No would be my my advice, it will definitely eat the uncoated polystyrene. Look at the solvent list in the SDS. A while ago I tested water based polyurethane to seal coat EPS and it was fine, but I then sprayed it with a solvent based coating and it dented the test piece, ie penetrated the seal coat.I'm going to need to pick up another can of Dupli-Color I think so I can test it on a bare panel.
One way you could try it would be to apply the spray to a very lightweight paper like yellow tape, or scrim material, let it cure, then stick it to the panel. Can't avoid the slightly extra mass, but I would think the paper and PVA mass would be low compared to the deadener mass
Eucy
Last edited:
That was meant to be yellow trace, but for this application I think scrim cloth would be the best bet...Off to the fabric shop for you.. 🤭
I recall that I considered it would be possible to make roll surrounds like that with this material. Make a mould, lay scrim and spray with synthetic rubber like Rust Oleum leak seal, which is probably not much different than the deadener
Eucy
I recall that I considered it would be possible to make roll surrounds like that with this material. Make a mould, lay scrim and spray with synthetic rubber like Rust Oleum leak seal, which is probably not much different than the deadener
Eucy
Last edited:
Eucy,OK – so after 600+ pages on this thread, I still have fundamental questions, the answers to which may be out there so here goes:
1/ Are we able to establish any type of rules/guidelines for the minimum size of a panel of a given material to allow full development of mid range frequencies (say from 150Hz), accepting that above coincidence, the importance of panel size reduces and hf is highly governed by panel material and the driver.
It's a huge topic, so much to consider. But the one thing I'll say is that I think there is a very good rule for the minimum size of a panel to be able to reach down to say 100 or 150 Hz. And the rule is basically this: the panel must be large enough that, in the intended mounting condition, the fundamental frequency of vibration of the panel has to be at or below the lowest frequency that you want the panel speaker to reach.
There are a few caveats, however. The exciter plays a role too, So just having a panel with a fundamental at 10 Hz doesn't mean it'll play down to 10 Hz. Most of the exciters we use have their own fundamental frequencies in the range of 30 Hz, and really don't power a panel very well until at least about 60 Hz to 80 Hz. But as long as you design a panel and mounting with a fundamental of about 80 Hz or higher, you can pretty much depend on the first peak in your panel's frequency response to be pretty close to (but slightly higher than) the panel's lowest natural frequency (i.e. it's fundamental).
But the challenge still is to figure out how to (1) determine the real Elastic Moduli (plural!) and density of you panel and (2) estimate the fundamental frequency of your panel based on it's properties. There are engineering equations for doing that, but they depend on the boundary conditions of the panel, so can't be stated in a general form. For me, the answer is to use Finite Element Modeling. Which actually helps you do both of these. I have posted information about both previously and would be happy to find and post links to those posts if anybody is interested.
But even if you are not interested in learning how to use FEM, there is a fairly simply way to figure out how big your plate needs to be to obtain a particular fundamental frequency. The method is based on a simple relationship, which is that the fundamental frequency of a panel is inversely proportional to the panel area. So the method is this: make a "small" prototype of your speaker, using the panel material you plan to use, in the thickness and aspect ratio you plan to use, and the same mounting strategy. That is, if you plan to use a frame and attach the two long sides of the panel to the frame with foam, do exactly that for your small prototype. Then do a tap test on your small prototype, as I have described in recent posts, with a close mic in the center of the panel, and tapping the panel as near to the center as you can. Monitor the mic using the RTA function in REW, with no smoothing. You will observe a series of peaks in the frequency response. The fundamental frequency of the panel is the peak at the lowest frequency. Then simply increase the area of the panel in proportion to the decrease the in fundamental frequency that you desire. That is, if the fundamental of your small prototype is 400 Hz, and your design goal is 100 Hz, then simply increase the size (area) of the panel by a factor of four.
One final caveat is that adding an exciter shifts the fundamental slightly higher, typically by about 20 Hz or so. So if you really want a response starting at 100 Hz, adjust the panel size for a fundamental of about 80 Hz.
