Yes, very modest indeed for live work. But it's a start. I think Beyma does a 100W 16 ohm bass shaker, which seems to beg for four of them in parallel for 400W, 4-ohms. Could be interesting...I guess one problem is that there are no 200w exciters, and that it is still a quite modest power handling for a sub?
In any case, I really like the sound of an open baffle woofer. I'll have to find out for myself why this is not used in small to medium sized live gigs. Subs are omnidirectional anyway (unless using bass horns large enough to fill a stadium) so that's not part of the problem. It could be a size or robustness thing.
Exactly. 160W-worth of XT32 exciters deliver more Bl (Bl=8.54 in series/parallel) than the Alpha15a (Bl=7.7). If the XT32's were all in parallel then Bl would be 17.08. But then again, I'm not expecting such panels to be used for heavy bass in an outdoor techno/rave setup, in which case I would also definitely go for enclosed subs like you would do.If you have a loose suspension around the frame, allowing the whole plate to move as freely as a cone, you still have around half the Xmax of the 15" driver, so you would need double the surface area. Since 4x Xite 32 has more than double the BL of an eminence 15", it should be able to push that air and almost match the output of the 200w cone driver.
I'm aiming for a flat response down to say 60Hz, which should be sufficient for most small indoor venues where even 100W of clean sound could be too much.
I have a bit of a head-scratch on the Xmax thing.
The Excite XT32's have their Xmax specified as ±1.6mm, which I think is the correct way of specifying it. Eminence says the Alpha15a is 3.8mm, which, to my mind, is ±1.9mm.
I think it's the same issue (badly specified confusion) when specifying peak voltage or peak-to-peak voltage, or wattage, or average wattage, or RMS or or PMPO.
But IF the Xmax is really an issue, then I have no problem with surface area. A square baffle, say 40 x 40cm in size, which is only-just big enough to accommodate a 15" speaker, has a surface area of 1,600sq.cm. The speaker itself has an active surface area of only 850sq.cm or so, which is why a squarish DML panel, 40 x 40cm in size, has almost double the active surface area of a 15" speaker available to do the work.
I think this could be a good tree to bark at.
I have posted this patent from 1961, quite a few times over the years.
It has some good ideas for producing low frequencies from a panel with adjustable resonant frequencies.
Also smoothing out dips in responses in the 100hz to 200hz region.
I would still keep serious modern low frequencies well away from these types of panels.
Although some panels are capable of producing frequencies down to 40hz at moderate levels.
The exciters that I have seen so far are not designed to handle that amount of power.
So multiple exciters on a low frequency panel is probably the way to go for me.
Maybe Covering frequencies from 40hz to about 300hz, maybe full range if it matches my eps panels well ?
Steve.
https://patents.google.com/patent/U...=priority:19610101&oq=inventor:+A+Cohen++1961
It has some good ideas for producing low frequencies from a panel with adjustable resonant frequencies.
Also smoothing out dips in responses in the 100hz to 200hz region.
I would still keep serious modern low frequencies well away from these types of panels.
Although some panels are capable of producing frequencies down to 40hz at moderate levels.
The exciters that I have seen so far are not designed to handle that amount of power.
So multiple exciters on a low frequency panel is probably the way to go for me.
Maybe Covering frequencies from 40hz to about 300hz, maybe full range if it matches my eps panels well ?
Steve.
https://patents.google.com/patent/U...=priority:19610101&oq=inventor:+A+Cohen++1961
While I understand that most panels don't produce a lot of low frequency sound, by feeding them full range signal aren't they trying to produce it? Therefore getting all the heat and power, unless of course they are high passed in some way.
