It's interesting that you say "scream loudly". Having a few speakers with Polykevlar cones, (5" to 10") I've never noticed this (compared to my paper cone drivers which certainly do have a breakup around 3k - 4K). The published graphs (if they are to be believed) do not infer this either). You do realise that Polykevlar cones are actually a composite three layer PC-Foam-PC, they seem far stronger than some thin single layer cones, and I thought resist breakup reasonably well.Kevlar scream loudly in the midband. Every cone has a particular problem area. But Kevlar the problem area is right in the required passband of the driver. Attempts at reducing that ringing make for a heavy cone. To add to the fun and games many "Kevlar" cones are actually fiberglass. Same goes for carbon fiber cones. Actually visiting your vendors is an education all to itself.
Nonsense by KA. Of course, there is a possibility some DIYer might actually design a bad sounding polykevlar based system. I should know for I have repaired one like that.It's interesting that you say "scream loudly".
edit: of 6 pages from Interview, this is only one slightly touching our topic.
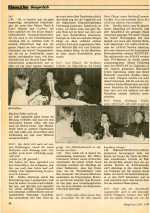
Last edited:
I don't find that a great example, since the thing basically has no surround.Actually that is dependent on design, and execution of the driver itself mostly, not Kevlar. The data added below from the B&W LF00264 done by Zaph audio.
Also take note of the sensitivity compared to most 'hifi' midranges.
Yes there is a breakup and slight resonance at 3,5k, that deserves a gentle notch.
To me that is already out of the midrange.
Overall though it is cleaner then 99% of the "competition" even with that artefact, all the way to 10 k.
And that is with a 6 grams cone on a 6".
A 4" cone wil have that breakup Even higher in frequency.
The need for the heavy and damped cone is not really existing ?
Most people would be crossing that driver to match the directivity of a tweeter 2-2,5k. And not stretch it to 3,5k with a low order xo ala B&W.
And the sensitivity opens up for some interesting driver combinations in some cases.
Which changes cone resonances and break-up modes drastically.
A mid-woofer asks for a very different set of compromises.
I haven't seen any more modern drivers lately, because the old ones were far from being optimized.
Often resulting in other just high overall distortion and/or a distortion peak right around 1-2kHz.
Wavecor has introduced some hybrid kevlar/carbon ones;
https://audioxpress.com/article/voice-coil-test-bench-wavecor-s-wf182bd13-04-7-midbass-driver
https://audioxpress.com/article/test-bench-the-new-6-wf152bd09-04-midbass-driver-from-wavecor
On Zaph Audio's website there a couple of oldies to been seen.
Usher 8836A; Although has an inverted dust cap
Davis 13KLV5MA
But to be perfectly honest, it's impossible to draw much conclusion from these kind of graphs.
Mostly because so much depends on how well a manufacturer spend the time and effort to really optimize things.
Often leading to false conclusions based on wrong anecdotal examples.
Even more so when other things like demodulation rings aren't well implemented.
Although that doesn't change those resonances, it does change the overall frequency response.
Which could lead to a different mechanical choices by the manufacturer.
In the end, it's very much a tricky and complicated tango dance.
Based on my own professional experience, the majority of companies and brands you see, most certainly don't go that far.
I do not know who here designs drivers, or who here even works with drivers everyday. You are all unknown to me. Yes you can find reasonable examples of Kevlar cones. Every cone has it's own flaws. And everyone has their opinion. I tend to work on and design drivers that are purposefully neutral. This is not always the design aim for many companies. A truly neutral loudspeaker exposes the flaws in the vast majority of recordings.
What only none of you has said and it tells me something important in it's omission, is that you cannot see cone resonances to any true degree in an SPL graph. At the very least you need SPL, Impedance and phase. Better to have a waterfall or CSD graph and you will begin to understand the true character of the driver. What is even a better test is a true multitone intermodulation graph that uses tones you have already learned are problematic for the driver membrane. Then you will learn what is actually happening. Arez Posted CSD of a driver. And in the midrange around 600 hertz you do have significant energy that is present after the rest of the cone is quite well behaved.
Now as to how far down below the normalized SPL levels you can hear this is also interesting. Quite a few people consider that if the resonance is about 24db below the normal baseline efficiency it should pretty much be inaudible. What we have learned is that it is very frequency dependent. If those nasty resonances are in the range from 1k to 4k our ears most acute range we can hear things that will be irritating.
As for do I design drivers? Yes since 1997. Largest is a 24 inch subwoofer and smallest are some AMT and dome tweeters. I specialize in underhung design although I will engineer whatever is required by a client. Why you have not heard of me? It's called NDA! Behind the scenes I have fixed and saved many driver designs. There are many less companies that design anything than you know. FOCAL is indeed one of the companies that does have in-house design engineers. So does KEF and B&W.