Eric
Hi Eric - thanks for the response
As a (retired) bridge design engineer, I've used FEM quite a lot, so I'm comfortable with that aspect - However, the nub of what I'm getting to in that question is exactly covered in your quote below:
Can we reliably say that to achieve an acceptable level of output at say 150 Hz, we need a panel with an f0 of no more than 53 Hz (or 35Hz for 100Hz ) - that's 1.5 octaves. That falls within the guide mentioned somewhere (can't remember where) of the limiting output being 2.5 times f0. Again, more testing required, but at least it's a starting point if a panel is to be crossed over for bass output.
Thar doesn't seem to hold for this panel of Andre's:
f0 68Hz but full output down to 55Hz ?? What does that mean?? - was the 68Hz a spurious spike with the real f0 at 35Hz ??
Of course, if no crossover is to be used, then you would seek the lowest f0 possible within size/material constraints, and the above is of no concern.
Related to this is the the question of whether there is a reliable rule of thumb for the rate of natural roll-off of a DML panel - ie can it be (even somewhat generalised) or is it panel and mounting specific ( I need to look back at posted FR plots for this I guess, but it's certainly very steep in the above example). I'll look through some more for this but it's not an easy job - is there a way to search out just figures in the thread??
My focus on this aspect is recent, and driven by the woofer build. Do I try a reduced size panel with this? - it's a whole new ball game - I've so far tested 2 overlaps of the woofer and panel. Overlapping creates a semi-closed back to part of the panel. I've tested the effect of passive backs before and know that they have a (significant) sonic effect but now I have an active pressure backing and I can tell you that the punch effect on the overlapped front panel portion is very significant. More to come on this.......
As for the rest of my previous post re theory - I hope for some feedback on this also
And when I mentioned hardness in that post - it relates to a ball bearing test on wood, which involves both compression and rupture, but it really translates to ZZ compressive strength in other materials. (Maybe I should try a bull-oak panel LOL - I've never come across it but it's an Australian Casuarina and it's reported to be the hardest wood in the world - 3 times harder than Blackwood, 9 times that of Poplar)
Eucy
As a (retired) bridge design engineer, I've used FEM quite a lot, so I'm comfortable with that aspect - However, the nub of what I'm getting to in that question is exactly covered in your quote below:
I agree with this entirely... but even with the F0 analysis, however achieved, we still don't have a practical performance limit for a given panel without extensive trial and error experiments, and I think this is the killer preventing real progress on zooming it to workable, reliable solutions...there's just so much to be done (poor me, whinge whinge etc 🙄😢) . Basically starting with a large-ish panel and cutting it down in increments, moving the exciter, etc etc, while plotting the FR at each stage (what a PITA!) . And is the target to be -3dB at a selected frequency of say 100 or 150Hz, or 0dB ?There are a few caveats, however. The exciter plays a role too, So just having a panel with a fundamental at 10 Hz doesn't mean it'll play down to 10 Hz. Most of the exciters we use have their own fundamental frequencies in the range of 30 Hz, and really don't power a panel very well until at least about 60 Hz to 80 Hz
Can we reliably say that to achieve an acceptable level of output at say 150 Hz, we need a panel with an f0 of no more than 53 Hz (or 35Hz for 100Hz ) - that's 1.5 octaves. That falls within the guide mentioned somewhere (can't remember where) of the limiting output being 2.5 times f0. Again, more testing required, but at least it's a starting point if a panel is to be crossed over for bass output.
Thar doesn't seem to hold for this panel of Andre's:
f0 68Hz but full output down to 55Hz ?? What does that mean?? - was the 68Hz a spurious spike with the real f0 at 35Hz ??
Of course, if no crossover is to be used, then you would seek the lowest f0 possible within size/material constraints, and the above is of no concern.
Related to this is the the question of whether there is a reliable rule of thumb for the rate of natural roll-off of a DML panel - ie can it be (even somewhat generalised) or is it panel and mounting specific ( I need to look back at posted FR plots for this I guess, but it's certainly very steep in the above example). I'll look through some more for this but it's not an easy job - is there a way to search out just figures in the thread??
My focus on this aspect is recent, and driven by the woofer build. Do I try a reduced size panel with this? - it's a whole new ball game - I've so far tested 2 overlaps of the woofer and panel. Overlapping creates a semi-closed back to part of the panel. I've tested the effect of passive backs before and know that they have a (significant) sonic effect but now I have an active pressure backing and I can tell you that the punch effect on the overlapped front panel portion is very significant. More to come on this.......
