As mentioned previously, this is my latest speaker build. A pair of full range with 4” drivers, the timber is Tasmanian Oak planks 14mm thick with 6mm MDF adhered to the inner surface, all surfaces glue fixed with Titebond wood glue. I’ve applied a stain to them this morning, clear coats still to come.
Attachments
-
59ACF2AB-9BE1-495E-831E-89B4528219FF.jpeg398 KB · Views: 216
-
8921B0A7-3246-4C0D-A798-CAED58819A71.jpeg458.1 KB · Views: 174
-
073C3BC4-54CF-475B-8B59-9B613F1294C0.jpeg371.1 KB · Views: 264
-
17860A8A-0C93-4094-9E35-4A765AE0701A.jpeg483.6 KB · Views: 194
-
BAD8DE83-6934-422C-B5E4-471D3E293DBD.jpeg449.8 KB · Views: 186
i've used to build enclosure using plywood back in the 5 years past ... then when MDF board became easily accessible i start to switch over to them ... MDF board is relatively easy to work with if you have the right tools but get to be prepared to battle with saw dust going all over the place ... for midrange enclousre plywood is ok but for stuff like subwoofers definitely look into MDF boards since to me they were more solid ... the plywood i had locally tend to splinter after few years
Get a stronger grade of plywood, Boiling Water Proof, or Marine grade.
We used to import a lot of wood and wood products from Malaysia to India.
And do bind the edges with strips, to protect them.
I have seen board with ply on the faces, and particle board inside, those are not so good.
We used to import a lot of wood and wood products from Malaysia to India.
And do bind the edges with strips, to protect them.
I have seen board with ply on the faces, and particle board inside, those are not so good.
Birch plywood from the Baltic states is good strong consistent plywood. They say its acoustic values are tried and true.
It hits the pocket book harder although its nicer to work with.
I paid $40.00 CAD for a 4x4'x 3/4" piece of "North American" stuff just last week. It has fewer plies. And it doesn't take dark stains well. But it is decent ply to use I suppose.
European plywood must be higher in cost these days that it ever has.
I found a stack of the genuine stuff on k***I this morning. He wants 40 bucks per 5x5 sheet. But its only 3 mm thickness. I would of jumped on a few if it was 16 mil.
It hits the pocket book harder although its nicer to work with.
I paid $40.00 CAD for a 4x4'x 3/4" piece of "North American" stuff just last week. It has fewer plies. And it doesn't take dark stains well. But it is decent ply to use I suppose.
European plywood must be higher in cost these days that it ever has.
I found a stack of the genuine stuff on k***I this morning. He wants 40 bucks per 5x5 sheet. But its only 3 mm thickness. I would of jumped on a few if it was 16 mil.
As mentioned previously, this is my latest speaker build. A pair of full range with 4” drivers, the timber is Tasmanian Oak planks 14mm thick with 6mm MDF adhered to the inner surface, all surfaces glue fixed with Titebond wood glue. I’ve applied a stain to them this morning, clear coats still to come.
How is the cab finishing coming along?
Staining solid oak brings great satisfaction.
Anyone who has had to design, build, and deliver premium things made from sheet goods will likely not prefer plywood due to the inconsistency in the material. There are higher priced exceptions, but usually will bite you. Voids, delaminations, warping…
I don’t know how a speaker would be immune to any of those things.
I don’t know how a speaker would be immune to any of those things.
There is nothing premium at all about mdf...high quality plywood is readily available with no voids or delamination and I have never had warpage problems with it. It will cost you more than the big box junk, but if you endeavor to create a premium end product you should expect to pay for premium material....premium things made from sheet goods...
Yes.if you endeavor to create a premium end product you should expect to pay for premium material.
dave
For my last two projects I used laminated white oak boards - as an experiment. The boards were 1" thick, 11.5" wide and available in various lengths. They are sold as "stair treads" here in the USA by the home improvement stores. I was happy with the results. The cabinets are rigid and sound good but also very heavy at 45 lbs empty. After a very dry winter I have some minor cracking to deal with, but that probably could have been avoided with a varnish finish instead of the Danish oil that I used.
Attachments
The first coat was applied this morning, now it’s drying - sanding - re-coating - drying - sanding etc etc…. Probably another two to three coats.How is the cab finishing coming along?
Staining solid oak brings great satisfaction.