So the bond strength is interesting. The coating has a powdery feel and sometimes when it sprays out of the can it forms fine strings. It sticks pretty good to the panel and can easily withstand gentle hands, but if you drag something like a popsicle stick across the surface it will scrape up a line in the coating pretty easily. I'm wondering if it needs a hard coating on top. I tested some acrylic lacquer for compatibility and it worked on top of cured undercoating, but idk if it impacts the damping performance or not.<snip>
They did have Dupli-Color rubberized undercoat for $8 though and the clerk said it's basically the same as 3M so I grabbed a can. I'm sure 3M is actually better, but this is just a cheap test anyway.
<snip>
I still haven't done any measurements but I did take an awful panel from the past with tons of ringing and I sprayed about 10g or so of undercoat on each side and now the panel has far less ringing. I'm guessing at least 50% reduction. The coating is difficult to put on lightly and the thicker spots takes several hours in the sun to cure, so unfortunately I won't be able to do tests the same day that I apply the coating.
Oh, and of course the exciter cannot mount to this coating, I'll have to mask off the mounting area.
Yes, but with the right suspension you can make it act more like a cone for LF content, and will not actually have to bend the plate at those frequencies. Unless you add a baffle or cabinet it will be just like a cone in free air, meaning it will cancel itself out a lot, so while the cone does move in response to the force from the exciter, the perceived loudness will be low because the acoustic cancellation. But with a design that doesn't have a compliant frame, like the one I'm using, indeed a lot of sub energy will just turn into heat.While I understand that most panels don't produce a lot of low frequency sound, by feeding them full range signal aren't they trying to produce it? Therefore getting all the heat and power, unless of course they are high passed in some way.
I'm also not interested in making a full range DML. It would not be practical nor sound good for the kind of music and levels I like to play. But I can imagine getting a very natural and clear sound with no crossovers anywhere in the range, and that it could work well for acoustic music.
I did some test of the XPS panel with heavy PVA on both sides and CLD tape. I did at 6ft, 3ft, and extremely close mic. Then I pulled off all the tape, nothing else changed, and repeated tests.
I'm not really sure how to interpret the results except to say that the CLD tape did flatten out the FR curve while lowering most of it a few dBs. The CLD does make the spectrogram more messy, I think. I've attached the results for anyone else to provide feedback.
I learned tonight that one should only use butyl rope for the mounts for a permanent attachment. After I finished these tests it was very hard to remove the panel, and when I did the butyl stretched into strings and went everywhere. As I pulled it off panel it took PVA skin with it in a lot of places:
I'm not really sure how to interpret the results except to say that the CLD tape did flatten out the FR curve while lowering most of it a few dBs. The CLD does make the spectrogram more messy, I think. I've attached the results for anyone else to provide feedback.
I learned tonight that one should only use butyl rope for the mounts for a permanent attachment. After I finished these tests it was very hard to remove the panel, and when I did the butyl stretched into strings and went everywhere. As I pulled it off panel it took PVA skin with it in a lot of places:
Attachments
BMW
OOPS 🤭
This is the BMW I meant:
600x30 Bending Mode Woofer...test bed
OOPS 🤭
This is the BMW I meant:
600x30 Bending Mode Woofer...test bed
That is a VERY NICE surround!600x30 Bending Mode Woofer...test bed
How'd you do that?
Unless it's just an optical illusion, it looks like you have a half-roll surround there.
Nice. Tell us more details. What's the panel? What is the suspension? What does the cross section of the frame/panel/suspension look like? What is 600x30? Or is it 600x300? What FR do you want to cover with the woofer?600x30 Bending Mode Woofer...test bed
Eric
Yep...600x300
There's a lot to tell so I'll put some details together
There's a lot to tell so I'll put some details together
Eucy,On multiple tests in the same conditions, I find my results to be inconsistent in terms of the resonant peak locations.
The resonant peak locations in the tap test shouldn't be inconsistent, if nothing changes in the supports, tap location, and mic location. If the peak frequencies are inconsistent, something isn't quite right. Maybe you should try something other than your finget for tapping.
