. Simply impossible they hve the exact conditions you have.
Here's a "better" formula, based on the ideal gas law:
Lv=(gamma*Pb/(rho*16*pi))*Dv^2/(Fb^2*Vb)-0.85*Dv
gamma ~= 1.0 to 1.4
Pb ~= 101325
rho ~= 1.2
pi=3.1415926535...
If you believe the whole adiabatic to isothermal thing, you could say gamma=1.4 for unstuffed boxes, and somewhere around 1.2 or so for stuffed boxes. rho could possibly be altered by stuffing. Pb is barometric pressure, which perhaps varies by +5/-10% or so. IMO, at typical vent frequencies all ports are effectively flanged at both ends.
Clear as mud, right? 😉 Have fun, try it out, discuss! You saw it here first, folks!
Regards,
Ron
I've found the formula above gives near identical results to the formula given on my website if you use Pb=1013250 and substitute k=0.732. Possibly a dimension thing, as I used vent dimensions in cm in the calculations. And we already know that my formula is a bit, um.. generous 🙂.
well, anyways regardless of the mathematical effort even if You use a server cluster dedicated for the task, and the most complicated formulas, you are still not getting results of real life.
So realy no need to fancy things out anymore 😀
-> simulate
->build
/start of loop, last untill You = happy
->mesure
->adjust
/end of loop
the simple formulas give results quite close enough to serve as a starting point.
One "could" get absolute proper results via simulation with simulating infinate elements of variables.
By the time one would gather the required data to start with, a clever guy will do a set of mesurements and adjust tuning properly. (takes like less than a half hour if You have some experience)
I must ask, why You think its worth digging so deep?
no problem with that, but i just can't seem to figure out where is this going to lead.
So realy no need to fancy things out anymore 😀
-> simulate
->build
/start of loop, last untill You = happy
->mesure
->adjust
/end of loop
the simple formulas give results quite close enough to serve as a starting point.
One "could" get absolute proper results via simulation with simulating infinate elements of variables.
By the time one would gather the required data to start with, a clever guy will do a set of mesurements and adjust tuning properly. (takes like less than a half hour if You have some experience)
I must ask, why You think its worth digging so deep?
no problem with that, but i just can't seem to figure out where is this going to lead.
I must ask, why You think its worth digging so deep?
I think a calculated result for vent length that's almost 20% longer than measurements indicate is actually required can be improved upon, that's all.
- Status
- Not open for further replies.
- Home
- Loudspeakers
- Subwoofers
- Design of rectangular ports for Bass reflex box