I confess I didn't read the whole thread, but the opening few posts, at least upon cursory reading, seemed to be missing the main reason MDF is a great building material for cabinets. It is inherently non-resonant. Knuckle-tap a piece of plywood, then do the same with MDF. There's a reason you can build a string bass out of plywood and it'll do a decent job of resonating the strings. The last thing you want in a speaker box is material that will add any color to the sound or resonate in any fashion. Yes, you can brace it to make it more rigid, and damp it to reduce coloration, but why start out with something that requires more correction?
I built my cabinets out of 3/4" MDF, braced internally with additional MDF pieces dependent upon cabinet size, then typically finish them with another layer of 1/4" or 1/2" baltic birch, oak, or cherry plywood for added mass and for appearance. I find MDF an ideal cabinet material.
I built my cabinets out of 3/4" MDF, braced internally with additional MDF pieces dependent upon cabinet size, then typically finish them with another layer of 1/4" or 1/2" baltic birch, oak, or cherry plywood for added mass and for appearance. I find MDF an ideal cabinet material.
Everything is resonant MDF included.the main reason MDF is a great building material for cabinets. It is inherently non-resonant.
Is most often not well interpreted. The dead thud you get with MDF is lower frequency broader Q. The “sharper” sound from the plywood enclosure is higher frequency, higher Q. The latter is much harder to excite (with music), the MDF can be excited much easier and if so, more easily heard.Knuckle-tap
Your argument supports a (quality) plywood. Even MDF plywood is better than MDF.
dave
I understand one of your points, and I should have said "inherently LESS resonant" rather than "nonresonant." Everything has SOME resonance, as you stated. Thanks for the correction. I'm not familiar with MDF plywood. If it's a sandwich of MDF and spruce or other plys of natural wood, that may be the best of both worlds... sandwiches of differing densities are desirable. I take exception to the notion that MDF can be "excited much easier" by music. Not to be argumentative, but do you have any data to back up that claim? I know of no instance where MDF is favored over plywood when resonance or reinforcing acoustic energy is desirable... none. There's a reason why MDF has been, and continues to be, the material of choice among the vast majority of speaker building enthusiasts.Everything is resonant MDF included.
Is most often not well interpreted. The dead thud you get with MDF is lower frequency broader Q. The “sharper” sound from the plywood enclosure is higher frequency, higher Q. The latter is much harder to excite (with music), the MDF can be excited much easier and if so, more easily heard.
Your argument supports a (quality) plywood. Even MDF plywood is better than MDF.
dave
yes agree ... and the resonant can be reduced significantly by adding damping material such as sound proof sheets and polyfiber (and maybe few smaller pillows) they work really well ... shown below is my subwoofer project for a 6' cheap driver ... damping material and polyfiber all over the place and some soundproof around and on the driver magnet made the whole box almost resonant free (the MDF itself only 9mm thickness) ... during testing on the raw stage( no bracing no damping no treatment) even using MDF it resonates badly) .... i ended up using MDF for almost all my projects due to nothing better than thisEverything is resonant MDF included.
Attachments
-
240173308_3118621838351169_5733091225745195607_n.jpg46.8 KB · Views: 111
-
240515470_3118621731684513_5536785413782339552_n.jpg41.1 KB · Views: 106
-
241370130_3118621668351186_5810742749097143408_n.jpg71.5 KB · Views: 108
-
241372446_3118621781684508_5138082719297830170_n.jpg35.8 KB · Views: 106
-
242770107_3118621701684516_8277467279800767183_n.jpg55.6 KB · Views: 115
Still not the case. A metal enclosure that only rings at very high frequency would likely much more resonant and MDF (if excited by the right frequency), but the metal box would be a better speaker box.I should have said "inherently LESS resonant" rather than "nonresonant."
We should only really be interested in materials that do not resonate because the music will not excite their inherent resonant structures.
Note that we are talking about box wall resonance, not air space damping, the primary purpose of which is to quell internal resonances in the trapped airspace inside the box. It does reduce, by a small amount, the hf energy that gets into the box walls, so a HF/HiQ box will get an even greater edge.
