Wesayso, it is good to see these pictures again. You are truly a madman! I'm reminded of Dr. Brown from Back to the Future 🙂
The theory goes that if you have a heavier mass, you need heavier damping. It's the classic spring-mass-damping system. You need less damping for lighter mass. That's why the BBC recommends thin walls. This approach has intrigued me as well. Imagine what you would do to damp a vibrating washing machine. Will you make the metal thicker or damp it using a constrained layer? I would damp it using a constrained layer. Of course, I am too lazy to build a constrained layer speaker. I just pretend the coloration does not exist 🙂
The thin walled enclosure theory is cute, but didn't do it for me. I can't help but think it will colour the sound in the bass department. Well damped rigid enclosure walls did make more sense to me. I also have a damped baffle construction etc. It worked for me.
The theory goes that if you have a heavier mass, you need heavier damping. It's the classic spring-mass-damping system. You need less damping for lighter mass. That's why the BBC recommends thin walls. This approach has intrigued me as well. Imagine what you would do to damp a vibrating washing machine. Will you make the metal thicker or damp it using a constrained layer? I would damp it using a constrained layer. Of course, I am too lazy to build a constrained layer speaker. I just pretend the coloration does not exist 🙂
Can you elaborate on "constrained layer"? Regarding damping, are you referring to damping material (stuffing) in the cabinet?
I know the theory, makes me wonder though, what a washing machine designed by Magico would look like 😱 What would it weigh?
The BBC speakers were designed with a purpose in mind, from what I've read they worked quite satisfactory... I've never had the pleasure to hear a set.
So how are your arrays holding up? Still enjoying them I suppose?
Constrained layer damping is using 2 rigid materials with a flexible layer in between, sort of like this:
It's common practice in Car Audio to use constrained layer technique to damp the outer sheet metal of doors with damping matt made from butyl with an aluminium layer on top.
For thicker materials you'd need a bigger flexible layer between two more rigid outer shells...
In a way my front baffle, made of 2 aluminium pieces with butyl rope pressed in between is a constrained layer construction, weighed down even further by a layer of mass loaded vinyl on the back side of the inner baffle, with neoprene behind that to seal against the enclosure.
Reading all this and seeing my journey again I can only conclude, yeah, I am a madman
The BBC speakers were designed with a purpose in mind, from what I've read they worked quite satisfactory... I've never had the pleasure to hear a set.
So how are your arrays holding up? Still enjoying them I suppose?
Constrained layer damping is using 2 rigid materials with a flexible layer in between, sort of like this:
It's common practice in Car Audio to use constrained layer technique to damp the outer sheet metal of doors with damping matt made from butyl with an aluminium layer on top.
For thicker materials you'd need a bigger flexible layer between two more rigid outer shells...
In a way my front baffle, made of 2 aluminium pieces with butyl rope pressed in between is a constrained layer construction, weighed down even further by a layer of mass loaded vinyl on the back side of the inner baffle, with neoprene behind that to seal against the enclosure.
Reading all this and seeing my journey again I can only conclude, yeah, I am a madman
Attachments
Last edited:
Wow, I came here to edit my post and there are already a couple of posts.
In your design, the damped front baffle should absorb all the energy. David Smith seemed to think that constrained layer was the right approach. I want to try it someday and see how it works myself.
My arrays are holding up fine. There is a resonance somewhere in the midrange, which I can feel on my fingers when sweeping the frequency response. It doesn't show up as a squiggle on the impedance plot. And I don't hear it when the music is on. I'm not too worried about it. I just enjoy them too much. I still need to do Pano's shuffler experiments. Just not enough time in the day.
Recently, a friend loaned me the Stax SR5 headphones. Quite wonderful sounding. Compared to other speakers, they would be world class, but compared to the arrays, I can find some flaws. We are spoiled 🙂
I really want to build synergies next. That should be quite a treat.
In your design, the damped front baffle should absorb all the energy. David Smith seemed to think that constrained layer was the right approach. I want to try it someday and see how it works myself.
My arrays are holding up fine. There is a resonance somewhere in the midrange, which I can feel on my fingers when sweeping the frequency response. It doesn't show up as a squiggle on the impedance plot. And I don't hear it when the music is on. I'm not too worried about it. I just enjoy them too much. I still need to do Pano's shuffler experiments. Just not enough time in the day.
Recently, a friend loaned me the Stax SR5 headphones. Quite wonderful sounding. Compared to other speakers, they would be world class, but compared to the arrays, I can find some flaws. We are spoiled 🙂
I really want to build synergies next. That should be quite a treat.
Last edited:
@JR, constrained layer is basically a limp layer of mass constrained between two other layers. For example, mass loaded vinyl sandwiched between two thin sheets of plywood. Or a heavy sheet of rubber constrained between two thin sheets of plywood. Mass load vinyl is often used for soundproofing homes in the US. The key to the damping effect is that the constrained layer should be of comparable weight to the other layers (edit:actually, I'm not sure about that).
