No post cure. I experiment with epoxy resin flexibilizer to to adjust Tg even lower. Have you tried that?Hey Lenta,
Do you do a 60 C post cure to get the highest Tg?
Eric
I've been working with my damping test unit, that is, what Christian calls my "anti-zylophone", trying to figure out the best way to conduct the tests.
Originally, I was using the "tapping" method. But over the past few days I've been trying some new things. One is a video method. That is, I just deflect the center of the bar with my fingertip, then let it free, and record what happens with the slo-motion feature of my phone camera. I was hoping to post some videos, but it seems I can't post a .mov file. Anyway, the slo-mo video gives a good idea of how long or short the vibrations continue, gives a decent indication of how good the material is.
But the method I like best (as of today anyway) is to mount an exciter close to one end of the beam (about 50 mm) and locate my microphone the same distance from the other end.
.
Then I run a frequency sweep in REW and look at the peaks generated. The first image below is the result when the test beam is mounted to the frame using my "favorite" example of poor damping, 3M Indoor mounting tape. Note that there are sharp peaks in the response across virtually the entire frequency range. Each of the peaks occurs at one of the resonance frequencies of the beam. In fact, the first peak is actually not the fundamental, but rather the second natural frequency. The fundamental is at about 30 Hz, but is not really excited by the exciter, since it's located close to the end of the beam.
The second image is using a butyl rubber window glazing to mount the beam. The butyl rubber appears to provide better damping at low and high frequencies, but around 1k to 2k is no better than the 3M Indoor.
The overlay below shows a comparison of a bunch of different mounting tapes/foams I tried today. Above about 5 kHz, the results are similar for all the mounting materials. But below that, they vary greatly, with each better in some region, and worse in others. Interestingly, Sorbothane 30 Duro is pretty good above 1 kHz, but not much better than the 3M Indoor below that.
Based on these results, it looks like the EPDM foam might be the best thing I have to provide decent damping over the entire frequency range. I will be interested to try other materials (Poron?) whenever I find something new. Meanwhile, I've started looking combinations of materials along the perimeter, rather than just one, to take advantage of each material's strength.
Eric
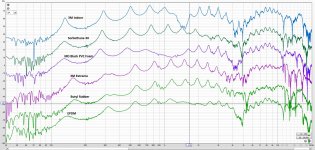
Originally, I was using the "tapping" method. But over the past few days I've been trying some new things. One is a video method. That is, I just deflect the center of the bar with my fingertip, then let it free, and record what happens with the slo-motion feature of my phone camera. I was hoping to post some videos, but it seems I can't post a .mov file. Anyway, the slo-mo video gives a good idea of how long or short the vibrations continue, gives a decent indication of how good the material is.
But the method I like best (as of today anyway) is to mount an exciter close to one end of the beam (about 50 mm) and locate my microphone the same distance from the other end.
.
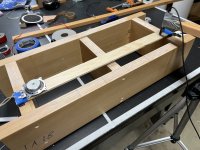
Then I run a frequency sweep in REW and look at the peaks generated. The first image below is the result when the test beam is mounted to the frame using my "favorite" example of poor damping, 3M Indoor mounting tape. Note that there are sharp peaks in the response across virtually the entire frequency range. Each of the peaks occurs at one of the resonance frequencies of the beam. In fact, the first peak is actually not the fundamental, but rather the second natural frequency. The fundamental is at about 30 Hz, but is not really excited by the exciter, since it's located close to the end of the beam.
The second image is using a butyl rubber window glazing to mount the beam. The butyl rubber appears to provide better damping at low and high frequencies, but around 1k to 2k is no better than the 3M Indoor.

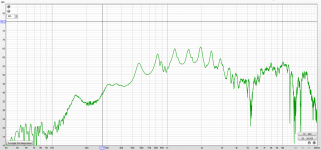
The overlay below shows a comparison of a bunch of different mounting tapes/foams I tried today. Above about 5 kHz, the results are similar for all the mounting materials. But below that, they vary greatly, with each better in some region, and worse in others. Interestingly, Sorbothane 30 Duro is pretty good above 1 kHz, but not much better than the 3M Indoor below that.
Based on these results, it looks like the EPDM foam might be the best thing I have to provide decent damping over the entire frequency range. I will be interested to try other materials (Poron?) whenever I find something new. Meanwhile, I've started looking combinations of materials along the perimeter, rather than just one, to take advantage of each material's strength.