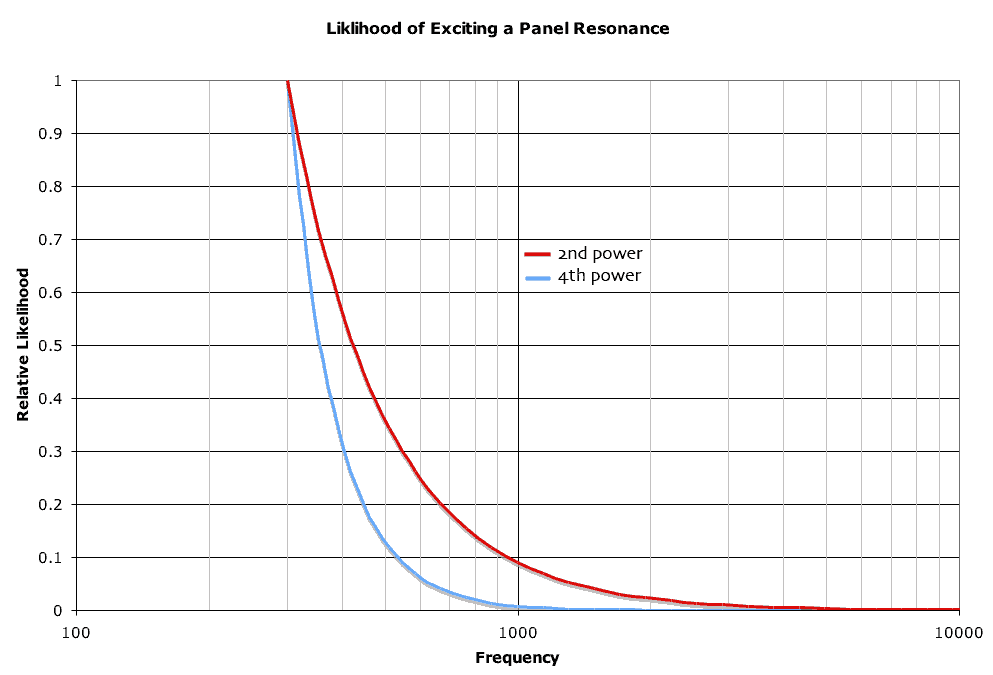
dave
Last edited:
Wow. OK, I'm new here, and you're an administrator, but one of us is REALLY confused. If it's me, please set me straight and provide some data to confirm you're assertions. I'm always more than willing to admit that I'm wrong... but what you're saying goes against a lifetime of experience both as a musician and an amateur speaker builder.Still not the case. A metal enclosure that only rings at very high frequency would likely much more resonant and MDF (if excited by the right frequency), but the metal box would be a better speaker box.
We should only really be interested in materials that do not resonate because the music will not excite their inherent resonant structures.
dave
Metal?!? Musical instruments are made out of either metal (brass most commonly, followed by nickel, copper, and silver in no particular order), solid woods (spruce, maple, rosewood, and mahogany are typical, depending upon instrument and part function), or plywood in less expensive celli, bass, and some guitars/ukes/etc. The WHOLE point of using those materials is to amplify the sounds produced by the player, whether it be by causing a string to vibrate, then passing those vibrations to a resonating chamber built with the aforementioned materials, or by buzzing one's lips, vibrating a reed, or splitting a column of air (flute/recorder), and then amplifying THAT vibration with a metal conical or cylindrical chamber or bell. Over-simplistic, but that's the idea. There's a reason those materials are chosen; they are good at amplifying resonances, Luthiers go out of their way searching like crazy for perfect "tonewoods," brass instrument manufacturers experiment with different alloys, thicknesses, bores... all because the material influences and enhances the sound.
Now, speaker cabinets. Other than creating the correct box size and damping characteristics for a specific driver's parameters, desired low frequency slope, and designing around or using the diffraction step inherent in the front baffle, the whole POINT of constructing a speaker cabinet is so that the materials do NOT add to the sound in any way. It is, of course, possible to counteract or at least minimize or reduce inherent problems with pretty much any chosen building material, but to say that metal is a better material for building a cabinet than MDF is just... well.... I have no words. I'll defer to the real experts, like Vance Dickason. In addition to MDF, Sonotube is another excellent material; rigid, made up of many layers of paper, and also very minimal resonance.
