Hello,
What is the status of the DH-200C pc boards?
Thanks and regards,
Rob
Hi Rob,
Revised versions (hopefully final) are in final evaluation, and performance is quite good. Rick and I hope that they will be available soon. This development has taken us much longer than expected (as is often the case with these sorts of things), but we really want to get it right before others invest time and money in a build. This includes issues of documentation.
Thanks for your interest!
Cheers,
Bob
DH-200C
Once I secured a couple of DH-200 chassis to work with, I was able to get a better idea of the mechanics/assembly involved, actually be able to do one myself, find ways to make it as easy as possible to implement and document the build process.
Still need to verify the design with a +/-90V supply, for a DH-500 implementation, but the design seems to be working well in the DH-200/220 chassis.
A couple of pics of my prototypes in a DH-200 chassis.
Notice that we designed an addition OPS pcb in order to make that wiring easier and an upgrade to the output stage design to match Bob's prototype.
There will be a special OPS pcb needed for the DH-500 as well, it is in the works.
Enjoy
Rick
As Bob has mentioned, the design is progressing quite well.What is the status of the DH-200C pc boards?
Once I secured a couple of DH-200 chassis to work with, I was able to get a better idea of the mechanics/assembly involved, actually be able to do one myself, find ways to make it as easy as possible to implement and document the build process.
Still need to verify the design with a +/-90V supply, for a DH-500 implementation, but the design seems to be working well in the DH-200/220 chassis.
A couple of pics of my prototypes in a DH-200 chassis.
Notice that we designed an addition OPS pcb in order to make that wiring easier and an upgrade to the output stage design to match Bob's prototype.
There will be a special OPS pcb needed for the DH-500 as well, it is in the works.
Enjoy
Rick
Attachments
Last edited:
As Bob has mentioned, the design is progressing quite well.
Once I secured a couple of DH-200 chassis to work with, I was able to get a better idea of the mechanics/assembly involved, actually be able to do one myself, find ways to make it as easy as possible to implement and document the build process.
Still need to verify the design with a +/-90V supply, for a DH-500 implementation, but the design seems to be working well in the DH-200/220 chassis.
A couple of pics of my prototypes in a DH-200 chassis.
Notice that we designed an addition OPS pcb in order to make that wiring easier and an upgrade to the output stage design to match Bob's prototype.
There will be a special OPS pcb needed for the DH-500 as well, it is in the works.
Enjoy
Rick
Great pictures, Rick!
Cheers,
Bob
Question about XL-280
Since it's a little slow here lately I'm going to ask a quick quesiton about the XL-280: Can someone explain the function of a thermister between chassis and star ground? Shouldn't the signal ground have unhindered conduction to star ground?
In this case there is no earth ground connected to chassis--so what is the function of chassis ground?
I though it was desirable to have control over the path of the ground signal--it seems like connection to chassis defeats this purpose.
I understand chassis to earth for safety, but with no earth ground it doesn't make sense to me here.
Thanks
Ron
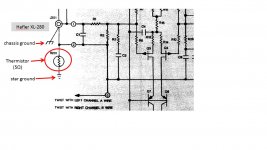
Since it's a little slow here lately I'm going to ask a quick quesiton about the XL-280: Can someone explain the function of a thermister between chassis and star ground? Shouldn't the signal ground have unhindered conduction to star ground?
In this case there is no earth ground connected to chassis--so what is the function of chassis ground?
I though it was desirable to have control over the path of the ground signal--it seems like connection to chassis defeats this purpose.
I understand chassis to earth for safety, but with no earth ground it doesn't make sense to me here.
Thanks
Ron
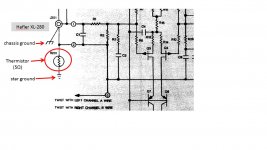
Last edited:
Since it's a little slow here lately I'm going to ask a quick quesiton about the XL-280: Can someone explain the function of a thermister between chassis and star ground? Shouldn't the signal ground have unhindered conduction to star ground?