Eric
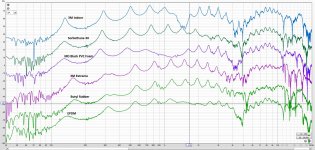
Lenta,No post cure. I experiment with epoxy resin flexibilizer to to adjust Tg even lower. Have you tried that?
No, I have not tried that. Actually, I didn't know that there was such a thing as flexibilizer! I did have the idea to try adjusting the hardener level in order to get a lower Tg, but have yet to actually try it. I'm not sure if it's a good idea or not, but it seems like lowering the Tg is a very interesting way to build damping directly into the panel, instead of trying to do everything at the boundaries. But I've never heard of anyone else taking this approach (before today).
I will look up flexibilizers, but I would be interested to know anything you can share about flexibilizers. Any idea what Tg you are reaching?
Eric
Just excellent!I've been working with my damping test unit, that is, what Christian calls my "anti-zylophone", trying to figure out the best way to conduct the tests.
Bravo Eric!
Thanks Christian!Just excellent!
Balsa I have tried so far is 6.5mm thick, tried to keep it as flexible as possible. I have tried to add 10 %, 20% of flexibilizer and epoxy cured hard, but viscoelastic. 50% mix I made with ultra fast curing epoxy to pre seal balsa pores. Have not done measurements, but with 50% mix it was too soft, rubbery state wich still probably works as cld between balsa and CF skins.Lenta,
No, I have not tried that. Actually, I didn't know that there was such a thing as flexibilizer! I did have the idea to try adjusting the hardener level in order to get a lower Tg, but have yet to actually try it. I'm not sure if it's a good idea or not, but it seems like lowering the Tg is a very interesting way to build damping directly into the panel, instead of trying to do everything at the boundaries. But I've never heard of anyone else taking this approach (before today).
I will look up flexibilizers, but I would be interested to know anything you can share about flexibilizers. Any idea what Tg you are reaching?
Eric
https://www.r-g.de/en/art/130140
Thanks Lenta,
I just called West Systems, but they don't have a flexibilizer for their system. I did find another epoxy supplier (local) that does, but I've never used their epoxy before. Maybe I'll give it a try, though. If you do any measurements comparing panels with and without flexibilizer, I would be very interested in the results.
Wow, 6.5 mm balsa! That must be a really stiff panel. With CF skins I am only using 1.6 mm balsa.
Eric
I just called West Systems, but they don't have a flexibilizer for their system. I did find another epoxy supplier (local) that does, but I've never used their epoxy before. Maybe I'll give it a try, though. If you do any measurements comparing panels with and without flexibilizer, I would be very interested in the results.
Wow, 6.5 mm balsa! That must be a really stiff panel. With CF skins I am only using 1.6 mm balsa.
Eric
I only just discovered this thread! I have not been visiting the main forum, so missed the launch announcement. Anyway, I found it because I was about to ask Eric & Christian about their mounting techniques on the impulse technique forum, and first did a search. I wonder how many more threads there are I'm oblivious of.
Im about half way through, some ideas that might be profitable to think about which have not (I think) been discussed yet.
Im about half way through, some ideas that might be profitable to think about which have not (I think) been discussed yet.
- Constrained layer damping. Im thinking of using layers of the same material (in my case HD EPS) with a viscoelastic material between (eg butyl mastic). Not sure how to keep them together though, unless I recessed the multiple edge layers into the frame.
- Viscous damping - extend the panel edges into a recess in the frame, and surround with a fluid (would have to be inside a plastic pouch.
- Eddy current damping. Strips of conductive material along the edge beside strong magnets.
Hello Paul,I wonder how many more threads there are I'm oblivious of.
The threads I follow at the moment :
- the main DML thread : A Study of DMLs as a Full Range Speaker
- the impulse one : Application of Impulse Excitation for DML Design and Analysis
- the exciter building : DML Exciter Design
You have the full set.
Christian
Welcome to the thread Paul, appreciate your input as always.I only just discovered this thread!
I have been thinking about CLD too. But I'm thinking of that as more of an option for damping the panel itself, rather than the boundary.
