Yes will snaps some pics Steve.
Printer I'm using is one of these: https://www.tenlog3d.com/tenlog-tl-...support-pva-tpu-abs-pla-600w-version_p11.html
Now I'm thinking if I even need to outsource printing (don't have room for a larger printer now, and they are costly) to make larger panels. If I get sufficient bass from 300x300, what will I gain from larger panels, rather than several smaller?
As I understand according to Tectonic, the way DML can be more efficient is that instead of a small surface acting as a piston generating waves, those waves are generated over a larger surface. The amplitude of the waves are the same, but basically the waves are bigger, so the total energy emitted will be greater.
So I suspect a smaller panel will not have as much of the benefit from DML? So I might get similar 1m on axis performance, but will need more wattage for good coverage compared to a larger panel?
Printer I'm using is one of these: https://www.tenlog3d.com/tenlog-tl-...support-pva-tpu-abs-pla-600w-version_p11.html
Now I'm thinking if I even need to outsource printing (don't have room for a larger printer now, and they are costly) to make larger panels. If I get sufficient bass from 300x300, what will I gain from larger panels, rather than several smaller?
As I understand according to Tectonic, the way DML can be more efficient is that instead of a small surface acting as a piston generating waves, those waves are generated over a larger surface. The amplitude of the waves are the same, but basically the waves are bigger, so the total energy emitted will be greater.
So I suspect a smaller panel will not have as much of the benefit from DML? So I might get similar 1m on axis performance, but will need more wattage for good coverage compared to a larger panel?
This is a photo of the card panel (top left) I made a little too much epoxy.
So I panicked and grabbed the square wood panel and the low grade eps panel and gave them a bit of a coat too.
The other is my 6x9 inch 1mm veneer panel coated in pva.
The pva coating is much thinner , but this is my first attempt and I was rushing.
The epoxy is quite hard now on the wood and cardboard, but it still feels a little sticky and soft on the eps ?
Hopefully this will cure better with time ?
Steve
So I panicked and grabbed the square wood panel and the low grade eps panel and gave them a bit of a coat too.
The other is my 6x9 inch 1mm veneer panel coated in pva.
The pva coating is much thinner , but this is my first attempt and I was rushing.
The epoxy is quite hard now on the wood and cardboard, but it still feels a little sticky and soft on the eps ?
Hopefully this will cure better with time ?
Steve
Attachments
Leob.
tectonic do pretty well filling halls with just a pair of their panels ?
but with smaller panels there are some benefits, size obviously, maybe I shouldn't call them benefits ? It is more about presentation and scale.
in a normal music room a 6x9 inch panel can happily play along next to a 7ft panel at very realistic levels with no problems.
I do this sort of thing all the time when testing and comparing different panels.
They will both go loud enough to reach ,pain threshold !
With a decent low end driver that is.
I would roll both off at something like 100hz but roll the subs off at 300hz to deal with room suck outs.
But if filling a large hall I would go for the large panel .
But then you have got to be able to move it !!
Obviously if you do not have to move the panel and is in a fixed position there is no problem.
So you can understand why tectonic chose their size.
Steve.
tectonic do pretty well filling halls with just a pair of their panels ?
but with smaller panels there are some benefits, size obviously, maybe I shouldn't call them benefits ? It is more about presentation and scale.
in a normal music room a 6x9 inch panel can happily play along next to a 7ft panel at very realistic levels with no problems.
I do this sort of thing all the time when testing and comparing different panels.
They will both go loud enough to reach ,pain threshold !
With a decent low end driver that is.
I would roll both off at something like 100hz but roll the subs off at 300hz to deal with room suck outs.
But if filling a large hall I would go for the large panel .
But then you have got to be able to move it !!
Obviously if you do not have to move the panel and is in a fixed position there is no problem.
So you can understand why tectonic chose their size.
Steve.
Leob.
thanks for the link.
it all looks a bit like star trek to me.
Just dial in your panel.
Steve.
thanks for the link.
it all looks a bit like star trek to me.
Just dial in your panel.
Steve.
Steve,Eric .
Reduce the low end ?
I used weights on my panels to fill in the large dips in the response in the 100hz to 300hz , which it does well .
I thought everyone new this ?