View attachment 815844
I guess I wasn't thinking when I asked that 2nd question--of course the signal ground is connected directly to the ground plain on the board. But I still don't understand the use of chassis ground and the thermistor.
I guess I wasn't thinking when I asked that 2nd question--of course the signal ground is connected directly to the ground plain on the board. But I still don't understand the use of chassis ground and the thermistor.
It breaks the ground in a safe manner, it is a high resistance and inhibits ground loop currents when there is little current but allows fault currents, which are high (and therefore heat up the thermistor and reduce the resistance) to safely conduct to ground.
I like the new boards!
Must do something to refresh the 220 and XL280 I use, why refresh old boards when this will be available?
Speaking of which...will they be available generally, or is there restricted first quantities? Need I do anything now to be in a queue?
Must do something to refresh the 220 and XL280 I use, why refresh old boards when this will be available?
Speaking of which...will they be available generally, or is there restricted first quantities? Need I do anything now to be in a queue?
Hi Peter,
Thanks for your interest.
I do not see any restrictions for boards, once Bob gives the design his go ahead for release and I can stock ample supply for the demand. I was thinking that the supply of pcbs would also include the jfets too, so one only needs to order parts from a Mouser shopping cart link.
There will be no assembled/tested pcb's offered initially. Maybe this can be done at a later time, if resources and time allow.
As Bob responded to earlier, we are presently working on documentation. It is coming together very nicely, almost done.
The XL-280 will not be supported by this DH-220C design, nor will DH-500, P230.
Initially DH-200, DH-220, P220 will be supported, since those designs are very similar and we have units for evaluation. I have a DH-200 up and running continuously. Working on a 2nd one using Exicon mosfets.
Bob has both a DH-220 and a P230 for eval. So P230 will be supported, but not initially, since we need to design/test/eval a 3 pair OPS pcb.
DH-500, is on the to do list. We do not have one, so that poses a problem for evaluation. This one will also need a new OPS to support the 3 pairs of o/p devices, evaluate, test. Hopefully will be able to use the 3 pair OPS designed for the P230 in the DH-500 and not need yet another OPS pcb just for that model.
It maybe possible one could build without using the upgraded OPS pcb and just use the DH-220C amp front end (AFE), but this needs evaluation.
I see the XL-280 uses a PC-400 pcb, it has differences that need to be addressed. For one, it has the mono/stereo bridging switch included. The DH-220C AFE design does not support bridging in its current configuration. Also the PC-400 has a boosted supply for the AFE, rail fuses on the PC-400 pcb, where as the other models have rail fuses chassis mounted. There are no fuses on the DH-220C AFE.
Thanks for your interest.
I do not see any restrictions for boards, once Bob gives the design his go ahead for release and I can stock ample supply for the demand. I was thinking that the supply of pcbs would also include the jfets too, so one only needs to order parts from a Mouser shopping cart link.
There will be no assembled/tested pcb's offered initially. Maybe this can be done at a later time, if resources and time allow.
As Bob responded to earlier, we are presently working on documentation. It is coming together very nicely, almost done.
The XL-280 will not be supported by this DH-220C design, nor will DH-500, P230.
Initially DH-200, DH-220, P220 will be supported, since those designs are very similar and we have units for evaluation. I have a DH-200 up and running continuously. Working on a 2nd one using Exicon mosfets.
Bob has both a DH-220 and a P230 for eval. So P230 will be supported, but not initially, since we need to design/test/eval a 3 pair OPS pcb.
DH-500, is on the to do list. We do not have one, so that poses a problem for evaluation. This one will also need a new OPS to support the 3 pairs of o/p devices, evaluate, test. Hopefully will be able to use the 3 pair OPS designed for the P230 in the DH-500 and not need yet another OPS pcb just for that model.
It maybe possible one could build without using the upgraded OPS pcb and just use the DH-220C amp front end (AFE), but this needs evaluation.
I see the XL-280 uses a PC-400 pcb, it has differences that need to be addressed. For one, it has the mono/stereo bridging switch included. The DH-220C AFE design does not support bridging in its current configuration. Also the PC-400 has a boosted supply for the AFE, rail fuses on the PC-400 pcb, where as the other models have rail fuses chassis mounted. There are no fuses on the DH-220C AFE.