For fun I made a tiny panel a few weeks ago with wood veneer skins and my 3M Extreme mounting tape (mostly butyl rubber I suspect) as the core. The result was not impressive by any means, but it was really a silly attempt. I intend to make some more serious attempts soon.
Eric
I suspect that some sort of gel would provide for maximum damping. Soft yet massive, and intimate contact with the panel and frame can be ensured, conducting away vibrations & converting to heat.
Perhaps a strong mix of plain beef gelatin would work well, as long as it does not degrade. Thinking of the ballistic gelatin that myth busters are so fond of.
Perhaps a strong mix of plain beef gelatin would work well, as long as it does not degrade. Thinking of the ballistic gelatin that myth busters are so fond of.
Eric, would you be able to try another material on your antixylophone?
Take a piece of sponge rubber (either the yellow open cell PU foam from kitchen sponges, or possibly better the fine textured white melamine foam). Saturate completely with water, place in a snap lock back, excluding all air, and use that as your damper.
A good way to exclude air and excess water is to almost close the bag, then dip the bag in a bucket of water as you let air out the top, and close bag.
Soft pvc disposable glove material would be better than polyethylene bags which crackle as they move, but I don’t know of any bag form of PVC.
Take a piece of sponge rubber (either the yellow open cell PU foam from kitchen sponges, or possibly better the fine textured white melamine foam). Saturate completely with water, place in a snap lock back, excluding all air, and use that as your damper.
A good way to exclude air and excess water is to almost close the bag, then dip the bag in a bucket of water as you let air out the top, and close bag.
Soft pvc disposable glove material would be better than polyethylene bags which crackle as they move, but I don’t know of any bag form of PVC.
I made some refinements to my anti-xylophone. I have a stiffer frame and added some constrained layer damping to it to keep the resonances in the frame from affecting the measurements. I also started using a smaller exciter, with only a 13 mm voice coil. I was thinking to call it my Silophone (as in SILent). Which name do you guys prefer?
Meanwhile I got some samples of Poron foam, too. Test results below are with the new frame and compare two grades of Poron with my two 3M mounting tapes and with EPDM foam.
In the image below, all are compared. I ordered them from worst to best from top to bottom.
The Porons are two versions of Poron "Shockseal" foam, which are touted for impact protection and which the Poron rep thought would have particularly good damping too. The two grades are 4790-79 and 4790-92. The 79 is quite a bit firmer than the 92.
As it turns out, both are pretty good, while the 92 seems best, and in fact is just a bit better than my EPDM foam, perhaps. The Poron 79 might actually be the best at low frequencies by a small margin, but the 92 is clearly better than the 79 above 700 Hz. The firmer Poron 79 also creates more constraint at the ends, which pushes all the natural frequencies a bit higher than the rest.
The second chart compares the two best, EPDM and Poron 92. The differences are small but Poron 92 damps a little better in the 1 kHz range. Interestingly, the EPDM seems particularly good at 2 kHz, but I'm not sure exactly what's happening there so I'm a bit suspicious of that.
I have some additional Poron samples coming. Other grades and thinner. I'm wondering if thinner foams might be better, as they should have greater strain and perhaps that will help. We will see.
Paul, I tried your foam/water suggestion. I'll share that in a separate post.
Eric
Meanwhile I got some samples of Poron foam, too. Test results below are with the new frame and compare two grades of Poron with my two 3M mounting tapes and with EPDM foam.
In the image below, all are compared. I ordered them from worst to best from top to bottom.
The Porons are two versions of Poron "Shockseal" foam, which are touted for impact protection and which the Poron rep thought would have particularly good damping too. The two grades are 4790-79 and 4790-92. The 79 is quite a bit firmer than the 92.
As it turns out, both are pretty good, while the 92 seems best, and in fact is just a bit better than my EPDM foam, perhaps. The Poron 79 might actually be the best at low frequencies by a small margin, but the 92 is clearly better than the 79 above 700 Hz. The firmer Poron 79 also creates more constraint at the ends, which pushes all the natural frequencies a bit higher than the rest.
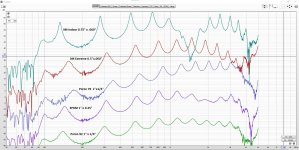
The second chart compares the two best, EPDM and Poron 92. The differences are small but Poron 92 damps a little better in the 1 kHz range. Interestingly, the EPDM seems particularly good at 2 kHz, but I'm not sure exactly what's happening there so I'm a bit suspicious of that.