You could also use the weights to extend the low end performance of small panels ,not reduce it .
I'm sure I talked about this over on NXT RUBBISH .
Steve.
It took me a while to figure out what you are saying here, but now I realize you misunderstood me. When I said, "reduce the low end" I meant reduce the frequency of the low end (i.e. extend the frequency range lower), not reduce the sound power of the low end.
I meant the former, you thought I meant the latter. But my other point was that I think weights would be better used to make subtle manipulations of the higher modes to eliminate peaks or fill in dips, rather than extend the low end. Simply extending the low end with weights might actually be more likely to create bigger dips at higher frequencies. But, this is speculation, since I have not really tried any of this.
But what I find most remarkable is that you think "everyone would know" about a particular experiment you did. I can barely recall even half of what I've done myself.
Eric
Last edited:
Eric.
extending is a much better description.
the weights have been mentioned many times by many people and in patents.
I am just one of many.
Steve.
extending is a much better description.
the weights have been mentioned many times by many people and in patents.
I am just one of many.
Steve.
Eric.
https://patents.google.com/patent/U...=priority:19610101&oq=inventor:+A+Cohen++1961
In this patent from way back in 1961 shows in figs 6 8 and 9 very clearly the effects of weights.
I love this patent, it is easy to read and understandable, he is obviously very interested in the sound.
More modern patents are more interested in the math , the sound does not seem to come into it ?
We do not know if the panels we design are any good until we attach the exciter and hear how the material sounds.
But after testing lots of different materials you get an idea of what works and what does not.
I only wish I could have re-found the patent with all the different panel shapes ,including the ear shape.
This also helped to minimise dips in the response.
Steve.
https://patents.google.com/patent/U...=priority:19610101&oq=inventor:+A+Cohen++1961
In this patent from way back in 1961 shows in figs 6 8 and 9 very clearly the effects of weights.
I love this patent, it is easy to read and understandable, he is obviously very interested in the sound.
More modern patents are more interested in the math , the sound does not seem to come into it ?
We do not know if the panels we design are any good until we attach the exciter and hear how the material sounds.
But after testing lots of different materials you get an idea of what works and what does not.
I only wish I could have re-found the patent with all the different panel shapes ,including the ear shape.
This also helped to minimise dips in the response.
Steve.
Yes, you have convinced me to not think in watts and SPL when comparing DML to a line array. I guess the claim Tectonic makes that 8 DML500 can replace 20 line array speakers might be slightly inflated, but I doubt it is completely off if that is what they are selling their customers, and they seem to be a serious business. 20 line arrays typically would be 20-30kw, which it lots considering that is excluding subs.Leob.
tectonic do pretty well filling halls with just a pair of their panels ?
but with smaller panels there are some benefits, size obviously, maybe I shouldn't call them benefits ? It is more about presentation and scale.
in a normal music room a 6x9 inch panel can happily play along next to a 7ft panel at very realistic levels with no problems.
I do this sort of thing all the time when testing and comparing different panels.
They will both go loud enough to reach ,pain threshold !
With a decent low end driver that is.
I would roll both off at something like 100hz but roll the subs off at 300hz to deal with room suck outs.
But if filling a large hall I would go for the large panel .
But then you have got to be able to move it !!
Obviously if you do not have to move the panel and is in a fixed position there is no problem.
So you can understand why tectonic chose their size.
Steve.
My thinking was that in a normal music room, the difference between 10w into a regular speaker, a 30cm or a 60cm panel might not be that different in terms of loudness. The DML will appear a bit louder off axis than a regular speaker, but when you are trying to fill a large space or throw sound long distance outdoors, the increased total mass of air being moved by the DML thanks to the large surface must be what makes it possible to replace 20000w with 2400w.
Would be really interesting to compare at say 10m distance and 45 degrees of axis with panels of different sizes and see if it affects the SPL values.
Leob.
tectonic use the word intelligibility a lot,which I think sums up dml very well.
it's not just that at a train station , with dml you can actually hear what the announcer is saying.
at a very loud rock concert for instance the sound can get very hard and distorted, your ears start to shut down and you start wincing, and it can all become a bit of a mush.
with dml this does not seem to happen ?
This does have a down side though.
I have come a cropper myself sometimes.