Last edited:
A couple of pics of my prototypes in a DH-200 chassis.
Notice that we designed an addition OPS pcb in order to make that wiring easier and an upgrade to the output stage design to match Bob's prototype.
There will be a special OPS pcb needed for the DH-500 as well, it is in the works.
Enjoy
Rick
Rick, What will be the constraints on the distance between the IPS/VAS board and the OPS board? I ask because I'm considering the feasibility of adapting these boards to a 5-channel amp chassis, but using only 3 boards so as to improve heat dissipation per board. But some flexibility in placing the boards would likely be required.
Ron
I'm very curious what your thoughts will be on the sonic comparison between the Exicon and the stock Mosfets.I have a DH-200 up and running continuously. Working on a 2nd one using Exicon mosfets.
I have a P500 which I'd be happy to lend you for the testing. One of the boards is blown, but other than that it seems to be in order. It has a heftier transformer than the DH-500, and a balanced input stage (which can be bypassed), but other than that I believe it is identical to the DH-500. At least with respect to the mounting of the board on the heat sink it is definitely identical.DH-500, is on the to do list. We do not have one, so that poses a problem for evaluation. This one will also need a new OPS to support the 3 pairs of o/p devices, evaluate, test. Hopefully will be able to use the 3 pair OPS designed for the P230 in the DH-500 and not need yet another OPS pcb just for that model.
I also have a DH-500 which wasn't fully working before I took it apart, but I think it could probably work for your evaluation needs...and I have an XL-280 I could lend which is a fully working stock version.
I imagine most people doing a mod like this would be OK to loose the bridging capability in exchange for really nice sounding stereo capability, but perhaps I'm wrong about this.I see the XL-280 uses a PC-400 pcb, it has differences that need to be addressed. For one, it has the mono/stereo bridging switch included. The DH-220C AFE design does not support bridging in its current configuration.
Ron
Last edited:
It breaks the ground in a safe manner, it is a high resistance and inhibits ground loop currents when there is little current but allows fault currents, which are high (and therefore heat up the thermistor and reduce the resistance) to safely conduct to ground.
OK, thanks for the reply. So it is identical in function to a parallel diode/resistor/diode arrangement, but it seems in both cases makes much more sense if chassis is connected to earth ground, (which it isn't in the XL-280).
OK, thanks for the reply. So it is identical in function to a parallel diode/resistor/diode arrangement, but it seems in both cases makes much more sense if chassis is connected to earth ground, (which it isn't in the XL-280).
In the best builds, no signal returns (signal grounds) or power supply grounds are on the chassis. The chassis acts only as a safety ground for AC and DC currents to earth via the AC connector. Hence, when the AC comes into the chassis, the ground wire should be immediately bonded to the chassis, and tthe central ground for PS and signal (star ground) is connected via the ground loop breaker to that chassis ground. Thus, all single inputs and output jacks and some potentiometers whose cases are grounded, must be isolated via insulating washers from the chassis.
Grounding is truly difficult.
I do not know. Something that would need to be tested. What distances are you anticipating?What will be the constraints on the distance between the IPS/VAS board and the OPS board?
I find it hard to imagine that the Exicon mosfets would sound any better or different than the Hitachi's. I will do some measurements to see if that would uncover any differences. The Exicon's have a slight higher dissipation rating than the stock Hitachi devices.I'm very curious what your thoughts will be on the sonic comparison between the Exicon and the stock Mosfets.
A P500 too, oh boy, one more to add to the list.
Thanks for the offers, let me work on getting what we will support at this time out the door and then move on to the other models.
Rick
This then answers my next question: shouldn't the decoupling caps on the OPS of these Hafler amps be grounded to the ground plain instead of to chassis? Or is it OK to do it this way for some reason?In the best builds, no signal returns (signal grounds) or power supply grounds are on the chassis. The chassis acts only as a safety ground for AC and DC currents to earth via the AC connector. Hence, when the AC comes into the chassis, the ground wire should be immediately bonded to the chassis, and tthe central ground for PS and signal (star ground) is connected via the ground loop breaker to that chassis ground. Thus, all single inputs and output jacks and some potentiometers whose cases are grounded, must be isolated via insulating washers from the chassis.