I did a bunch of taps on a PS foam panel with various "tappers". The panel was suspended by two strips of painter's tape, the mic was at the center of the panel, and I tapped about 1/2" above the mic. The results, even with different tappers, were incredibly consistent (see image below). Even to some of the tiniest details like the little dip at 280 Hz (no idea what that is!). The bottom curve (purple) is my attempt with my finger as the tapper. It still shows the same peaks, but is the least clear of all the results. The image attached below shows all the different tappers I tried. For the screwdriver, scraper and scissors I tapped with the handle end. I was surpised that I found the hard, light ones to be the easiest to use (like the Sharpie Marker and pencil), particularly for the panel suspended with tape strips. The heavy and/or soft ones (especially my fingertip) transferred too much momentum to the panel and and made it swing into the mic. But the marker and pencil both worked great. The best tapping technique seems to be to hold the tapper lightly between your finger tips so it can swing freely between your fingertips just before it strikes the panel.
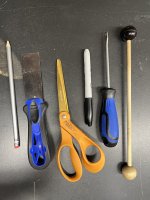
Recently, I gained access to a drum sander, so I decided to sand off the rear ply, and thin the front face slightly from each panel.
It does indeed look great! But be cautious about the sanding. Plywoods are made with symmetric structure. if you disrupt that, a panel is far more likely to bend, warp, twist etc, especially when the humidity changes.I have high hopes for this material. It is recognised as a great tonewood, which is always my main starting point. It's also attractive.
Eric
Thanks Eric - Yes - I'm sure it was me, but in this instance I was really only testing for damping so I was more interested in the shape of the peaks rather than their location - The marker pen/pencil is a good tip - I just need an extra set of hands 🙂
However, in the case of this material, there's no sign so far of a propensity to warp and it is far less 'wobbly' that poplar. An important characteristic of this timber (btw: from Tasmania, the State of my birth 👍) as well a being beautiful, it is also very hard, even though the density is only 50% more than poplar, that's why I mentioned ( I think) that it almost feels like a thin fibreglass panel in stiffness.
Comparative figures:
https://www.wood-database.com/australian-blackwood/ (referred to here as Tas Blackwood where it originates)
https://www.wood-database.com/white-poplar/
Density (Kg/m3) : Poplar 440 / Blackwood 640
Janka Hardness (N) : Poplar 1820 / Blackwood 5180
Mod E (GPa) : Poplar 8.90 / Blackwood 14.82
The natural tone I think is brighter/crisper than that of Cedar (which I like a lot), and maybe (not sure) poplar also, and although I haven't tested these panels yet due to a range of circumstances, the highs are great to my ears, and these panels by themselves do seem to have noticeable bass for their size. That may be the material and/or the mounting.
Either way it was a trial that I am very happy with so far, (although my daughter still prefers the sound of the Cedar panels seen in the background of the pics above (I admit they do sound very nice, but freely supported so the bass is not developed to full potential - I'll modify them someday) )
Eucy
Well, actually they're asymmetric as they a 3/5/7 etc plies with the final faces longitudinal, so I now have 4 plies, 2 in each direction. But I take your point.It does indeed look great! But be cautious about the sanding. Plywoods are made with symmetric structure. if you disrupt that, a panel is far more likely to bend, warp, twist etc, especially when the humidity changes.
However, in the case of this material, there's no sign so far of a propensity to warp and it is far less 'wobbly' that poplar. An important characteristic of this timber (btw: from Tasmania, the State of my birth 👍) as well a being beautiful, it is also very hard, even though the density is only 50% more than poplar, that's why I mentioned ( I think) that it almost feels like a thin fibreglass panel in stiffness.