As for the rest of my previous post re theory - I hope for some feedback on this also
And when I mentioned hardness in that post - it relates to a ball bearing test on wood, which involves both compression and rupture, but it really translates to ZZ compressive strength in other materials. (Maybe I should try a bull-oak panel LOL - I've never come across it but it's an Australian Casuarina and it's reported to be the hardest wood in the world - 3 times harder than Blackwood, 9 times that of Poplar)
Eucy
So I got more Dupli-Color rubber undercoating and my samples of all three dried. I found that Rustoleum was the lightest and stiffest, seems like maybe there's acrylic in it or something. 3M is the heaviest, softest, most flexible and rubber-like. Dupli-Color is right in between the two.
I sprayed an approximately equivalent patch on printer paper and Rustoleum+paper sample weighs 5g, Dupli-Color weighs 7g, and 3M weighs 9g. Dupli-Color is the only one safe for polystyrene foam so it's the winner I think.
I did try spraying 3M on top of Dupli-Color on foam and where Dupli-Color was heavy it protected the foam from 3M, but where it was light the 3M did get through a little bit. 3M on PVA worked fine though - as long as the PVA skin has no holes it protects the foam from 3M solvents.
So Dupli-Color is easiest and cheapest and I already tested it in REW so I know it works well. I'll have to compare XPS, XPS+PVA, XPS+Dupli-Color, XPS+PVA+3M. I've got 2 identical XPS panels already so should be ready this weekend 🙂
@Eucyblues99 if you want to get really crazy you should try densified wood. It's soaked and heated to dissolve some lignan, then compressed and heated to press the fibers much closer together. NilesRed did a youtube video where he made it himself and built a multi-ply panel (about 1" thick I think?) that was able to stop a 9mm bullet. Idk if you can buy it anywhere yet but I think I heard of a company in USA that recently built (or is building) a factory to mass-produce it. Building a large thin panel would be pretty tricky though, unless huge got access to a huge press that can handle the surface area...
I sprayed an approximately equivalent patch on printer paper and Rustoleum+paper sample weighs 5g, Dupli-Color weighs 7g, and 3M weighs 9g. Dupli-Color is the only one safe for polystyrene foam so it's the winner I think.
I did try spraying 3M on top of Dupli-Color on foam and where Dupli-Color was heavy it protected the foam from 3M, but where it was light the 3M did get through a little bit. 3M on PVA worked fine though - as long as the PVA skin has no holes it protects the foam from 3M solvents.
So Dupli-Color is easiest and cheapest and I already tested it in REW so I know it works well. I'll have to compare XPS, XPS+PVA, XPS+Dupli-Color, XPS+PVA+3M. I've got 2 identical XPS panels already so should be ready this weekend 🙂
@Eucyblues99 if you want to get really crazy you should try densified wood. It's soaked and heated to dissolve some lignan, then compressed and heated to press the fibers much closer together. NilesRed did a youtube video where he made it himself and built a multi-ply panel (about 1" thick I think?) that was able to stop a 9mm bullet. Idk if you can buy it anywhere yet but I think I heard of a company in USA that recently built (or is building) a factory to mass-produce it. Building a large thin panel would be pretty tricky though, unless huge got access to a huge press that can handle the surface area...
Quoting my own post, but I later re-read a paper by Christian in the archive relating that this very approach was taken, and commenting on the response differences without actually showing them... Would be good to see if you still have the results ChristianBasically starting with a large-ish panel and cutting it down in increments, moving the exciter, etc etc, while plotting the FR at each stage (what a PITA!)
Eucy
SS ... What was the area of the paper?I sprayed an approximately equivalent patch on printer paper and Rustoleum+paper sample weighs 5g, Dupli-Color weighs 7g, and 3M weighs 9g.
A4 printer paper and I sprayed about 60% of it. Attempted to achieve same thickness but it's very hard to control from a can. It's a crude test but the numbers align with my subjective assessment of each as well. Rustoleum is light and hard, Dupli-Color is medium-weight and softer, 3M is heavy and floppy.
Hello Eucy,OK – so after 600+ pages on this thread, I still have fundamental questions, the answers to which may be out there so here goes:
Something tells me you are not alone in such a situation... about fundamental questions. That's good to see a post searching for "design rules" and I am happy you refer to "my work" which more a tentative to collect and to put things together.