What only none of you has said and it tells me something important in it's omission, is that you cannot see cone resonances to any true degree in an SPL graph. At the very least you need SPL, Impedance and phase. Better to have a waterfall or CSD graph and you will begin to understand the true character of the driver. What is even a better test is a true multitone intermodulation graph that uses tones you have already learned are problematic for the driver membrane. Then you will learn what is actually happening. Arez Posted CSD of a driver. And in the midrange around 600 hertz you do have significant energy that is present after the rest of the cone is quite well behaved.
Now as to how far down below the normalized SPL levels you can hear this is also interesting. Quite a few people consider that if the resonance is about 24db below the normal baseline efficiency it should pretty much be inaudible. What we have learned is that it is very frequency dependent. If those nasty resonances are in the range from 1k to 4k our ears most acute range we can hear things that will be irritating.
As for do I design drivers? Yes since 1997. Largest is a 24 inch subwoofer and smallest are some AMT and dome tweeters. I specialize in underhung design although I will engineer whatever is required by a client. Why you have not heard of me? It's called NDA! Behind the scenes I have fixed and saved many driver designs. There are many less companies that design anything than you know. FOCAL is indeed one of the companies that does have in-house design engineers. So does KEF and B&W.
Last edited:
The late 80's B&W Kevlar made me get up and leave the room. I have sat in front of decent B&W Kevlar that were much more recently manufactured.As for another anecdotal example, I should have some measurements from a B&W matrix woofer somewhere.
That one was surprisingly smooth actually.
Don't remember what the distortion graph was.
HahaThe late 80's B&W Kevlar made me get up and leave the room. I have sat in front of decent B&W Kevlar that were much more recently manufactured.
Yeah it seemed the era that almost every company was going for fancy materials and looks, including the magnesium frames.
By now, quite a few of those are starting to corrode and it looks like the speaker is covered in mold.
I do have to admit that the looks back than hit a bit of a nostalgia nerve with me
Looking at the performance of many of those old speakers, they don't hold up very well unfortunately.
There are a few exceptions.
Some companies seem to be very stuck in that mindset.
Resulting in very expensive drivers that perform mediocre at best.
Obviously that also has to do with quantities, but still.
I guess there is a market for it....
Do not worry Mark: we know what you do...
To my best of knowledge other than Mark Krav., only Lars Risbo and Norwegian member Snicker-ish are true driver designers here at diya. I have done some tinkering on the past, but that was very very crude and ultra basic stuff. That being said, I am still looking for a free copy of FineCone, just for fun.
To my best of knowledge other than Mark Krav., only Lars Risbo and Norwegian member Snicker-ish are true driver designers here at diya. I have done some tinkering on the past, but that was very very crude and ultra basic stuff. That being said, I am still looking for a free copy of FineCone, just for fun.
🤫 before you know people find that bragging and it's deemed as being rude and disrespectful .....Why you have not heard of me? It's called NDA!
I guess it could be looked as at bragging. It is not meant to be bragging. Just laying out the cards on the table for all to see. I don't post very often anymore on many threads on diyaudio. If I type anything it is because I hope I can add something useful.🤫 before you know people find that bragging and it's deemed as being rude and disrespectful .....
I can tell you that there is nothing that actually models cones correctly. You are better off learning what a particular cone shape will do, what a dustcap shape and diameter will do and what a surround profile will do. These are the things that make the greatest differences. Basically a study of how these behave versus frequency response is much more informative.Do not worry Mark: we know what you do...
To my best of knowledge other than Mark Krav., only Lars Risbo and Norwegian member Snicker-ish are true driver designers here at diya. I have done some tinkering on the past, but that was very very crude and ultra basic stuff. That being said, I am still looking for a free copy of FineCone, just for fun.
I have talked with Peter Larson about some of his software suite. And showed him the software we use internally which is a wrapper for FEMM 4.2, Calculix and Z-88. It gets us as accurate calculations as COMSOL or Vector Fields or the other megabuck software packages.
What I can tell you from experience is that no one will ever tell you their cone or surround formulations in order to model them accurately. So what we do is literally compare previous measurements and extrapolate.
When I end up having to fix a driver design what often strikes me as strange is the blind belief in a computer simulation. They are ballpark guesses. Nothing more. You can get flux close, if you know every mass added you can get SPL relatively close. But connecting the math and the calculations to the real world is the part that take comparative analysis and practical experience. That starts by noting cone and dustcap shapes and relating them to frequency responses. There are definite patterns.