Comparative figures:
https://www.wood-database.com/australian-blackwood/ (referred to here as Tas Blackwood where it originates)
https://www.wood-database.com/white-poplar/
Density (Kg/m3) : Poplar 440 / Blackwood 640
Janka Hardness (N) : Poplar 1820 / Blackwood 5180
Mod E (GPa) : Poplar 8.90 / Blackwood 14.82
The natural tone I think is brighter/crisper than that of Cedar (which I like a lot), and maybe (not sure) poplar also, and although I haven't tested these panels yet due to a range of circumstances, the highs are great to my ears, and these panels by themselves do seem to have noticeable bass for their size. That may be the material and/or the mounting.
Either way it was a trial that I am very happy with so far, (although my daughter still prefers the sound of the Cedar panels seen in the background of the pics above (I admit they do sound very nice, but freely supported so the bass is not developed to full potential - I'll modify them someday) )
Eucy
Last edited:
I did some test of the XPS panel with heavy PVA on both sides and CLD tape. I did at 6ft, 3ft, and extremely close mic. Then I pulled off all the tape, nothing else changed, and repeated tests.
I'm not really sure how to interpret the results except to say that the CLD tape did flatten out the FR curve while lowering most of it a few dBs. The CLD does make the spectrogram more messy, I think. I've attached the results for anyone else to provide feedback.
I learned tonight that one should only use butyl rope for the mounts for a permanent attachment. After I finished these tests it was very hard to remove the panel, and when I did the butyl stretched into strings and went everywhere. As I pulled it off panel it took PVA skin with it in a lot of places:
View attachment 1324760
Arrgh - I meant to mention this before - If you look through my posts (don't bother, it's too hard), you would see that I am a LIBERAL user of GREEN masking tape (probably known to you as painter's tape). I use it for all temporary fixings, mounts, exciters etc. Put layers on both faces and glue etc to those, then when finished, you can readily peel the tape off with the mess above and have a clean panel/frame to test again. The green tape is the best for medium term stick and easy removal. The basic buff colour tape is not good to remove, and the blue doesn't stick well enough.
Cheers
Eucy
SS,I did some test of the XPS panel with heavy PVA on both sides and CLD tape. I did at 6ft, 3ft, and extremely close mic. Then I pulled off all the tape, nothing else changed, and repeated tests.
I'm not really sure how to interpret the results except to say that the CLD tape did flatten out the FR curve while lowering most of it a few dBs. The CLD does make the spectrogram more messy, I think. I've attached the results for anyone else to provide feedback.
I learned tonight that one should only use butyl rope for the mounts for a permanent attachment. After I finished these tests it was very hard to remove the panel, and when I did the butyl stretched into strings and went everywhere. As I pulled it off panel it took PVA skin with it in a lot of places:
I looked at your results. Looking at the close mic spectrograms and FR, I would say that your panel is quite well damped by the butyl rope alone. It's not obvious to me that the CDL tape is adding much to the damping, but maybe a little. It does seem to flatten the 3 ft and 6 ft FR. I'm not sure I would attribute that to the damping aspect of it.
Have you tried it without the PVA? I'm not really sure what it actually does. Does it stiffen? Damp? Create magic?
I use the same pink foam for a lot of tests, and I have the properties (foam uncoated) pretty well characterized. are you using the 0.5" nominal foam? I did a quick finite element model and was happily surprised at how well it predicted the resonances at 35 and 95 Hz that show up in your close mic test. I'll share those results tomorrow. If you are interested in doing a few tap tests, I think we could map out the first 8 or 10 modes (resonant frequencies and corresponding mode shapes).
Which exciter is it and where is it placed?
When you did the close mic tests, where was the mic positioned? It doesn't look like it was exactly opposite the exciter. Nothing wrong with that, but just noting it.
Yeah, the butyl rope could ruin a PS panel for sure. Good thing XPS is cheap, unless you've invested a lot of time into coating it with PVA. And you don't really need the clamshell frames to use it. You could have just used the butyl between the panel and one half of the frame. That would not have saved your panel, but you'd only have to peel the butyl off one of your frame halves, not two! My CF/balsa panel is still mounted to the frame with butyl rubber. The CF epoxy has a much stronger surface than XPS, so I expect I can get it off without ruining the panel, but I have yet to try. I'm not looking forward to it.