I'm all ears (OK, eyes) if you can link to any reputable sources that confirm that metal and plywood are better construction materials for cabinets for acoustic reasons. Yes, there's lots of sites that tout the ease of working with plywood compared to MDF, the extra strength for portability, the weight savings, ease of finishing, etc. If, however, we're discussing which material is better acoustically, there really isn't much to discuss. I wouldn't want to carry my speakers anywhere; between 3/4" MDF all around, 1.5" MDF baffle (two 3/4" layers), and then 1/2" Russian birch on top, even my small surround speakers weigh a LOT, and the subwoofers are almost impossible for one person to move. My goal wasn't portable speakers, it was inert cabinets that let the drivers do what they need to do without any additional coloring contributions from the cabinet.
So... yes, you can build speakers out of anything. Yes, plywood is easier to work with. No, it is not less resonant than MDF. If I'm wrong, I'll admit it, but I want to see data.
The important part to think about is, what in the music can excite the potential resonance(s) in your enclosure, and how can you exploit that to build an enclosure that effectively, does not ring. A knuckle rap (or a hit with a hammer) do not represent music. Forget about what the marketing dept has made “common knowledge” and think about the problem.
Looking at musical horns, they are designed to have highQ air resonances, notes. Part of learning to play these is the ability to generate the correct exciting frequencies. The metal may add some of its own character, but it is primarily the air that resonates to make the noise.
So not at all analogous.
For instance, it is easy to see why (quality) plywood makes for better subwoofer boxes. A sub has a very limited hf bandwidth. So if we can make all panels resonate at frequencies higher than the bandwidth they will never be excited. This is much easier with 15mm BB than 3/4” MDF. Using push—push can yield a woofer that has to be significanty abused to get the box walls moving.
I have built a proof of concept sub where the enclosure can be picked up with a couple of fingers in the driver hole, add the drivers it becomes a serious lift. Massive sub is only an asset if the box starts moving from the reaction force (push-push takes advantage of active reaction force cancelation). This represents an elegant, efficient, diametrically opposed to the brute force you applied to your sub.
It is much harder to do with a FR speaker. But i have gotten pretty good. Stiff, light helps (if no sacrifice in stiffness) can be used to engineer an enclosure that does not resote when playing music. After that you need to work on the shape to reduce the enclosure diffraction signature.
A loudspeaker with an enclosure that gets out of the way is a huge help at improving DDR and being able to reproduce the subtle bits of inormation that lend life to a voice or an instrument sand do not bury the tiny buits that are require to reproduce a solid 3D soundstage/image.
Solid wood is tricky to deal with but can make nice enclosures.
Bote the Oak enclosures above, we built the same loudspeaker out of garry oak and out of western red cedar. One oak box weighed more than the pair of cedar ones. The cedar ones worked better (but are easily dented).
Don’t have a pic of our Oal ones, here is someone elses/similar,
I started with K3/partical board, then HDF, then thin HDF with laminate on both sides. Then BB. Then better plywood yet, and if you can afford it, stranded/fossolozed bamboo plywood. Even better plywoods can be envisioned with existing material and a vacuum bag. Actully i started with vintage (then new) mandiran orange boxes when i was 12. Double walled, leaky boxes.
MDF's only real asset is that it is cheap. Cheap to buy, cheap to work, cheap tpo finish. Not cheap to ship.
There is a lot more that can be said.
dave
Looking at musical horns, they are designed to have highQ air resonances, notes. Part of learning to play these is the ability to generate the correct exciting frequencies. The metal may add some of its own character, but it is primarily the air that resonates to make the noise.
So not at all analogous.
For instance, it is easy to see why (quality) plywood makes for better subwoofer boxes. A sub has a very limited hf bandwidth. So if we can make all panels resonate at frequencies higher than the bandwidth they will never be excited. This is much easier with 15mm BB than 3/4” MDF. Using push—push can yield a woofer that has to be significanty abused to get the box walls moving.
I have built a proof of concept sub where the enclosure can be picked up with a couple of fingers in the driver hole, add the drivers it becomes a serious lift. Massive sub is only an asset if the box starts moving from the reaction force (push-push takes advantage of active reaction force cancelation). This represents an elegant, efficient, diametrically opposed to the brute force you applied to your sub.
It is much harder to do with a FR speaker. But i have gotten pretty good. Stiff, light helps (if no sacrifice in stiffness) can be used to engineer an enclosure that does not resote when playing music. After that you need to work on the shape to reduce the enclosure diffraction signature.