I have some additional Poron samples coming. Other grades and thinner. I'm wondering if thinner foams might be better, as they should have greater strain and perhaps that will help. We will see.
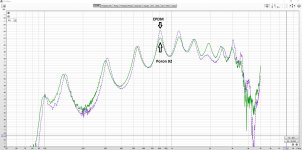
Paul, I tried your foam/water suggestion. I'll share that in a separate post.
Eric
@pway
Paul,
I tried your water/foam idea in the anti-xylophone. I was able to use ziplock bags just as you proposed, and seal them underwater to get all the air out.
Here's what it looked like.
And here's the result, compared to EPDM foam. Actually it seemed to work very well at low frequencies, but not as well at high frequencies. I wonder if it would work even better with a more viscous liquid, like oil. But I wasn't eager to get that messy!
Eric
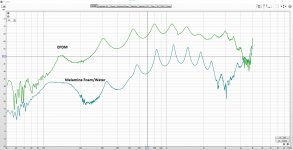
Paul,
I tried your water/foam idea in the anti-xylophone. I was able to use ziplock bags just as you proposed, and seal them underwater to get all the air out.
Here's what it looked like.
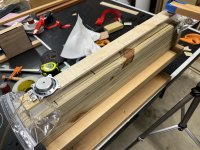
And here's the result, compared to EPDM foam. Actually it seemed to work very well at low frequencies, but not as well at high frequencies. I wonder if it would work even better with a more viscous liquid, like oil. But I wasn't eager to get that messy!
Eric
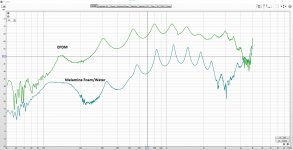
Thanks for doing that Eric.wonder if it would work even better with a more viscous liquid, like oil
I prepared one myself and was struck by how 'dead' it was if you whack or flick it. Your result is promising, I think.
I expect oil being less dense would be closer to the characteristic impedance of ply or EPS than water. Melamine is also quite stiff compared with soft polyurethane, but I guess that is a better match at HF. Regarding viscosity, I would reckon less viscous would be better, so energy is converted to heat with the fluid moving through the foam matrix.
I also expect that for this and the other materials, the damping effect will also depend upon the dimensions of the damping material. I guess you have anticipated this, as you marked the sizes on each test. Each will have its own resonant frequency at any particular size, and damping effect would be greatest at that freq I expect.
Regarding the name, FWIW, silophone sounds too similar, so the pun only works if it's written down. But either is fine. You could also call it the 'rod of silence' after a favourite comedy show from my youth 'Get Smart' (remember the cone of silence?).
What is the aim for damping? I think you would want maximum damping at low frequency, correct?
Last edited:
I would have suggest silentophone to keep the word silent in it. An other suggestion is Dampophone as the word xylophone is made from the greek xylo = wood and phon = sound. You are the inventor... your choice.I was thinking to call it my Silophone (as in SILent). Which name do you guys prefer?
Yeah, that's a great question. In my mind the ultimate goal might be to virtually eliminate modal behavior altogether, and have only the "pebble in the pond" waves, that everybody waxes on about in speaker literature. But whether or not that really is the holy grail is still an open question for me.What is the aim for damping? I think you would want maximum damping at low frequency, correct?
That said, I doubt there's any chance that edge damping alone would ever take us to that extreme. Probably the best we can really hope for with perimeter damping is to substantially reduce the duration of any ringing, and perhaps smooth the frequency response at the same time. When I look at spectrograms, ringing is of longest duration at the fundamental (typically about 100 Hz in my usual designs), and is rarely obvious above 1000 Hz. So, it seems to me that 100 to 1000 Hz is probably the region of most interest, with the emphasis on the lower end, as you are suggesting.
One tricky aspect is that the materials that seem to work best at the low end (e.g. butyl rubber, Poron 92) are stiffer materials, and tend to act more like clamped edges than simple supports. Of course that means that a bigger panel is necessary to have the same f3 at the low end. There's always tradeoffs.
Eric
- Home
- Loudspeakers
- Full Range
- Effect of Boundary Conditions on the Ringing of DML Speaker Panels