Last edited:
I still have a soft spot for synergies as well... I could never "sell" that idea to my girlfriend though, she doesn't like the look of horns and they would take up way more space than my huge towers, that still fit on a sheet of A4 paper 😀.
Would love to try them though, play with that... especially after playing with the impulse from bushmeister's "bookshelf" experiment...
Would love to try them though, play with that... especially after playing with the impulse from bushmeister's "bookshelf" experiment...
Yeah, this is a huge benefit of the arrays--small footprint. I'm not sure there is another topology that can produce this combination of volume and low distortion in this small a footprint. Too often, we audiophiles ignore the social aspect.
Wesayso, it is good to see these pictures again. You are truly a madman! I'm reminded of Dr. Brown from Back to the Future 🙂
When I think back listening to the arrays a long time ago (and still even more true today) I did think: this is kind of like a time machine, at my will I can be in the room with Jim Morrison especially on a song like "The Ghost Song".
I love that! Drifting away on the music makes it all worth it to me... What a fun hobby we have!
I can't understand a speaker at that price point using MDF... I'd expect something like Pantzerholz at that price point (lol)
Meh, let them, at that price point it's about the customer making a statement, ie "I have a lot of money" and they are just there to facilitate that statement. It's hard making money from low volume manufacturing and this is a good source for getting a good christmas bonus to everybody. Are they ripping him off? sure, but his prize is exclusivity, maybe unedifying but everybody is happy in the end.
I would think a high pressure grease such as a lithium grease would be superior to the light weight WD40 would be. Nice work, I know how hot those aluminum chips are though when flying off the end of the cutter, I assume that was what the fence was about. The plain guide pins is good as long as you aren't using a wooden template that would probably burn quickly and not be usable for very long.
I know many pooh pooh the use of mdf but you have to remember that you are trading some of the stiffness of the ply for the extra mass of the mdf. I think if you duplicated the enclosures that Ronald made here with mdf at the same thickness and with all the other factors such as a fiberglass shell you would be hard pressed to find a significant difference is sound transmission through the cabinet walls. For a simple box speaker then the birch ply could have an advantage but with careful engineering even in a simple box with the correct internal bracing you can get similar end results. Now take the mdf stack and use an epoxy/carbon fiber outer layer and perhaps it would be even stiffer than the birch ply and glass layer. Many ways in engineering to end up with the same end results, you just have to think your way through the differing material properties. At the same time the end result that Ronald achieved are excellent.
On another note (just had to share), REW added the possibility to use an external sweep with a timing reference added to the signal.
That means that Mac users can use JRiver, or any other audio app to play the file, and it is recorded on another computer to analyse and play with EQ / Convolution settings.
It's not as convenient as the WDM driver in JRiver, but at least, that gives an option to Mac users.
Thank you REW team!
That means that Mac users can use JRiver, or any other audio app to play the file, and it is recorded on another computer to analyse and play with EQ / Convolution settings.
It's not as convenient as the WDM driver in JRiver, but at least, that gives an option to Mac users.
Thank you REW team!
I know many pooh pooh the use of mdf but you have to remember that you are trading some of the stiffness of the ply for the extra mass of the mdf. I think if you duplicated the enclosures that Ronald made here with mdf at the same thickness and with all the other factors such as a fiberglass shell you would be hard pressed to find a significant difference is sound transmission through the cabinet walls. For a simple box speaker then the birch ply could have an advantage but with careful engineering even in a simple box with the correct internal bracing you can get similar end results. Now take the mdf stack and use an epoxy/carbon fiber outer layer and perhaps it would be even stiffer than the birch ply and glass layer. Many ways in engineering to end up with the same end results, you just have to think your way through the differing material properties. At the same time the end result that Ronald achieved are excellent.
I agree there's more than one solution for every problem, however MDF got on my dislike list after working with it a long time ago.
I mainly would say pooh pooh to MDF due to not liking the material properties... for me it feels like it's one step above cardboard. I've used it for a sub enclosure in my car and that only reminded me of why I dislike working with it so much.


For the tower project I wanted to create something durable and serviceable. I could not picture a role for MDF within those ideals.
A combination of MDF and Ply with a flexible layer in between to create a constrained solution would be hard to beat. Dissimilar materials can work well together like that.
One of my early plans was to use epoxy plus matt to create the outer shape of the enclosure but I figured I wanted more weight in the cabinet to offset the moving mass.
I actually liked working with the birch ply. I would choose to work with it again.
On another note (just had to share), REW added the possibility to use an external sweep with a timing reference added to the signal.
That means that Mac users can use JRiver, or any other audio app to play the file, and it is recorded on another computer to analyse and play with EQ / Convolution settings.