This is missing to me also. There are possibly different behaviors behind this width.1/ Are we able to establish any type of rules/guidelines for the minimum size of a panel of a given material to allow full development of mid range frequencies (say from 150Hz), accepting that above coincidence, the importance of panel size reduces and hf is highly governed by panel material and the driver.
- The front and rear wave cancellation. The DML is said to be "self baffled" as the membrane and the baffle are the same part. I have made at different moments tests to try to find a link between the panel dimension and the low frequency but without success. My last test was even very surprising. I started from a 60x80cm EPS panel and cut it keeping its height (80cm), if I remember, 60, 50, 40 and finally 35cm... All had the same FR. None going down to 150Hz, rather 300Hz. An other observation was with my large plywood panel. The low frequency response goes lower outside compare to in room measurement. The room or the distance from the walls should be part of this question. This for the FR below 300Hz. When the dimension becomes smaller than maybe 30cm, the lower frequency is somehow driven by the panel geometry. The panel starts to cut above 300Hz and more and more with the dimension reduction. If you find a paper about this selfbaffling, please share it.
- The wave attenuation while traveling : everybody might not agree on that but I wonder about the FR smoothness linked to the panel dimensions like if under a certain length, the waves reflected at the edge are not attenuated enough. This is of course depending on the suspension type. A too stiff, or clamped suspension has the stronger reflections.
A second comment is : it is not the coincidence frequency that marks a change in the panel FR. The change occurs much before the coincidence frequency. For a EPS test panel I have, the behavior above let say 1k is for example not influence by the suspension design when the coincidence frequency is in the 8/9k area. I think the change is more linked to what is called the transition frequency which is for DML the equivalent of the Schroeder frequency for rooms. Above this frequency, the number of modes for a frequency is such that the modal behavior is no more visible.
I should find something in my archives about that (from one test to the next one, one dimension was divided by 2) but I don't know if it is relevant as it was a 9mm XPS panel which never gave good results.2/ For a given exciter and material, is there information on output vs size for a range of frequencies..eg say for 500Hz, 1000, etc. ie: what is the response curve for a typical exciter as the panel size varies.
Not sure to follow what you did. When I made test about efficiency, I found a not to bad correlation between the mean SPL in a medium band and the B/µ³. This doesn't mean that second order factor does't play. What was not in the game and it is not a second order parameter, it is the force factor of the exciter. DAEX25SHF-4 is 4.29Tm, and the DAEX30HESF-4 BL not specified... how that can be? I just have a pair of them unmounted... maybe a good candidate for an impedance test with REW. For now, I won't based something on the absolute SPL of the FR of the exciter specification. I am not sure the conditions for such a measure are well under control.3/ Panel Material: We have Christian’s work on panel material selection, and I have been prompted to crawl through this again as a result of my most recent Blackwood panel.
I first tested this material yonks ago at 2.5mm thick against an identically sized 3mm Poplar panel, and although the response was more even that the Poplar, the output level was depressed compared to the Poplar, so I put it away. Having reduced the thickness, I find that the 2mm Blackwood panel using a DAEX30HESF-4 now equals the same size 3mm poplar panel (DAEX25SHF-4) in output level with an exciter rated 10-15dB lower across the whole frequency range.
Strange... How is it possible? We expect all those panels to be linear so if one panel is less efficient at a level, it should remain below when you increase the level for both... except if some psychoacoustic is involved like the FR of each being different, the loudness countour curves, one is the perceived as louder... which suppose it as a larger bandwidth? Sorry here I am thinking loud. Even not a test referring to that on my side.Compare now the Blackwood panel (900x300) with a 1200x400x4mm Cedar panel driven by a DAEX25SHF-4, and it exceeds it at moderate amp levels, with the Cedar only catching up as the power is increased.