Eric
I'm thinking that the CLD did indeed dampen a little, but most of it was just from the mass. With all that tape applied there probably was significant damping from the CLD effect too, but the mass has the bigger effect. It's like a physical EQ, as discussed previously on this thread. I don't think that 140g mass was worth it though; there are better solutions.
The PVA was already on this panel and I wasn't going to try to remove it. It was an undiluted heavy coat of PVA. It adds some rigidity and a lot of damping and the panel is definitely better with it than without. I'm sure we all know what the PVA skin is like, but my observation is that it isn't very rigid by itself but it has good tensile strength so when the panel tries to bend it pulls on the skin which reduces bending. It has a very slight elastic nature, a slow partial return after bending, which gives damping. There is a huge difference when tapping an untreated XPS panel vs a heavily PVA'd one.
The XPS is the Foamular 250, 2"x4'x8' and I cut it down with a hot wire. This panel is something like 10.25"x20.75"x0.75" but the hole in the frame is 9"x19" front and back. With the frame I clamp the panels pretty firmly with foam strip full length top and bottom (short sides) for testing as I've found a firm clamp gives the best low end, typically. Sometimes when I try it looser that is better but most of the time a firm clamp that isn't enough to compress the XPS is best. If the panel gets squished that seems to be too much.
For all those measurements the DAEX32EP-4 exciter is placed approx 2/5 & 2/5 position. It isn't an exact measurement but I have some guide lines on the frame and I try to line it up by hand. Stuck on with carpet tape. For the close mic I held the mic very near the exciter but on the front side of panel, with exciter on back side. I don't have a tripod so I had to hold it by hand with a finger or two against the frame for stability. I was definitely within 1.5" of the center of the driver, and the mic distance was about 1/8" from the panel. I have two of these drivers and they've both been pried off many many times. I suspect they always were low in HF but the abuse has made them even lower. Twice I've had to super glue the foot/bobbin.
I tested the rubberized undercoat today and it gave a pretty nice improvement. Distortion was significantly flatter and lower. The Impulse EDT is lower than anything else I've tested recently. It was a medium coating so I sprayed again and am waiting for this heavy coat to dry. I'll test tomorrow and share both.
I also tested the coating on old panel that used to ring very badly and now it is actually ok. Not as good as the PVA'd panel, but went from 'garbage' to 'usable', I'd say.
I also tested the 5mm thick heavily epoxied panel today that I spoke about some days ago and it wasn't that great. Too heavy, and too floppy for its weight I think.
The PVA was already on this panel and I wasn't going to try to remove it. It was an undiluted heavy coat of PVA. It adds some rigidity and a lot of damping and the panel is definitely better with it than without. I'm sure we all know what the PVA skin is like, but my observation is that it isn't very rigid by itself but it has good tensile strength so when the panel tries to bend it pulls on the skin which reduces bending. It has a very slight elastic nature, a slow partial return after bending, which gives damping. There is a huge difference when tapping an untreated XPS panel vs a heavily PVA'd one.
The XPS is the Foamular 250, 2"x4'x8' and I cut it down with a hot wire. This panel is something like 10.25"x20.75"x0.75" but the hole in the frame is 9"x19" front and back. With the frame I clamp the panels pretty firmly with foam strip full length top and bottom (short sides) for testing as I've found a firm clamp gives the best low end, typically. Sometimes when I try it looser that is better but most of the time a firm clamp that isn't enough to compress the XPS is best. If the panel gets squished that seems to be too much.