It's not as convenient as the WDM driver in JRiver, but at least, that gives an option to Mac users.
Thank you REW team!
That is good news!
Hey all here.
Been reading some (especially the construction section at first many pages)
I must say, that i admire the will you got whesayso! 🙂... completing such a big project, and the will to go on for years...
I see you are discussing the MDF vs. Ply. But none mention the HDF; HDF is a better compressed MDF plate, and i know for sure many laudspeaker manufactors here in Denmark have used this materiel (Audiovector etc...)... Also Troels Gravesen write about this materel, which he use a lot for example some of his baffles. / DIY Loudspeaker Projects Troels Gravesen normally HDF is called blackMDF btw.
I have myself a big intterest (at the moment😛), using a raspberry pi for a stream solution connected to my NAS, and logitech squeezebox server etc...
Anyway i saw that jriver has released a solution for the newest pi-3, and was wondering if anyone here tries that with all the functionality.
Just my inputs Regards from Jesper
Been reading some (especially the construction section at first many pages)
I must say, that i admire the will you got whesayso! 🙂... completing such a big project, and the will to go on for years...
I see you are discussing the MDF vs. Ply. But none mention the HDF; HDF is a better compressed MDF plate, and i know for sure many laudspeaker manufactors here in Denmark have used this materiel (Audiovector etc...)... Also Troels Gravesen write about this materel, which he use a lot for example some of his baffles. / DIY Loudspeaker Projects Troels Gravesen normally HDF is called blackMDF btw.
I have myself a big intterest (at the moment😛), using a raspberry pi for a stream solution connected to my NAS, and logitech squeezebox server etc...
Anyway i saw that jriver has released a solution for the newest pi-3, and was wondering if anyone here tries that with all the functionality.
Just my inputs Regards from Jesper
I agree that HDF makes more sense than MDF, Pantzerholz might even make more sense in some cases, but its all about choices. Most materials mentioned, including aluminium can be made to work, but all require different measures to make them perform the best they can.
We've had countless threads on materials, some make sense for use in the bass frequencies, other combinations do better in the midrange, I had to pick a compromise for the whole range. I do not regret my choices at all, the clean early waterfall plots back me up, it works quite satisfactory.
I did notice the Raspberry Pi version of JRiver, I'm kind of curious what it can and cannot do. I hope we will soon find out, I didn't read up on it yet. It would make for a nice, almost stand alone solution... I wouldn't want to have to give up my FIR and PEQ, my plugins and... ah well, I guess I'm asking a whole lot, better stick to my PC solution... 😀
We've had countless threads on materials, some make sense for use in the bass frequencies, other combinations do better in the midrange, I had to pick a compromise for the whole range. I do not regret my choices at all, the clean early waterfall plots back me up, it works quite satisfactory.
I did notice the Raspberry Pi version of JRiver, I'm kind of curious what it can and cannot do. I hope we will soon find out, I didn't read up on it yet. It would make for a nice, almost stand alone solution... I wouldn't want to have to give up my FIR and PEQ, my plugins and... ah well, I guess I'm asking a whole lot, better stick to my PC solution... 😀
I think this may have come up before, but what type of software would you all recommend for cabinet design? I am able to do some basic 2D work in AutoCAD, but 3D is we'll beyond my level in AutoCAD. Do any of you know any 3D rendering applications that are relatively easy to learn? I am anxious to get started on my design.
As for construction, I am really taken by the rib construction design of the Gauder Akoustic speakers referenced earlier. I'm thinking of doing my 2-ways by bonding 3 or 4 layers of 3/4" Baltic birch for each rib section and then using perhaps 6 steel rods to bolt each of these rib sections, along with the top and bottom layers together, with a gasket between each section. I gather this will form the constrained layer construction discussed earlier. Are there any suggestions for gasket materials? Perhaps something like a layer of 1/8" mass loaded vinyl?
For the a Baffle, I'm leaning toward a Corian type composite material. I'm also thinking of layering this with a gasket in between for both structure and to hide bolt heads. I think it might look great too, the exposed Baltic birch layers with black gasket lines against a black Corian baffle. Matching style stands would round out the package.
As for construction, I am really taken by the rib construction design of the Gauder Akoustic speakers referenced earlier. I'm thinking of doing my 2-ways by bonding 3 or 4 layers of 3/4" Baltic birch for each rib section and then using perhaps 6 steel rods to bolt each of these rib sections, along with the top and bottom layers together, with a gasket between each section. I gather this will form the constrained layer construction discussed earlier. Are there any suggestions for gasket materials? Perhaps something like a layer of 1/8" mass loaded vinyl?
For the a Baffle, I'm leaning toward a Corian type composite material. I'm also thinking of layering this with a gasket in between for both structure and to hide bolt heads. I think it might look great too, the exposed Baltic birch layers with black gasket lines against a black Corian baffle. Matching style stands would round out the package.