Keep in mind that the efficiency value in dB is from an heuristic I "invented" and only for an exciter similar at least in force factor o the DAEX25FHE. There is no academic paper behind it. For the rest it is what we find in the papers or patents about DMLAll this despite the following theoretical figures, which are after all, aimed at efficiency and output levels:
ρ (kg/m3) E (Gpa) h (mm) μ B fc Zm fhigh T=B/μ3 'B/μ A.f0 Eff (dB) Poplar 440 8.9 3 1.32 20.025 4835.46 41.13 8.71 15.17 12.24 87.7 Blackwood 640 14.82 2 1.28 9.88 6778.97 28.45 4.71 7.72 8.73 86.4 NXT 550 0.55 6.6 5436.84 15.24 39.67 12.00 10.88 91.0 Cardboard 140 1 3 0.42 2.25 8137.11 7.78 30.37 5.36 7.27 90.4 Cedar 4mm 370 7.66 4 1.48 40.85 3584.71 62.21 12.60 27.60 16.51 88.5 Acrylic 3.8 8.3 12743.53 44.93 0.15 2.18 4.64 78.9
Note that the 2mm Blackwood panel is theoretically a very poor candidate material (Refer to Christian’s charts for details) (PS: Christian – I can’t follow why figures 3 and 4 show fc <5kHz target when Section 7.1 states targets of 6500Hz < fc < 6500Hz)
I should go in the code to try to remember why I put a line at fc=5k in each graph. In the figure 4 which is related to 7.1, 7.2 (targets), there is an orange horizontal line at fc=6.5k and a green one at 7.5kHz (seen the fc scale on the right)
All what is in my "paper" is for isotropic material. Wood is not. It is orthotropic with different Young modulus along or across the grain. In papers like a thesis about the piano soundboard, an equivalent Young modulus used in first approach is the root mean square of the 2 Young modulus (I hope I am clear enough...) Might it be a possible explanation?With respect to the Blackwood/Cedar comparison, I can understand the results from an intuitive standpoint, but the theoretical performance figures of the 4mm Cedar far exceed those of the 2mm Blackwood. Hence my question 2.
I see also that according to figures in the table above, there is "only" 2dB difference in efficiency between both. I am pretty sure that all this mathematical stuff is not precise enough in such a case.
Could you remind us where the strong high frequency performance of acrylic was reported. I have in mind the video from TypicalBen (still available on Youtube) but if I remember, he said in another video that some measurement mistakes lead to that.Also note the Acrylic data in comparison to the reportedly strong high frequency performance gained from this material. (I don't know what the rest of the range is like with material, but there a a number of tests and written reports on the hf end.)
I don't believe in such rising FR. Ok I don't have a piece of acrylic to make a test. I made tests with PS (the polystyrene used to make "organic glass" like what is sold with frames for pictures). No rising FR for this PS. So for now for me it is in the urban legend category... Let see which evidence will come (or not) on that. I have to admit that my list of possible phenomas that might limit the HF is longer than the ones that increase the HF (not to say this part is empty) when we see in all the FR that the HF decrease is slower than expected from the HF limiter.
I have no indications at the moment to say there is something "wrong" in the basic set of formulas we have. I don't say that because I wrote this synthesis paper. Where I would like to rewrite it is about the target for the coincidence frequency. I think now after more test the the 6.5/7.5k range is too low with the consequenceon the efficiency. But this is another story and I would like more test to be more confident in another target.In summary, unless I’ve messed something up here, it seems to me that the theoretical formulae are not a strong guide to actual material results.
I've a very strong suspicion that one material characteristic which is absent from the plate theory plays a big part in explaining at least some of the apparent discrepancies, and that is hardness !
I am sure that this paper identifies the main levers but is not precise enough. Among the missing parameters, there is the material damping. As mentionned above, it doesn't cover precisely the orthotropic materials.
Do you have measurements of your different woods if possible in the same set up (same room, same position...) to evaluate the difference in efficiency and bandwidth?
I don't answer fully to your questions but I hope you will find new ways and at least you willl have an idea of "where I am"Feedback would be appreciated... please put me out of my misery, this stuff is driving me nuts!😢😢😢😢 .
Cheers
Eucy
To be clearer about where I am with DML it is that I put a to high priority up to now on the lowest frequency and the efficiency. Now, I am more in the idea to explore materials like the PS for a higher coincidence frequency and I hope no strange directivity behaviors in the main audio band even if the efficiency is lower and if it doesn't go down to 150Hz (not sure for that but if necessary, cone are here for that) because one thing remains from the time I wrote the paper you mention : all the targets seem no reachable at the same time.
About the dimensions : I propose a minimum of 35cm and a high ratio (minimum 8/5?) as a safe design rule. We will see the feedback
Christian
I'm glad to see Christian's reply, I hoped he would chime in. I agree with much of Christian's views. In time, I'd like to add more of my own thoughts in response to the great questions raised by Eucy. It's hard to know where to start!