Grounding is truly difficult.
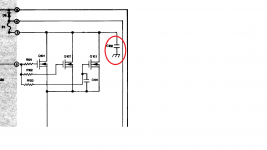
Not sure as of yet--I guess I mean something like 5" separation instead of the 1" you show in your photos.I do not know. Something that would need to be tested. What distances are you anticipating?
People have said they sound a little "better". I have some I want to try in an otherwise equivalent amp so that I can try side by side.I find it hard to imagine that the Exicon mosfets would sound any better or different than the Hitachi's. I will do some measurements to see if that would uncover any differences. The Exicon's have a slight higher dissipation rating than the stock Hitachi devices.
Keep me posted.A P500 too, oh boy, one more to add to the list.
Thanks for the offers, let me work on getting what we will support at this time out the door and then move on to the other models.
Rick
This then answers my next question: shouldn't the decoupling caps on the OPS of these Hafler amps be grounded to the ground plain instead of to chassis? Or is it OK to do it this way for some reason?
View attachment 816788
You have to stick to a selected grounding scheme. The Hafler as designed and constructed used the chassis as part of the grounding scheme. It thus mixed signal and chassis ground. Thus, unless you are going to completely rewire the amp, you have to keep the decoupling caps grounded to chassis.
What this means is that the typical position for the ground loop breaker is not going to work. You have to put it between the ground wire where it comes out of the AC wire, and the chassis ground. That may violate some legal requirements and may not be safe because if the ground loop goes open on a fault, then there is no safety ground AT ALL.
I guess the bottom line is, unless you are going through the trouble of rewiring the entire amp and carefully segregating signal and PS grounds from safety/chassis grounds, the ground loop breaker may not be a good thing to use. Instead, if you need to break a verified ground loop, use a high quality line input transformer like those from Jensen or Cinemag.
IMO, of course.
I'm planning to buy two boards for one of my DH200 amps. please post a link to a purchasing site when available.
if you need help proof reading the documentation, please let me know. I do a lot of this and understand keeping the sentence structure simple for a global market. The more complex the problem, the more simple the documentation needs to be in my experience.
if you need help proof reading the documentation, please let me know. I do a lot of this and understand keeping the sentence structure simple for a global market. The more complex the problem, the more simple the documentation needs to be in my experience.
So here's what I have, a 5-channel AT 1505 in like-new condition. But a standard Hafler 200/220 sounds better than this, which is why I have been trying to sell it. But given that the Hafler boxes are not the most beautiful things in the world, and given that I don't necessarily want to deal with 4 of them to power my 7.1 system, it would be nice to drop in the new Cordell boards into this chassis. Having opened it up I see that there are 2-boards per channel--the rectifier + caps + front end on one board, and the OPS on the second board. The distance between the surface of the heat sink and the fins of the adjacent heat sink is ~1.6", except on the sides where the distance between the heat sink surface and the side of the chassis is ~1.4". What is the minimum width required for the two Cordell boards? I can see they are using more than 1.6" in the photos, but I guess in their current context it's determined by the shape of the heat sink.I do not know. Something that would need to be tested. What distances are you anticipating?
Rick
1 idea is to remove 2 of the channels and use the remaining space for 3 channels + improved PSU (larger caps with LT4320 rectification).
Alternatively I could keep all 5 channels with the new boards but put the PSU in a separate chassis.
The toroid transformer has 10 x dual-wire secondaries with 50 VAC each. The current setup has +/- 65VDC rails x 5 channels. This is pretty close to a DH-220 in terms of power.
Does it seem like a good idea? Am I missing something obvious?
If I were to buy a chassis with the heat sinks, and a similar transformer it would probably cost me more than I can get for the 1505.
Ron
Attachments
- Home
- Amplifiers
- Solid State
- Hafler DH-200/220 Mods