A loudspeaker with an enclosure that gets out of the way is a huge help at improving DDR and being able to reproduce the subtle bits of inormation that lend life to a voice or an instrument sand do not bury the tiny buits that are require to reproduce a solid 3D soundstage/image.
Solid wood is tricky to deal with but can make nice enclosures.
Bote the Oak enclosures above, we built the same loudspeaker out of garry oak and out of western red cedar. One oak box weighed more than the pair of cedar ones. The cedar ones worked better (but are easily dented).
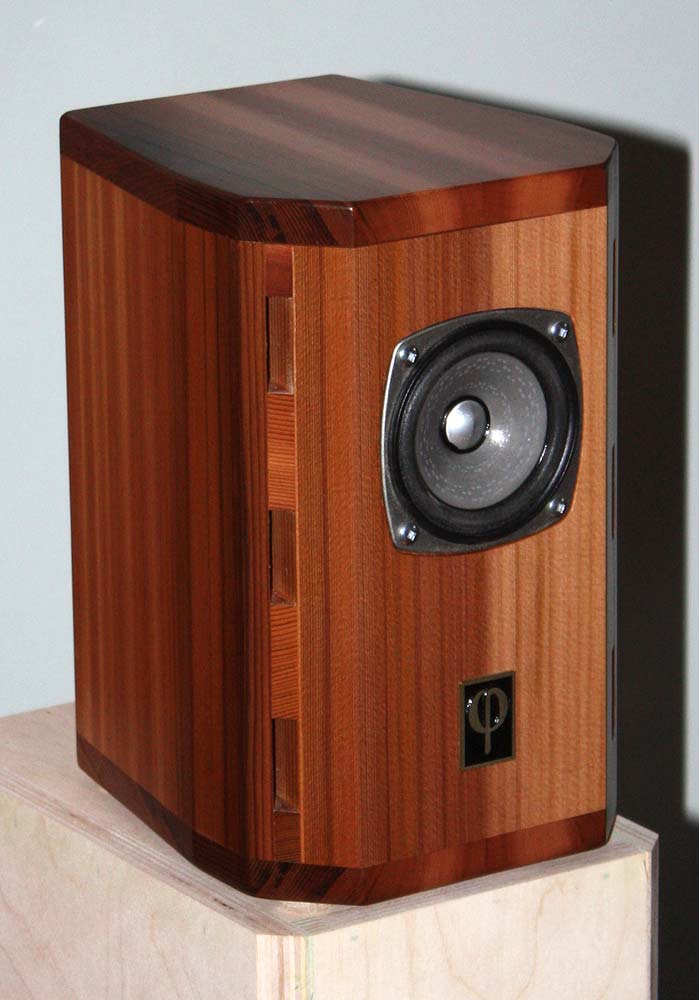
Don’t have a pic of our Oal ones, here is someone elses/similar,
I started with K3/partical board, then HDF, then thin HDF with laminate on both sides. Then BB. Then better plywood yet, and if you can afford it, stranded/fossolozed bamboo plywood. Even better plywoods can be envisioned with existing material and a vacuum bag. Actully i started with vintage (then new) mandiran orange boxes when i was 12. Double walled, leaky boxes.
MDF's only real asset is that it is cheap. Cheap to buy, cheap to work, cheap tpo finish. Not cheap to ship.
There is a lot more that can be said.
dave
Last edited:
But never guaranteed to have consistent laminations, sorry but you are misinformed.There is nothing premium at all about mdf...high quality plywood is readily available with no voids or delamination and I have never had warpage problems with it. It will cost you more than the big box junk, but if you endeavor to create a premium end product you should expect to pay for premium material.
Probably not going to matter much either way with 4” drivers though.
Think about the process, or maybe even spend ten + years building high end structures with all kinds of materials, then get back and reply, I’ll be more willing to listen then.
Sonny when you grow up a bit we can have an adult chat about the technical aspects of plywood vs mdf as it applies to speaker cabinet construction...I had 10 years in at this hobby 30 or so years ago.Think about the process, or maybe even spend ten + years building high end structures with all kinds of materials, then get back and reply, I’ll be more willing to listen then.
I am sure many have little clue of what i speak. My dad was a bit of a hoarder. Going thru the dregs of his stuff i found this, likely some 55 years old.… mandiran orange boxes ...
dave
- Home
- Design & Build
- Construction Tips
- Plywood VS MDF for speaker construction