How about here?
For me, the primary objective in developing a DML is to select the panel dimensions, panel elastic moduli, and boundary conditions to create a series of closely and evenly spaced well radiating natural frequencies. This is the most reliable way I know of to get a reasonably flat frequency response over the first several octaves of response.
Here's the harsh part. My opinion only. And I'm happy to hear other views: If you don't know what the natural frequencies of your panel are, and are not targeting such a series of natural frequencies, you are not actually designing a DML. You are sticking an exciter on a panel and hoping for the best.
Eric
How about here?
For me, the primary objective in developing a DML is to select the panel dimensions, panel elastic moduli, and boundary conditions to create a series of closely and evenly spaced well radiating natural frequencies. This is the most reliable way I know of to get a reasonably flat frequency response over the first several octaves of response.
Here's the harsh part. My opinion only. And I'm happy to hear other views: If you don't know what the natural frequencies of your panel are, and are not targeting such a series of natural frequencies, you are not actually designing a DML. You are sticking an exciter on a panel and hoping for the best.
Eric
@Eucyblues99 , @Veleric
Hello,
Sorry no times at the moment to read the posts... just an additional information on top of my previous post, an impedance measurement of the DAEX30HESF gives a BL 5,5Tm. So for the same material, it should give an additional +2dB compare to the DAEX25SHF which is said for 4.29Tm in its spec (I don't have this model).
Christian
Hello,
Sorry no times at the moment to read the posts... just an additional information on top of my previous post, an impedance measurement of the DAEX30HESF gives a BL 5,5Tm. So for the same material, it should give an additional +2dB compare to the DAEX25SHF which is said for 4.29Tm in its spec (I don't have this model).
Christian
I decided to compare the heavily PVA'd XPS with 2 coats of rubber to the small planar magnetic speaker I've got tonight. My goal is to get the DML 'as good as' the planar speaker but it needs a lot of help. Here's why I've focused so much on damping:
We can see there how the green DML keeps ringing for so long in this close-mic impulse overlay. This is even more wild in the 3ft measurement:
I think this is why the FR with no smoothing shows such a wild and hairy look compared to the planar:
Interestingly the close-mic distortion measures better for the DML, though for the usable range I guess they're both low enough that the difference doesn't matter:
Oh, and there is some (old) EQ'ing in these tests and the DML is crossed at 150hz. It has that weird ~80hz spike though and hole around 190hz that makes it look like it isn't crossed, but it is, and sub is muted.
This panel already has heavy PVA and a heavy coat of rubberized undercoating and compared to many other panels it is far more damped. Even still it has a very long way to go to come close to the planar speaker. It isn't even close to the very cheap 3.5" cone speaker I tested either.
We can see there how the green DML keeps ringing for so long in this close-mic impulse overlay. This is even more wild in the 3ft measurement:
I think this is why the FR with no smoothing shows such a wild and hairy look compared to the planar:
Interestingly the close-mic distortion measures better for the DML, though for the usable range I guess they're both low enough that the difference doesn't matter:
Oh, and there is some (old) EQ'ing in these tests and the DML is crossed at 150hz. It has that weird ~80hz spike though and hole around 190hz that makes it look like it isn't crossed, but it is, and sub is muted.
This panel already has heavy PVA and a heavy coat of rubberized undercoating and compared to many other panels it is far more damped. Even still it has a very long way to go to come close to the planar speaker. It isn't even close to the very cheap 3.5" cone speaker I tested either.
I'm feeling like some of that ringing, or potentially a lot of it, may be caused (or at least exacerbated) by the mass of the exciter hanging on the panel. I'm getting really close to buying a huge magnet to put behind the panel and then tape just a coil to the panel. This will be a big reduction in moving mass and I think it might tame this ringing. Without the exciter attached a thinner panel might be possible too.
In theory the exciter and panel should move in opposite directions and cancel each other out making the mass not matter, but I don't think that's true. First, the mass of the panel is not the same as the exciter so they aren't balanced. Second, the panel has some elasticity so as the exciter acceleration is applied the panel bows and not all of the panel's mass is moved right away, and some extra effort is required to bend the panel I guess, and after acceleration stops the bend inverts snapping the panel edges back the other way. And of course the exciter mass is attached via the spider spring so it's bouncing all around with that. There's so much going on that it surely the push-pull is not balanced, especially when multiple frequencies are involved, and the end result is likely ringing like the impulse graph shows. With just a coil on the panel these elasticity dynamics will still exist but those variables for the exciter mass and spider spring will no longer complicate the system.