In the recordings I have posted on this site ,I go to great pains to point out that I am recording while playing my system very loud !!!
Not that you can tell when listening to the recordings ,they sound clean and clear but you have no idea of the volume .
Sometimes after long periods of listenig, I turn the volume up to listen to some quiet music, and forget to turn down the volume, and this can happen a few times.
before I know it I'm listening at very loud volume ,but it sounds so clean and clear that I don't realise ,that is until I see the volume control job !! Or when my wife comes in and says , I could hear you down the end of the road, TURN IT DOWN !!!
That is my impression of the difference I have noticed between dml and normal speakers.
In my room anyway, my TLS, could not do this without showing signs of compression and distress.
Steve.
tectonic use the word intelligibility a lot,which I think sums up dml very well.
it's not just that at a train station , with dml you can actually hear what the announcer is saying.
at a very loud rock concert for instance the sound can get very hard and distorted, your ears start to shut down and you start wincing, and it can all become a bit of a mush.
with dml this does not seem to happen ?
This does have a down side though.
I have come a cropper myself sometimes.
In the recordings I have posted on this site ,I go to great pains to point out that I am recording while playing my system very loud !!!
Not that you can tell when listening to the recordings ,they sound clean and clear but you have no idea of the volume .
Sometimes after long periods of listenig, I turn the volume up to listen to some quiet music, and forget to turn down the volume, and this can happen a few times.
before I know it I'm listening at very loud volume ,but it sounds so clean and clear that I don't realise ,that is until I see the volume control job !! Or when my wife comes in and says , I could hear you down the end of the road, TURN IT DOWN !!!
That is my impression of the difference I have noticed between dml and normal speakers.
In my room anyway, my TLS, could not do this without showing signs of compression and distress.
Steve.
Eric,
When you evaluate the possible Fc, how do you get or infer the bending stiffness? Your experience of composite? In a quick look to the web site, I haven't seen information except thickness and mass.
... composites are strange things to me currently!
Christian
Christian,
Loeb's link included the following quite comprehensive details, which are enough to determine the Bending stiffness.
But one thing you may not have realized is that the carbon skin thickness can be determined from:
t=prepreg wt/prepreg density = .445/1560=.00028m = 0.28 mm.
Note, they made a mistake and wrote 1.56 g/m2 instead or 1.56g/cm2 or 1560 kg/m3 for the prepreg density.
Also, I don't know why they list the Tensile moduli twice. Once as 62 GPa (0 deg) and 60 GPa (90 deg) and then again as 70 GPa (0 deg) and 65 GPa (90 deg). Maybe they represent two different levels of curing? I don't know. But pick any number between 60 and 70 GPa, the result won't be much different.
So use:
Skins:
t=0.28 mm
E= 60 or 62 or 65 or 70 GPa
rho=1560 kg/m3
Core:
t=5 mm
E=0 ( not quite true but close enough)
rho=32 kg/m3
That should be all you need. Let me know if it's not.
The only caveat, as I mentioned before, is that the panel wts they report imply an areal weight of about 1.2 kg/m2, when it "should" be only about 1.0 kg/m3. I don't know if the difference is glue they add to attach the skins to the core, or if their reported "wt approx" is an overestimate, or a little of both.
Interestingly, they also report the shear modulus of the honeycomb in the spec sheet. I don't usually see that on spec sheets for cores. I could add the Heron shear criteria to my calculations, perhaps I should.
Eric
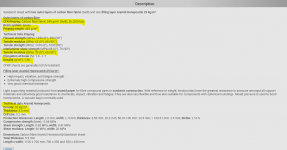
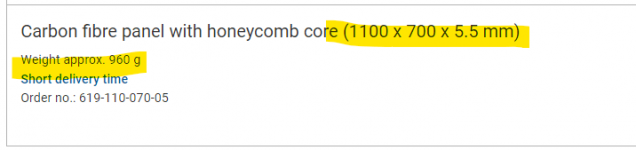
You are right Eric. In another document, the speed of the shear wave is v=(G/rho)^0.5. The goal is to get it greater than c the sound speed. In order of magnitude, with the data we have from materials :That first article must be a good one, as it's written by a Penn State professor. I did my graduate research in the same lab (but not in Acoustics!).