I know a lot of people use SketchUp over here, worth a shot. Though Autocad is 3D capable, it certainly isn't the easiest program to use for 3D drawings.
As I come from a mechanical design background I'm used to Autodesk's Inventor, but that's a pretty expensive package.
The Mass loaded vinyl I used in my project wasn't the most flexible type I encountered, I wouldn't recommend it as a gasket material, Once deformed it didn't return to the original shape when the pressure was taken off of it. I'd look for something that stays flexible over time, preferably with some weight to it. I cannot say I've come across a suitable rubber yet I'd recommend. Perhaps Kindhornman can recommend something? He's quite at home in various materials.
I'm sure it could look pretty, I can't say much useful about a Corian baffle, but I'd make sure to use damping there too. Its probably a stiff material with resonances up higher in frequency than any wood type material.
As I come from a mechanical design background I'm used to Autodesk's Inventor, but that's a pretty expensive package.
The Mass loaded vinyl I used in my project wasn't the most flexible type I encountered, I wouldn't recommend it as a gasket material, Once deformed it didn't return to the original shape when the pressure was taken off of it. I'd look for something that stays flexible over time, preferably with some weight to it. I cannot say I've come across a suitable rubber yet I'd recommend. Perhaps Kindhornman can recommend something? He's quite at home in various materials.
I'm sure it could look pretty, I can't say much useful about a Corian baffle, but I'd make sure to use damping there too. Its probably a stiff material with resonances up higher in frequency than any wood type material.
As for construction, I am really taken by the rib construction design of the Gauder Akoustic speakers referenced earlier. I'm thinking of doing my 2-ways by bonding 3 or 4 layers of 3/4" Baltic birch for each rib section and then using perhaps 6 steel rods to bolt each of these rib sections, along with the top and bottom layers together, with a gasket between each section. I gather this will form the constrained layer construction discussed earlier. Are there any suggestions for gasket materials? Perhaps something like a layer of 1/8" mass loaded vinyl?
Somehow this part did not sit well with me and stayed on my mind....
Consider a pressure build-up in a speaker, Now place a double wall at the outside, with a flexible layer glued between them. Once the pressure wants to move/vibrate the inner wall, the flexible layer is holding it back due to the shear load on the flexible layer:

Like the situation at the right of this picture I posted earlier:
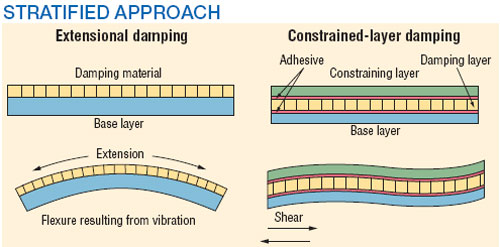
Now picture the Birch ply stacks, with a gasket in between and the same pressure build up in the closed back chamber, again trying to move/vibrate the wall:

You could still call it a shear load, but do you see the difference? The gasket itself is under load and the pressure build up will try to bulge the walls, including the gasket. Only the vertical pressure on that gasket is holding it in place. (and the glue of coarse) It will still damp somewhat, depending on that vertical pressure, but it would also mean the pressure being different due to humidity changes (wood contracting or expanding).
So I wouldn't call this a constrained layer construction. You might have figured this out already, but it didn't sit well with me, I had to mention it...
I see your concern. Perhaps the thickness of the wall would counteract this factor. I'm considering sidewalls of about 50mm with 6 threaded rods holding the body together. Wouldn't the highly compressed, 50mm wide, mass loaded vinyl in the sidewall layer more than offset this acoustic pressure while still providing expansion room for the wood? It also adds a level of modularity that would be lost by gluing it all together.
Thanks for the recommendation on SketchUp, it is exactly what I need. What an incredible application! I've been studying the tutorials and with my basic knowledge of AutoCAD, this should be quite easy. I look forward to working up my renderings. I definitely want to have very solid designs before starting. I'll post them once they are ready.
On the templates, do you think they can be effectively cut by hand into perhaps 1/4" thick aluminum? Is 1/4" thick enough? Are the trimming bits flush with the template so that the template should be cut to the exact dimensions of the desired layers?
Thanks for the recommendation on SketchUp, it is exactly what I need. What an incredible application! I've been studying the tutorials and with my basic knowledge of AutoCAD, this should be quite easy. I look forward to working up my renderings. I definitely want to have very solid designs before starting. I'll post them once they are ready.
On the templates, do you think they can be effectively cut by hand into perhaps 1/4" thick aluminum? Is 1/4" thick enough? Are the trimming bits flush with the template so that the template should be cut to the exact dimensions of the desired layers?
- Home
- Loudspeakers
- Full Range
- The making of: The Two Towers (a 25 driver Full Range line array)