It's an expensive test at ~$200 for a huge neodymium, and obviously it's dangerous to work with and will need a lot of wood for the frame, and probably a safety cage around the whole panel... But I'm probably going to figure out how to build it and give it a try.
In theory the exciter and panel should move in opposite directions and cancel each other out making the mass not matter, but I don't think that's true. First, the mass of the panel is not the same as the exciter so they aren't balanced. Second, the panel has some elasticity so as the exciter acceleration is applied the panel bows and not all of the panel's mass is moved right away, and some extra effort is required to bend the panel I guess, and after acceleration stops the bend inverts snapping the panel edges back the other way. And of course the exciter mass is attached via the spider spring so it's bouncing all around with that. There's so much going on that it surely the push-pull is not balanced, especially when multiple frequencies are involved, and the end result is likely ringing like the impulse graph shows. With just a coil on the panel these elasticity dynamics will still exist but those variables for the exciter mass and spider spring will no longer complicate the system.
It's an expensive test at ~$200 for a huge neodymium, and obviously it's dangerous to work with and will need a lot of wood for the frame, and probably a safety cage around the whole panel... But I'm probably going to figure out how to build it and give it a try.
@Eucyblues99 , @Veleric
Hello,
Sorry no times at the moment to read the posts... just an additional information on top of my previous post, an impedance measurement of the DAEX30HESF gives a BL 5,5Tm. So for the same material, it should give an additional +2dB compare to the DAEX25SHF which is said for 4.29Tm in its spec (I don't have this model).
Christian
Hi Christian - thanks... That makes sense but also indicates the Dayton spec sheet for the DAEX30HESF must be incorrect, as the output levels in the graph are way down on the DAEX25SHF.
Eucy
minimum 8/5 ?? - I don't follow that I'm afraid - is that a typo??About the dimensions : I propose a minimum of 35cm and a high ratio (minimum 8/5?) as a safe design rule. We will see the feedback
Eric, I think that's actually what most experimenters using this forum do. Then they play around with improvements. Using the general guidelines from here and other published information. Surely they will still be DMLs, just not optimised ones. They do that because most don't have access to or knowledge of FEM and so must start with a physical panel based on material and size preferences and guesstimates from here and elsewhere, and invent the wheel all over again with a lot of waste of time, material and money along the way - I guess that's part of the experience, but some improvements in the process can surely be made.If you don't know what the natural frequencies of your panel are, and are not targeting such a series of natural frequencies, you are not actually designing a DML. You are sticking an exciter on a panel and hoping for the best.
Perhaps modelling and tabulating expected values for a range of panel sizes and materials would be an effective starting point for generalised use. I remember you once provided a graph of modal density vs aspect ratios, pointing to the benefits of high aspect ratios. Maybe that can be extended to cover different material values as well as panel ratios - I'll have to look it up again.
(I also remember that we had a somewhat lengthy discussion regarding the pursuit of the lowest f0 (me) vs the greatest modal density (you) - 3 ply vs 5 ply. 😉 ) . And now I'm trialling 4 ply (LOL)
Eucy
SS- Maybe re-post the FR with 1/6th octave smoothing to get a clearer picture. The human ear can't distinguish those spikes. Also look at psych smoothing-it'll make you feel better ( 🙂 ). And what does it actually sound like compared to the commercial planar (that doesn't look that flash either btw).I decided to compare the heavily PVA'd XPS with 2 coats of rubber to the small planar magnetic speaker I've got tonight. My goal is to get the DML 'as good as' the planar speaker but it needs a lot of help. Here's why I've focused so much on damping:
View attachment 1327453
We can see there how the green DML keeps ringing for so long in this close-mic impulse overlay. This is even more wild in the 3ft measurement:
View attachment 1327454
I think this is why the FR with no smoothing shows such a wild and hairy look compared to the planar:
View attachment 1327455
Interestingly the close-mic distortion measures better for the DML, though for the usable range I guess they're both low enough that the difference doesn't matter:
View attachment 1327456
Oh, and there is some (old) EQ'ing in these tests and the DML is crossed at 150hz. It has that weird ~80hz spike though and hole around 190hz that makes it look like it isn't crossed, but it is, and sub is muted.