I agree the effect of the core shear modulus may very well be something that's underappreciated. I do recall this patent family well, as it's the first place I ever saw the B/mu3 criteria.
But check the math, I think there's a typo in the equation. If you read the sentence above it, I think it says somthing different from the "re-arranged" equation.
That is, the words say, effectively: G>(uc^2)/d, right? which correctly rearranges to (Gd/uc^2)>1 , right?
But they wrote (uc^2/dG)>1, which is exactly opposite. Or am I mistaken?
Strangely enough, they buggered up the same equation in the US version of the patent, but in a different way!
Eric
- EPS 15kg/m³ 350m/s not much above c
- XPS 30kg/m³ 430m/s
- Acrylic 960m/s
- Plywood 2500m/s
I don't remember if I have already posted the link to this document : Tutorial on the Vibroacoustics of Composite Sandwich Panels where there is the same things for sandwich. Then in this case v=(Gcore.hcore/rho_skin/hskin)^0.5 and about 2500m/s for the CF/balsa. Similar to the plywood.
Christian
Thank you Eric. I have to dig a little and get new knowledge. ChristianChristian,
Loeb's link included the following quite comprehensive details, which are enough to determine the Bending stiffness.
But one thing you may not have realized is that the carbon skin thickness can be determined from:
t=prepreg wt/prepreg density = .445/1560=.00028m = 0.28 mm.
Note, they made a mistake and wrote 1.56 g/m2 instead or 1.56g/cm2 or 1560 kg/m3 for the prepreg density.
Also, I don't know why they list the Tensile moduli twice. Once as 62 GPa (0 deg) and 60 GPa (90 deg) and then again as 70 GPa (0 deg) and 65 GPa (90 deg). Maybe they represent two different levels of curing? I don't know. But pick any number between 60 and 70 GPa, the result won't be much different.
So use:
Skins:
t=0.28 mm
E= 60 or 62 or 65 or 70 GPa
rho=1560 kg/m3
Core:
t=5 mm
E=0 ( not quite true but close enough)
rho=32 kg/m3
That should be all you need. Let me know if it's not.
The only caveat, as I mentioned before, is that the panel wts they report imply an areal weight of about 1.2 kg/m2, when it "should" be only about 1.0 kg/m3. I don't know if the difference is glue they add to attach the skins to the core, or if their reported "wt approx" is an overestimate, or a little of both.
Interestingly, they also report the shear modulus of the honeycomb in the spec sheet. I don't usually see that on spec sheets for cores. I could add the Heron shear criteria to my calculations, perhaps I should.
Eric
View attachment 1023688View attachment 1023706
Leob.
I've just watched this video ,which is very informative,and discusses many of the topics we have been discussing.
If you want to understand dml ,bmr, and cone drivers ,and a little history of dml ,it's a step in the right direction.
This should clear up a lot of your questions.
Steve.
I've just watched this video ,which is very informative,and discusses many of the topics we have been discussing.
If you want to understand dml ,bmr, and cone drivers ,and a little history of dml ,it's a step in the right direction.
This should clear up a lot of your questions.
Steve.
After testing the printed panel a bit more carefully, it is pretty dead above 3-4k.
I was mostly worried about the bass due to the small size, but I guess the material just has the wrong properties. It is of course nowhere near as stiff as plywood or PC/Acrylic, which I guess is the problem. I'm trying to print a plate with thinner surface and using PETG instead of PLA+, but expecting it to be quite similar. Stiffness will not be very different, and I'm guessing modifying thickness or density will not really help much either.
While most thermoplastics used in 3d printing is in the same ballpark when it comes to material specs, there are some specialized materials that claim to improve for example stiffness. The cheap PLA+ I'm using doesn't have specs, but I have PETG and BioFusion from extrudr, and they have specs on their website.