I delivered a bit of a presentation at the Loudspeaker Sourcing show in 2018 that explained how to use these programs. Carsten Tinggaard was interested in the programs as they were working on a driver that became the Purifi first offering. They were paying quite a lot to have ideas modeled. Hopefully this saved them a lot of money! R&D is not cheap to do even if you are a small team.
As I said, it will only be to play with for fun, so nothing more than ballpark guesses. I fully agree with your observations.When I end up having to fix a driver design what often strikes me as strange is the blind belief in a computer simulation. They are ballpark guesses.
Additionally, it all seems small signal simulation. When the going gets rough, the sims will fall apart.
The only limitation is 2D modeling. If 3D is absolutely required the is ELMER. Multiphysics. When we put together out software integration Elmer was very buggy. This seems to have gotten better.FEMM is wonderful.
Hi,
MeeToo! I make my own drivers as well.
Just to add some comments:
Yes, Lars, FEMM is great and if used correctly, delivers very realistic results.
And Mark is right with his thoughts on cones, shapes and so on. As I couldn´t afford FINECONE, I had to make R&D on my cones in the more traditional way, and every detail will alter the final driver´s behaviour.
All the best
Mattes
MeeToo! I make my own drivers as well.
Just to add some comments:
Yes, Lars, FEMM is great and if used correctly, delivers very realistic results.
And Mark is right with his thoughts on cones, shapes and so on. As I couldn´t afford FINECONE, I had to make R&D on my cones in the more traditional way, and every detail will alter the final driver´s behaviour.
All the best
Mattes
Attachments
just to fill in the details at Purifi from 2018: We never paid for simulations - that was in Carstens previous setup. We realised we had to solve the Sd modulation problem and needed to simulate geometric nonlinearity. We decided to work with Comsol and we got an extended trial license. This has been our workhorse for simulation of the soft parts ever since. I build a tool in Matlab to manage and run shape optimisation in Comsol. However, all of the is is not worth much unless it be has good material models. We built up our own testing methodology to derive material models - especially for paper, rubber, glue, former materials etc. The last many cone/surround designs we just tooled from the comsol geometry, glued together and it worked pretty much as simulated.I can tell you that there is nothing that actually models cones correctly. You are better off learning what a particular cone shape will do, what a dustcap shape and diameter will do and what a surround profile will do. These are the things that make the greatest differences. Basically a study of how these behave versus frequency response is much more informative.
I have talked with Peter Larson about some of his software suite. And showed him the software we use internally which is a wrapper for FEMM 4.2, Calculix and Z-88. It gets us as accurate calculations as COMSOL or Vector Fields or the other megabuck software packages.
What I can tell you from experience is that no one will ever tell you their cone or surround formulations in order to model them accurately. So what we do is literally compare previous measurements and extrapolate.
When I end up having to fix a driver design what often strikes me as strange is the blind belief in a computer simulation. They are ballpark guesses. Nothing more. You can get flux close, if you know every mass added you can get SPL relatively close. But connecting the math and the calculations to the real world is the part that take comparative analysis and practical experience. That starts by noting cone and dustcap shapes and relating them to frequency responses. There are definite patterns.
I delivered a bit of a presentation at the Loudspeaker Sourcing show in 2018 that explained how to use these programs. Carsten Tinggaard was interested in the programs as they were working on a driver that became the Purifi first offering. They were paying quite a lot to have ideas modeled. Hopefully this saved them a lot of money! R&D is not cheap to do even if you are a small team.
So when did you start with Carsten?just to fill in the details at Purifi from 2018: We never paid for simulations - that was in Carstens previous setup. We realised we had to solve the Sd modulation problem and needed to simulate geometric nonlinearity. We decided to work with Comsol and we got an extended trial license. This has been our workhorse for simulation of the soft parts ever since. I build a tool in Matlab to manage and run shape optimisation in Comsol. However, all of the is is not worth much unless it be has good material models. We built up our own testing methodology to derive material models - especially for paper, rubber, glue, former materials etc. The last many cone/surround designs we just tooled from the comsol geometry, glued together and it worked pretty much as simulated.
Nice that you harnessed Matlab. Comsol is certainly easier. But properly constructed simulations form COMSOL or Calculix or Z88 are giving the same answers. All in setting up the Mesh and the mesh properties. Sadly the dominant factors in modeling cones after the basic geometries which you can extrapolate from cone profile measurements is the glue bond. And that cannot be accurately simulated.
- Home
- Loudspeakers
- Multi-Way
- Focal Polykevlar cones