This panel already has heavy PVA and a heavy coat of rubberized undercoating and compared to many other panels it is far more damped. Even still it has a very long way to go to come close to the planar speaker. It isn't even close to the very cheap 3.5" cone speaker I tested either.
Eucy
If I had used smoothing in that FR it wouldn't have shown the correlation between the ringing on the impulse graph and the hairy-looking nature of the FR. I believe that if the impulse response can be cleaned up to look more like the planar (or any other cone speaker) then the FR extreme swings will also be cleaned up. There will still be lumps from the modal nature of course.
I don't know if myself or anyone else can hear those unsmoothed spikes directly, but they are a sign of what is going on underneath and I believe that can be heard. Additionally that high variability could cause more intense interference issues, I suspect. In this case I am pretty sure it is ringing in the panel and that muddles the sound clarity and paints those long tails on the FR graph.
When doing A/B test between this panel and this planar I can hear a slight difference in that clarity. It isn't a huge difference that I hear, if I didn't do the A/B I wouldn't know which is which (if I ignore the planar giving a 'small' sound while DML gives 'big' sound), but when switching to planar there is a little more 'magic' to the sound which makes the tingle response come more easily. This comes from clarity, I am certain.
The planar I tested is a GRS PT2522 mounted in a cardboard box with a jacket in box for damping... lol. It was a mockup for a center channel I was going to build but I decided to do DML instead.
I don't know if myself or anyone else can hear those unsmoothed spikes directly, but they are a sign of what is going on underneath and I believe that can be heard. Additionally that high variability could cause more intense interference issues, I suspect. In this case I am pretty sure it is ringing in the panel and that muddles the sound clarity and paints those long tails on the FR graph.
When doing A/B test between this panel and this planar I can hear a slight difference in that clarity. It isn't a huge difference that I hear, if I didn't do the A/B I wouldn't know which is which (if I ignore the planar giving a 'small' sound while DML gives 'big' sound), but when switching to planar there is a little more 'magic' to the sound which makes the tingle response come more easily. This comes from clarity, I am certain.
The planar I tested is a GRS PT2522 mounted in a cardboard box with a jacket in box for damping... lol. It was a mockup for a center channel I was going to build but I decided to do DML instead.
Eucy,Can we reliably say that to achieve an acceptable level of output at say 150 Hz, we need a panel with an f0 of no more than 53 Hz (or 35Hz for 100Hz ) - that's 1.5 octaves. That falls within the guide mentioned somewhere (can't remember where) of the limiting output being 2.5 times f0. Again, more testing required, but at least it's a starting point if a panel is to be crossed over for bass output.
You sent me looking for the articles where the 2.5 x fo figure was cited. I didn't find the exact one that I recall. (Christian, can you?) I'm all but certain it was from an article by Henry Azima or his group at NXT. I did find this one, by Azima himself.
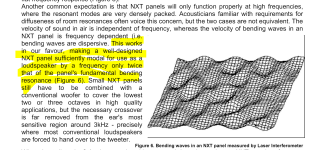
From here:
https://loudmagnet.com/html/pdf/NXT Technology.pdf
I'm not sure how it went from 2x to 2.5x or the other way around, however.
My inference (which could certainly be wrong) is that the 2.5x came from the fact that for most low aspect ratio panels, the fundamental is pretty far removed (i.e. much lower than) from the next higher natural frequencies, so there is little chance of filling in the gap in between. So maybe the next higher productive mode (say the 1,3 or 3,1) is where they figured the acceptable response really started.
But what I have found is that with high aspect ratio panels (supported around the perimeter) the fundamental is close enough in frequency to the next higher natural frequencies that the good response can begin at the fundamental itself, rather than 2x or 2.5x the fundamental.
Eric
Eucy,As a (retired) bridge design engineer, I've used FEM quite a lot, so I'm comfortable with that aspect
Are you using FEM for your DML work? If so, what program? Can it handle orthotropic materials?
Sorry if you have already mentioned it and I don't recall!
Eric
- Home
- Loudspeakers
- Full Range
- A Study of DMLs as a Full Range Speaker