For all those measurements the DAEX32EP-4 exciter is placed approx 2/5 & 2/5 position. It isn't an exact measurement but I have some guide lines on the frame and I try to line it up by hand. Stuck on with carpet tape. For the close mic I held the mic very near the exciter but on the front side of panel, with exciter on back side. I don't have a tripod so I had to hold it by hand with a finger or two against the frame for stability. I was definitely within 1.5" of the center of the driver, and the mic distance was about 1/8" from the panel. I have two of these drivers and they've both been pried off many many times. I suspect they always were low in HF but the abuse has made them even lower. Twice I've had to super glue the foot/bobbin.
I tested the rubberized undercoat today and it gave a pretty nice improvement. Distortion was significantly flatter and lower. The Impulse EDT is lower than anything else I've tested recently. It was a medium coating so I sprayed again and am waiting for this heavy coat to dry. I'll test tomorrow and share both.
I also tested the coating on old panel that used to ring very badly and now it is actually ok. Not as good as the PVA'd panel, but went from 'garbage' to 'usable', I'd say.
I also tested the 5mm thick heavily epoxied panel today that I spoke about some days ago and it wasn't that great. Too heavy, and too floppy for its weight I think.
Moray James.
This is a plot of the veneer panel ,at about 8inches.
Obviously this is not the response at 3m, but it is good to see that it has a decent near field output response .
I think I will make a youtube video with the proplex panel, and switch between the two for you to assess.
Looking at the plot I think I have decided to apply my dome to see if I can flatten the response at the 1k and 10k areas.
These are probably caused by the exciter cavity and inner coil surface.
I'm not sure if it is worth using weights or mounting points to improve the low end performance as I will XO higher up anyway .
The panel sounds pretty good as it is, but sorting out the exciter panel noises, will improve things immensely.
Although the overall sound will be the same.
Steve.
This is a plot of the veneer panel ,at about 8inches.
Obviously this is not the response at 3m, but it is good to see that it has a decent near field output response .
I think I will make a youtube video with the proplex panel, and switch between the two for you to assess.
Looking at the plot I think I have decided to apply my dome to see if I can flatten the response at the 1k and 10k areas.
These are probably caused by the exciter cavity and inner coil surface.
I'm not sure if it is worth using weights or mounting points to improve the low end performance as I will XO higher up anyway .
The panel sounds pretty good as it is, but sorting out the exciter panel noises, will improve things immensely.
Although the overall sound will be the same.
Steve.
Attachments
Eucy,Well, actually they're asymmetric as they a 3/5/7 etc plies with the final faces longitudinal, so I now have 4 plies, 2 in each direction. But I take your point.
However, in the case of this material, there's no sign so far of a propensity to warp and it is far less 'wobbly' that poplar.
I'm glad they haven't warped. Let's hope they don't!
But I suspect you are thinking of a different type of symmetry than what I was referring to. I was talking about symmetry around the plane that passes though the center of the panel's thickness. The common 3 ply, 5 ply and 7 ply etc plywoods are all symmetric with respect to that plane. I suspect you are thinking about symmetry between the two axes of the plate's length and width directions. And yes, having 2 plies oriented in each of those directions would be more symmetric in that sense than having say 2 plies with grain going in one direction and 3 plies going in the perpendicular direction.
But the symmetry that you need in to best avoid warping is to have symmetry around the center of the plate's thickness. In the sketch below of the cross section of a 5 ply plate, the plies are arranged symmetrically around the center plane (dotted line). Plies 1,3, and 5 have grain running parallel to the x direction, and 2 and 4 have grain running parallel to the y direction. To have a balanced structure with the least likelihood of warping, the plies on opposite sides (say, 2 and 4 or 3 and 5) of the structure should be the same thickness, and orientation.
And conversely, pretty much the worst thing you can do, from a warping standpoint, would be a two layer structure with the grain running in perpendicular directions in the two layers. A structure like that will warp like a potato chip!
Eric

Is there any way I can measure the center image with REW? It would be great to see some numbers to help find the best arrangement for the clearest center image.
- Home
- Loudspeakers
- Full Range
- A Study of DMLs as a Full Range Speaker