Looking at the specs for BioFusion its tensile modulus is 3200 MPa and their PETG is 3100 MPa. The stiffest I found with reasonable price and that is easily printable is nanodiamond filament which claims 6800 MPa: https://carbodeon.com/product/udiamond/
A bit trickier to print perhaps, but CA-PAHP claims 25GPa: https://treedfilaments.com/3d-printing-filaments/pahp-carbon-3d-printing-filament/
Thinking if I will give the latter a go, it seems to have quite radically different properties than your typical filament at least. And with my level of understanding in material science, shooting blindly in different directions and see what sticks seems like a good strategy 🙂
I was mostly worried about the bass due to the small size, but I guess the material just has the wrong properties. It is of course nowhere near as stiff as plywood or PC/Acrylic, which I guess is the problem. I'm trying to print a plate with thinner surface and using PETG instead of PLA+, but expecting it to be quite similar. Stiffness will not be very different, and I'm guessing modifying thickness or density will not really help much either.
While most thermoplastics used in 3d printing is in the same ballpark when it comes to material specs, there are some specialized materials that claim to improve for example stiffness. The cheap PLA+ I'm using doesn't have specs, but I have PETG and BioFusion from extrudr, and they have specs on their website.
Looking at the specs for BioFusion its tensile modulus is 3200 MPa and their PETG is 3100 MPa. The stiffest I found with reasonable price and that is easily printable is nanodiamond filament which claims 6800 MPa: https://carbodeon.com/product/udiamond/
A bit trickier to print perhaps, but CA-PAHP claims 25GPa: https://treedfilaments.com/3d-printing-filaments/pahp-carbon-3d-printing-filament/
Thinking if I will give the latter a go, it seems to have quite radically different properties than your typical filament at least. And with my level of understanding in material science, shooting blindly in different directions and see what sticks seems like a good strategy 🙂
I found the panel that suffered from the high output from the side on post 2315 on page 116.
I'd already taken measurements so did not take anymore.
it shows the peak at about 10k in picture 3,,but at the same time the panel is rolling off and reducing volume lower down.
I did this time measure from the top and bottom of the panel, and the 10k peak was reduced and the low end roll off was not so reduced, it was more of a gentle spread out hump ?
So I'm wondering if it is the width of the panel that is causing the problem , as the top and bottom measurements are not so harsh.?
also as luck would have it , above this post on post 2309 and 2310 there is a low grade eps panel with 3 weights (batteries) attached to fill in the response between 100hz and 300hz, that was only in Sept 2020 .
It worked well in this instance.
Nobody said why are you sticking batteries on your panels ?
Steve.
I'd already taken measurements so did not take anymore.
it shows the peak at about 10k in picture 3,,but at the same time the panel is rolling off and reducing volume lower down.
I did this time measure from the top and bottom of the panel, and the 10k peak was reduced and the low end roll off was not so reduced, it was more of a gentle spread out hump ?
So I'm wondering if it is the width of the panel that is causing the problem , as the top and bottom measurements are not so harsh.?
also as luck would have it , above this post on post 2309 and 2310 there is a low grade eps panel with 3 weights (batteries) attached to fill in the response between 100hz and 300hz, that was only in Sept 2020 .
It worked well in this instance.
Nobody said why are you sticking batteries on your panels ?
Steve.
PP is available as filament, but is very hard to print. I think PP is a bit more flexible than PLA, but not sure...they are probably in the same ballpark I would say.
Very interesting...didn't know the history behind NXT and that it basically arrived from aviation composite materials.Leob.
I've just watched this video ,which is very informative,and discusses many of the topics we have been discussing.
If you want to understand dml ,bmr, and cone drivers ,and a little history of dml ,it's a step in the right direction.
This should clear up a lot of your questions.
Steve.
Still have a lot of unclear questions though, so gonna have to keep picking your brains 🙂
Leob.
also on page 116 there are 2 recordings (yellow,Rammstein do hast ) using a couple of ropey test panels with photos.
If you listen to these recording ,and others, with the volume turned up as loud as you can stand , you will get an idea of how loud I was listening to them with no compression !
it is very difficult when recording at this loud a volume, you find yourself jumping up and down to the music, even at my age 😄
Steve.
also on page 116 there are 2 recordings (yellow,Rammstein do hast ) using a couple of ropey test panels with photos.
If you listen to these recording ,and others, with the volume turned up as loud as you can stand , you will get an idea of how loud I was listening to them with no compression !
it is very difficult when recording at this loud a volume, you find yourself jumping up and down to the music, even at my age 😄
Steve.
- Home
- Loudspeakers
- Full Range
- A Study of DMLs as a Full Range Speaker